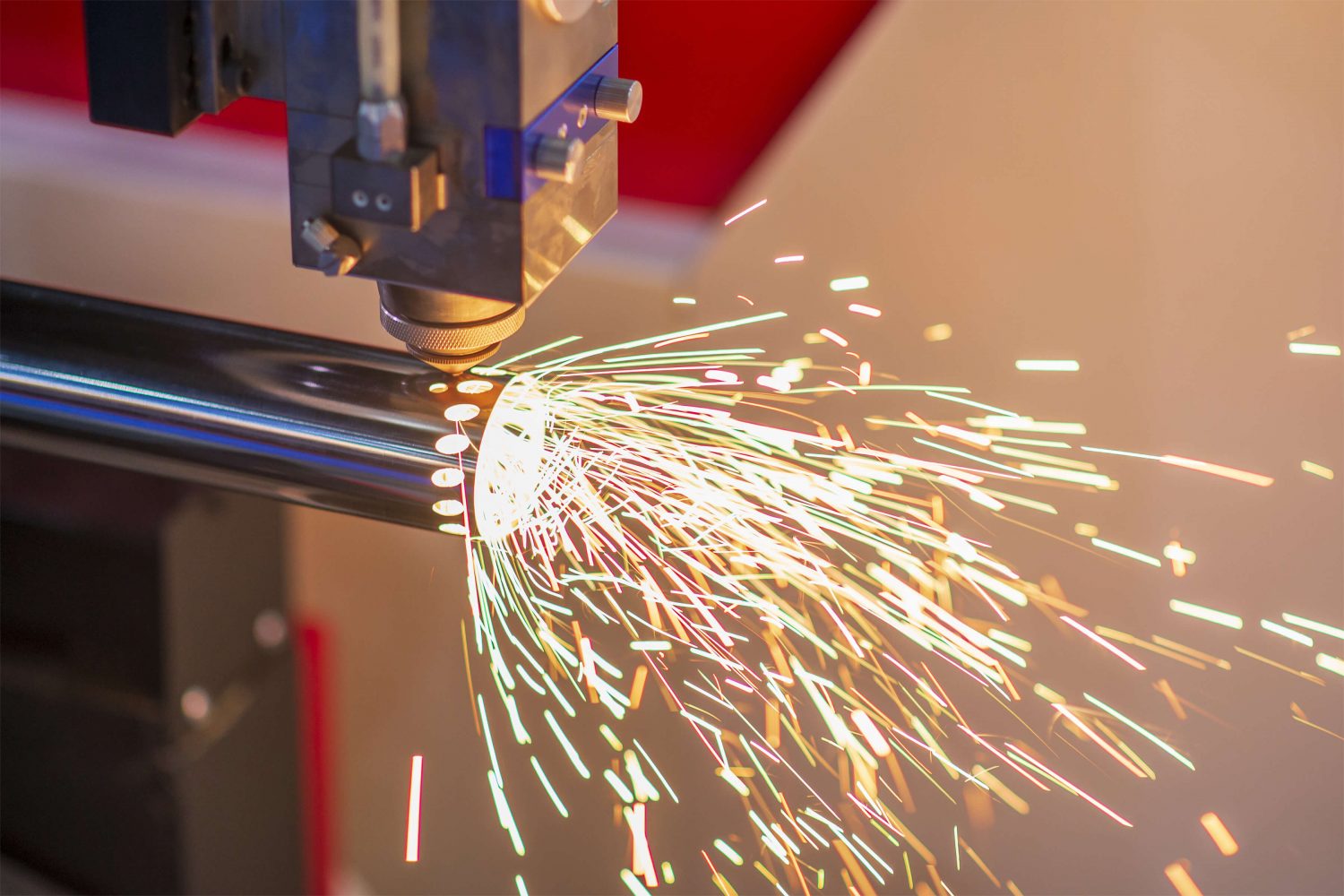
Obróbka metali i stali
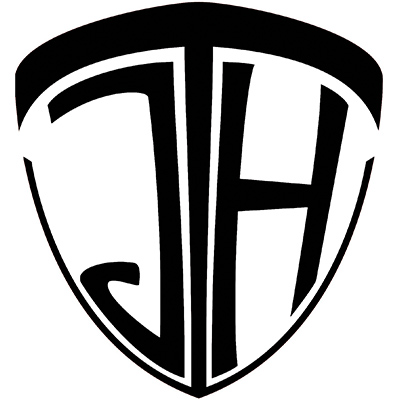
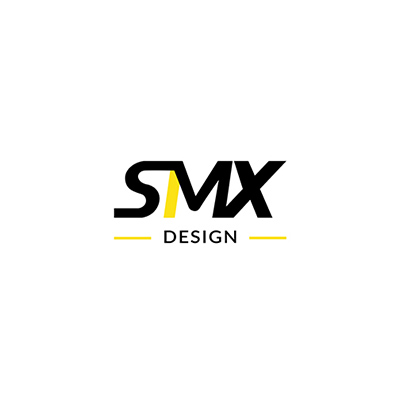
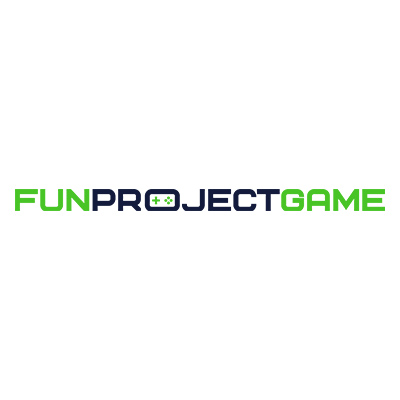
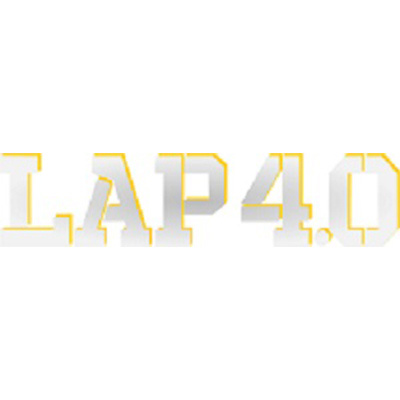
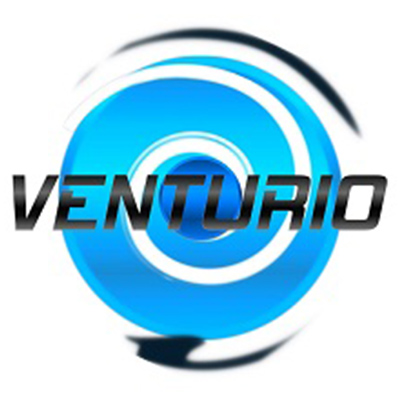

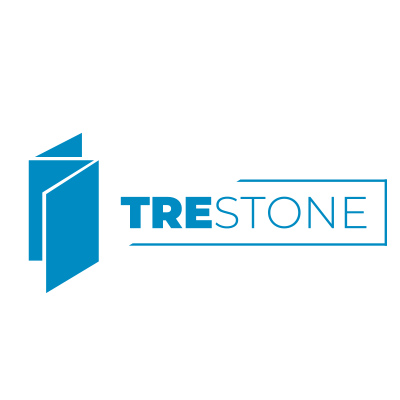
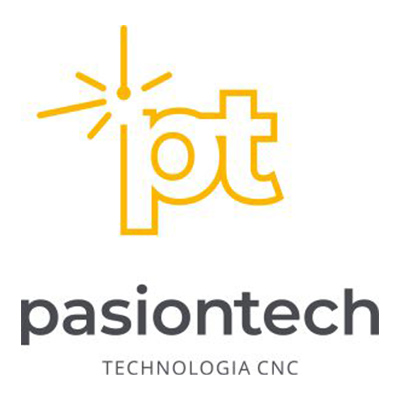
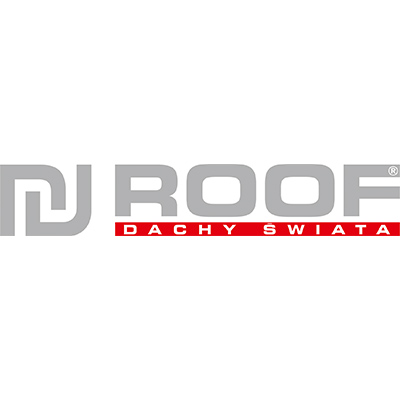
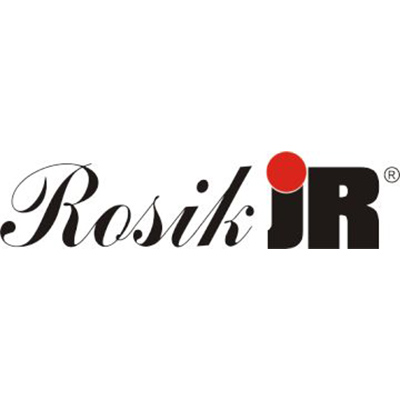
Czym jest obróbka metali i stali?
Tak bardzo ogólnie można powiedzieć, że obróbka metali i stali są to wszelkie procesy związane ze zmianą kształtów, wymiarów oraz właściwości fizycznych lub chemicznych różnego rodzaju metali. Dochodzi do tego wskutek użycia odpowiednich technologii. Są to rozwiązania szczególnie popularne w zakładach przemysłowych.
Obróbka metali i stali – podstawowe metody i procesy obróbki metali.
Obróbka metali i stali wykonywana może być w różnorodny sposób. Najpopularniejszymi metodami obróbki są:
- obróbka skrawaniem,
- obróbka plastyczna,
- obróbka cieplna metali,
- chemiczna obróbka metali.
Obróbka skrawaniem.
Obróbka skrawaniem stali (czy obróbka skrawaniem metali kolorowych) to jeden z najpopularniejszych rodzajów obróbki metali. Jak sama nazwa wskazuje – poprzez skrawanie, czyli fragmentaryczne pozbywanie się części materiału za pomocą specjalnych narzędzi, nadaje się przedmiotom odpowiedni kształt, wymiar, jakość. Krótko mówiąc, chodzi o: frezowanie, toczenie, szlifowanie, struganie.
Frezowanie.
Frezowanie jest jednym ze sposobów obróbki skrawaniem, polegającym na użyciu wieloostrzowego narzędzia na frezarce. Obrabiarka zapewnia ruch obrotowy, a ruch posuwowy zarezerwowany jest dla przedmiotu poddanego modyfikacji. Z uwagi na różnorodne położenie osi ustalonego frezu (czyli narzędzia do obróbki) wyróżnić można: frezowanie obwodowe i czołowe, współbieżne i przeciwbieżne oraz inne.
Toczenie.
Toczenie to kolejna z metod obróbki skrawaniem, realizowana przy użyciu tokarek. Ruch główny obrotowy wykonywany jest przez obrabiany przedmiot, z kolei prostoliniowy ruch posuwowy wykonywany jest przez narzędzie skrawające. Proces ów stosuje się zazwyczaj do obróbki elementów przypominających bryły obrotowe, czyli przedmiotów o kształtach walcowatych, kulistych czy stożkowych i polega na nadawaniu im konkretnego kształtu na skutek odcinania kolejnych warstw za pomocą noża tokarskiego.
Szlifowanie.
Szlifowanie jest rodzajem obróbki ściernej przy pomocy narzędzi umiejących zetrzeć metal, czyli np. ściernicy, taśmy ściernej, osełki itd. W jakich rodzajach stali jest to przydatna obróbka? Chodzi o przedmioty hartowane, kute, walcowane, odlewane – a szlifowanie wykonywane jest w celu ich wykończenia. Podczas tego procesu dochodzi do precyzyjnej obróbki materiałów stalowych oraz nieinwazyjnego konstrukcyjnie zdzierania warstwy wierzchniej z materiałów poddanych obróbce.
Struganie.
Struganie to sposób obróbki, w którym zarówno ruch narzędzia, jak i obrabianego przedmiotu są ruchami prostoliniowymi. Z uwagi na to, czy ruchem głównym jest ruch narzędzia, czy przedmiotu, rozróżnia się struganie poprzeczne i wzdłużne.
Obróbka plastyczna.
Obróbka plastyczna to rodzaj obróbki pozwalający na kształtowanie, dzielenie, zmianę struktury, gładkości powierzchni czy właściwości fizykochemicznych materiałów. Może się to odbywać na zimno albo na gorąco. Głównymi metodami obróbki plastycznej są: kucie, tłoczenie, ciągnienie, gięcie, walcowanie, wyciskanie.
Kucie.
Kucie służy polepszeniu właściwości mechanicznych materiału lub nadaniu materiałom określonego kształtu poprzez zginanie, nacisk, zgniatanie lub uderzanie. Wykonuje się je na gorąco lub na zimno, ręcznie albo mechanicznie – na prasach lub kuźniarkach. Kucie swobodne stosowane jest w produkcji jednostkowej lub małoseryjnej, a matrycowe – w produkcji wieloseryjnej.
Tłoczenie.
Tłoczenie też wykonuje się przy użyciu pras, na zimno lub gorąco, i odbywa się głównie na blachach, taśmach, płytach albo foliach. Kształt, jaki chcemy uzyskać, dokonuje się poprzez cięcie (wycinanie, przecinanie, rozcinanie, odcinanie, okrawanie, dziurkowanie, przetłaczanie) lub na skutek innych form plastycznego ukształtowania bez zmian w spójności materiału (zawijanie, wyginanie, profilowanie, skręcanie, przetłaczanie, wygniatanie, wywijanie, obciąganie, obciskanie).
Ciągnienie.
Ciągnienie to proces kontrolowanego wydłużania materiału przy jednoczesnym zmniejszaniu jego przekroju poprzecznego (średnicy). W ten sposób obrabiane mogą być druty, rury, pręty, a metodę stosuje się na zimno lub na gorąco.
Gięcie.
Gięcie polega na zmianie krzywizny materiału, bez naruszania jego wymiarów poprzecznych. Proces może być wykonany na zimno lub poprzedzony obróbką hydrotermiczną, mającą zwiększyć skłonności materiału do odkształcenia. Możemy więc wyróżnić gięcie metali tłocznicze albo kuźnicze.
Walcowanie.
Walcowanie polega na zgniataniu materiału przez napędzane walce, tarcze, rolki lub przemieszczające się względem siebie narzędzia płaskie. Wykonuje się je na zimno, na ciepło, na gorąco. Można w ten sposób kształtować takie wyroby hutnicze, jak: pręty, kształtowniki, blachy, rury, wyroby osiowo-symetryczne. Sposobów jest wiele: walcowanie wzdłużne, poprzeczne, poprzeczno-klinowe, pielgrzymowe, kuźnicze, skośne, jednoliniowe, wieloliniowe, ciągłe, półciągłe, mijane, szachownicowe.
Wyciskanie.
O wyciskaniu mówimy wtedy, gdy materiał znajduje się w pojemniku nazywanym recypientem, a kształtuje się go, wyciskając go z matrycy (pod naciskiem stempla). Aby zachować duże odkształcenia, materiały miękkie (takie jak np. czyste aluminium) wyciska się na zimno, ale przy pozostałych materiałach, stosuje się wyciskanie na gorąco (aby narzędzia wytrzymały tak znaczne siły i obciążenia). Wśród rodzajów wyciskania mamy: współbieżne, przeciwbieżne, złożone, hydrostatyczne, z bocznym wypływem materiału.
Obróbka cieplna metali.
Obróbka cieplna metali to zabieg bądź szereg zabiegów termicznych, mających na celu zmianę struktury stopów. Prościej mówiąc – stosując ten rodzaj obróbki, zmieniamy stan stały obrabianego stopu, a jednocześnie jego właściwości fizyczne, chemiczne, mechaniczne. Polega to na odpowiednim nagrzewaniu, wygrzewaniu i chłodzeniu materiałów metalowych do zadanych temperatur i z określoną szybkością, co powoduje zmiany właściwości stopu w stanie stałym. Najczęściej obrabianym w ten sposób metalem jest stal, charakteryzująca się wyjątkową skłonnością i podatnością na modyfikację.
Podział obróbki cieplnej.
Podział obróbki cieplnej kształtuje się następująco:
- obróbka cieplna zwykła: wyżarzanie, hartowanie i odpuszczanie (ulepszanie cieplne, utwardzanie cieplne), przesycanie i starzenie (utwardzanie wydzieleniowe),
- obróbka cieplno-plastyczna: niskotemperaturowa, wysokotemperaturowa, z przemianą izotermiczną,
- obróbka cieplno-chemiczna: nasycanie jednym lub wieloma pierwiastkami,
- obróbka cieplno-magnetyczna.
Obróbka chemiczna.
Obróbka chemiczna to rodzaj obróbki metali polegający na chemicznym bądź fizykochemicznym oddziaływaniu na ich powierzchnię, co ma na celu powstanie określonej powłoki ochronnej, która ma zabezpieczać przed korozją i zwiększać ich wytrzymałość. Czyni się to poprzez: nawęglanie, węgloazotowanie (cyjanowanie), chromowanie, azotowanie, naborowywanie, kaloryzowanie, nasiarczanie, nakrzemowanie, metalizowanie dyfuzyjne.
Obróbka metali i stali – metody.
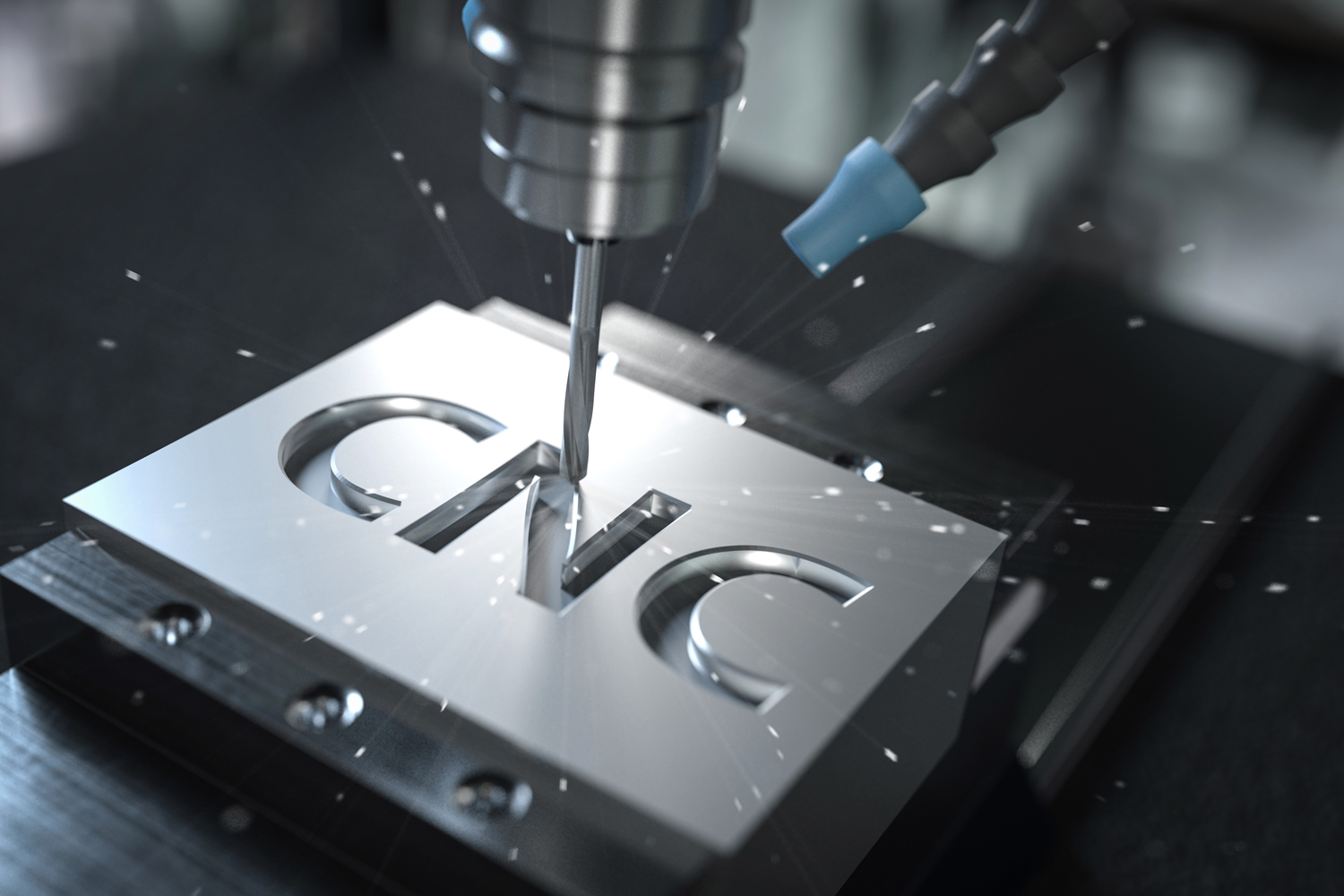
Oprócz wymienionych wyżej sposobów na obróbkę metali, występuje cały szereg innych. U nas zamówisz między innymi:
Laserowe cięcie blach.
Laserowe cięcie blach – rodzaj obróbki, podczas której na niewielkiej przestrzeni zostaje rozprowadzona – przy użyciu wiązki laserowej – duża ilość energii. Cięcie laserowe polega na punktowym wprowadzeniu energii pod postacią wysokoenergetycznego strumienia tnącego – a więc gorącego promienia lasera – otoczonego gazem technicznym o dużej czystości, innym w zależności od ciętego materiału. Przeprowadza się je na trzy sposoby – najczęściej w różnych kombinacjach – metodą spalania, stapiania lub sublimacji. Jedną z zalet laserowego wycinania jest szeroki zakres materiałów poddających się procesowi cięcia – obróbce poddawać można właściwie wszystkie rodzaje blach, przy czym znaczenie ma grubość blach i strefa cięcia (co zależne jest od posiadanego przez zakład parku maszynowego). Laserowe cięcie wykorzystywane jest w branżach: przemysłowej, motoryzacyjnej, budowlanej, automatyzacyjnej i wielu innych.
Laserowe cięcie rur i profili.
Laserowe cięcie rur i profili – można powiedzieć, że w pewnym sensie ma przewagę nad cięciem w blachach, bo bazuje się przy tym na półprodukcie bardziej przetworzonym niż blachy, dlatego nawet stosunkowo niewielka ilość obróbki laserowej może wygenerować gotowy produkt, niewymagający dalszej obróbki, a jego cena powinna być niższa od produktu z blachy. Obrobione laserowo rury i profile znajdują swoje zastosowanie w branży motoryzacyjnej, budowie pojazdów użytkowych, maszyn rolniczych, projektowaniu mebli, regałów sklepowych, przyrządów fitness, w architekturze, petrochemii; są częściami składowymi konstrukcji maszyn i urządzeń, konstrukcji nośnych, ram, podpór, rurociągów, rozmaitych wyrobów metalowych. Wycinanie w profilach pozwala na wielką kreatywność i otwiera ogrom możliwości w obszarze techniki wytwórczej: można wycinać dowolne typy – prostokątne, kwadratowe, okrągłe, owalne, w kształcie liter (przekroje otwarte H, L, T, U) – zachowując przy tym wysoką jakość i regularność krawędzi. Wszystko przy zachowaniu niezwykłej precyzji, dzięki której późniejszy montaż wyciętych elementów przebiega sprawnie, zapewniając dokładne połączenie wszystkich części.
Cięcie wodą.
Cięcie wodą – znane także pod wieloma innymi nazwami, jak: cięcie strumieniem wody, obróbka strumieniowo-ścierna, obróbka hydro-ścierna, obróbka wodno-ścierna, obróbka hydro-abrazyjna, abrasive waterjet (AWJ), waterjet – jest technologią rozdzielania lub przecinania materiałów za pomocą wody pod bardzo wysokim ciśnieniem. W przypadku cięcia grubszych i twardszych materiałów potrzebna będzie do tego celu woda z dodatkiem ścierniwa (garnetu). Wycinanie wodą pozwala na przebijanie prawie wszystkich rodzajów materiałów, daje więc możliwość wycinania z precyzją do 0,1 mm między innymi: stali, stali węglowej, nierdzewnej, narzędziowej, konstrukcyjnej, kwasoodpornej, Hardoxu i wielu innych jej rodzajów, ponadto także metali kolorowych i ich stopów, jak: miedź, aluminium, mosiądz, brąz, inne.
Cięcie plazmą.
Cięcie plazmą – jest procesem, w którym źródłem ciepła jest silnie skoncentrowany łuk elektryczny o dużej energii kinetycznej, jarzący się pomiędzy ciętym materiałem a nietopliwą elektrodą, umieszczoną w uchwycie plazmowym. Odpowiednią koncentrację łuku otrzymuje się za pomocą dyszy plazmowej (dyszy tnącej). Jej zadaniem jest koncentracja ciepła na niewielkiej powierzchni materiału, co powoduje znaczny wzrost stopnia jonizacji przepływającego gazu plazmowego. Chłodzone ścianki dyszy powodują zawężanie kolumny łuku, a dzięki dużemu zagęszczeniu mocy wytwarza się uformowany strumień plazmy, który ze względu na temperaturę sięgającą kilkunastu tysięcy stopni Celsjusza oraz dużą prędkość z łatwością przetapia i przedmuchuje metal, wyrzucając materiał ze szczeliny cięcia. Cięcie plazmą to metoda ekonomiczna i dobra jakościowo dla materiałów ze stali konstrukcyjnej o grubości poniżej 30 mm, stali stopowej i kolorówki. Plazmą można ciąć blachy, kształtowniki, rury oraz siatki.
Cięcie gazem.
Cięcie gazem (tlenowe) – usługa ta zwana bywa nieraz także cięciem płomieniowym i dzieli się na następujące etapy: rozgrzanie metalu do temperatury zapłonu, utlenienie, wydmuchanie za pomocą tlenu pod wysokim ciśnieniem. Można do tego celu używać propanu, acetylenu, propylenu i gazu ziemnego. Najlepiej w ten sposób tnie się materiały, w których zapłon odbywa się w temperaturze niższej niż wynosi jego temperatura topnienia, a topnienie powstających tlenków w temperaturze niższej niż zapłon.
Wykrawanie.
Wykrawanie (sztancowanie) – polega na wycinaniu z blachy określonego kształtu przy pomocy specjalnego stempla (wykrojnika). Proces najczęściej odbywa się przy wykorzystaniu pras mechanicznych i mimośrodowych. Podstawowe operacje cięcia za pomocą wykrojników to: wycinanie, dziurkowanie, odcinanie, przycinanie, nadcinanie, okrawanie, rozcinanie. Można w ten sposób nadawać detalom kształty wewnętrzne, zewnętrzne, wykrawać różne otwory.
Grawerowanie i znakowanie laserem.
Grawerowanie i znakowanie laserowe – są to sposoby bezdotykowego oznaczania rozmaitych wyrobów, opakowań czy etykiet informacjami typu: data przydatności, kod kreskowy, numer seryjny lub katalogowy, logo, różnego rodzaju napisy, grafiki, rysunki, zdjęcia. Techniki te wykorzystywane są przez wszystkie w zasadzie branże, a zastosowania użytkowe rozciągają się od znakowania przemysłowo wytwarzanych serii produktów (w celu zapewnienia ich identyfikowalności) po personalizację artykułów promocyjnych (poprzez umieszczenie znaków firmowych, nazw itd.). Trzeba tu zaznaczyć, że znakowanie laserowe jest terminem ogólnym, używanym w odniesieniu do takich procesów jak: grawerowanie laserowe, polerowanie, ablacja, wyżarzanie, wypalanie laserowe. Podczas grawerowania promień lasera usuwa materiał, a w przedmiocie obrabianym powstaje zagłębienie – grawerunek, którego głębokość zależna jest od parametrów obróbki. Grawerowanie jest wykonywane głównie na stali nierdzewnej, stalach stopowych i innych metalach.
Elektrodrążenie.
Elektrodrążenie (obróbka elektroerozyjna) – obróbka ubytkowa, oparta na wykorzystaniu erozji towarzyszącej wyładowaniom elektrycznym pomiędzy elektrodą i materiałem w środowisku dielektryka.
Wykorzystywane jest to w sytuacjach, gdy parametry produktu uzyskiwane prostszymi metodami obróbki ubytkowej są niewystarczające, a więc przy detalach o skomplikowanej budowie, przy metalach trudnych do obróbki oraz tych wymagających wysokiej precyzji wykonania.
Gięcie rur, profili, płaskowników.
Gięcie rur, profili, płaskowników – wykonuje się, gdy montaż rur czy profili w pierwotnej formie, o standardowych wymiarach i długościach dostępnych w ofercie handlowej producentów, nie jest możliwy i trzeba je poddać dodatkowej obróbce, jaką jest gięcie do wymaganej formy. Polega to na trwałej zmianie krzywizny przedmiotu obrabianego. Podczas gięcia następuje zmiana kształtu przekroju poprzecznego elementu giętego, spowodowana zwiększaniem się wymiarów poprzecznych warstw ściskanych oraz zmniejszaniem się wymiarów warstw rozciąganych. Odbywa się ono na: prasach (w tym: krawędziowych), wzorniku (szablonie), walcach, giętarce trzpieniowej do rur i profili, jako kształtowanie taśm krążkami.
Gięcie drutu.
Gięcie drutu – polega na odkształcaniu drutu poprzez jego wyginanie w trzech płaszczyznach do odpowiedniego kąta nachylenia, dzięki czemu prosty odcinek drutu – poddany odpowiedniemu naciskowi – zostaje przekształcony w przestrzenny element (tj. gotowy produkt wykonany z drutu).
Gięcie sprężyn.
Gięcie sprężyn – jest wieloetapowym procesem, wykonywanym przy użyciu specjalistycznych maszyn. Materiałem bazowym jest prosty stalowy drut, montowany w maszynie, która go zwija w specjalistyczny sposób. Następnie – w procesie odpuszczania, z udziałem wysokiej temperatury w specjalnym piecu – uzyskuje on mechaniczne właściwości (nadające trwałość). Później przychodzi pora na kulowanie, mające uodpornić sprężynę na wszelkiego rodzaju pęknięcia poprzez celowanie w jej powierzchnię dużym strumieniem małych kulek. W kolejnych krokach ugina się ją (celem uzyskania deformacji, aby podczas eksploatacji „nie osiadała”) i maluje (aby zapobiec korozji), a na końcu poddaje testom i kontroli.
Nitowanie.
Nitowanie – jest techniką łączenia metalowych elementów konstrukcyjnych za pomocą szczelnych, stabilnych i trwałych połączeń w postaci nitów (niewielkich rozmiarów metalowych elementów w formie walca). Metoda ta sprawdzi się wszędzie tam, gdzie z różnych przyczyn nie sprawdzi się spawanie (np. przy łączeniu elementów drobnych oraz konstrukcji ze stopów aluminiowych na zimno). Maszyny nitujące sterowane numerycznie zapewniają dowolnie programowalne punkty nitowania (co przekłada się na doskonałą precyzję całej konstrukcji) i pozwalają na kontrolę wszystkich mierzalnych parametrów połączenia nitowego, w tym: długości drogi, siły nacisku i czasu nitowania.
Gwintowanie.
Gwintowanie – polega na tworzeniu gwintów wewnątrz i na zewnątrz metalowego produktu na drodze obróbki skrawaniem lub obróbki plastycznej. Można je wykonywać z zastosowaniem różnych technik i wykorzystaniem różnych maszyn CNC, jak: frezarki (frezy krążkowe i głowice frezowe), tokarki (narzynki, gwintowniki, noże lub głowice gwinciarskie), szlifierki (ściernice), wiertarki (gwintowniki).
Spawanie laserowe.
Spawanie laserowe – polega na stapianiu obszaru styku łączonych przedmiotów ciepłem otrzymanym w wyniku doprowadzenia do obszaru skoncentrowanej wiązki światła koherentnego o bardzo dużej mocy. Wiązka laserowa, przechodząc z lasera do przedmiotu spawanego przez system przesłon zwierciadeł i elementów optycznych, jest ogniskowana w obszarze spawania. Padając na powierzchnię metalu, ulega intensywnemu odbiciu, w zależności od rodzaju metalu i jego stanu powierzchni. Efektywność procesu zależy przede wszystkim od absorpcji energii wiązki laserowej przez powierzchnię spawanego przedmiotu, toteż ważne jest odpowiednie przygotowanie powierzchni przez zmatowienie lub poczernienie. Technika idealnie sprawdza się przy łączeniu niewielkich elementów cienkościennych, zalecana przy cieńszej stali, stali o wysokiej wytrzymałości i stali trudnościeralnej, wysoką wydajność odnosi w produkcji wielkoseryjnej (np. przemyśle motoryzacyjnym).
Spawanie zrobotyzowane.
Spawanie zrobotyzowane – opiera się na odpowiednio dobranym robocie spawalniczym i wysokiej klasy osprzęcie spawalniczym. Robot spawalniczy – pracując z przyrządami spawalniczymi – wykonuje spoiny po zaprogramowanych trajektoriach ruchu. Dzięki wykorzystaniu osi pomocniczych (jak: obrotniki spawalnicze czy przejazdy liniowe) można spawać detal w jednym mocowaniu, czego nie udałoby się wykonać przy spawaniu ręcznym. Możliwości robota spawalniczego pozwalają na wdrożenie różnych technologii i procesów. Mamy zatem aplikacje z procesami: MIG/MAG, TIG, CMT, lutospawaniem, spawaniem plazmowym, spawaniem laserowym, technologią TWIM (dwa palniki pracujące jednocześnie w spoinie).
Spawanie konstrukcji stalowych.
Spawanie konstrukcji stalowych – jest sposobem łączenia ze sobą elementów metalowych, podczas którego łączone materiały są rozgrzewane, przez co stapiają się ze sobą, tworząc trwałe połączenie. Najpopularniejszą techniką łączenia elementów z metalu przy budowie konstrukcji stalowych jest spawanie metodą MIG (zastosowanie gazu osłonowego obojętnego) i MAG (zastosowanie gazu osłonowego aktywnego). MIG/MAG jest sposobem odpowiednim do spawania np. stali węglowej czy chromowo-molibdenowej. Innym rozwiązaniem jest zastosowanie metody TIG.
Spawanie stali, metali, metali nieżelaznych.
Spawanie stali, metali, metali nieżelaznych – wykorzystywane jest przez najróżniejsze branże: budownictwo, hydraulikę, architekturę, elektronikę, branżę AGD, różne gałęzie przemysłu – przemysł ciężki, metalurgiczny, stoczniowy, hutniczy, samochodowy, lakierniczy, chemiczny, naftowy, farmaceutyczny, wojskowy, włókienniczy, celulozowo-papierniczy, spożywczy. Zakres zastosowań jest praktycznie nieograniczony: blachy, rury, płaskowniki, kątowniki, szyny, druty, pręty, liny, balustrady, kabiny wind, rury katalizatorowe i wydechowe, koła zębate, kadłuby silników, felgi, łożyska, napędy, głowice, części samochodowe, konstrukcje inżynierskie, motoryzacyjne, okrętowe i lotnicze, żurawie mobilne, maszyny rolnicze i leśnicze, rurociągi, transformatory, agregaty prądotwórcze, sondy hydrostatyczne, wkłady kominowe, pompy betonu, zbiorniki do produktów spożywczych, sprzęt AGD, armatura łazienkowa i kuchenna, gięte meble, profile drzwiowe, okienne i fasadowe, sprzęt dentystyczny i chirurgiczny, produkty ozdobne, użytkowe oraz do zastosowania specjalistycznego itd. W zależności od zastosowanego materiału oraz potrzeby można skorzystać z następujących metod: GTAW/TIG, MIG/MAG, PAW, GMAW, FCAW, LBW.
Wyoblanie.
Wyoblanie – to rodzaj plastycznej obróbki, wykorzystujący podatność materiałów do odkształceń (po przekroczeniu granicy plastyczności), bez przerwania ciągłości kształtowanej blachy, dzięki czemu z materiału wyjściowego uzyskujemy cienkościenną bryłę obrotową, niejednokrotnie o bardzo skomplikowanym kształcie, trudnym lub niemożliwym do osiągnięcia przy użyciu klasycznych metod tłoczenia. Wyoblarki umożliwiają realizację złożonego procesu technologicznego, na który składają się: wyoblanie, obcinanie, zawijanie obrzeża, wywijanie, zaginanie i łączenie.
Odlewy staliwne.
Odlewy staliwne – wykorzystywane są w maszynach budowlanych, rolniczych, urządzeniach dźwigowych i transportowych. Znajdują zastosowanie w przemyśle hutniczym, wydobywczym, maszynowym, energetycznym, cementowo-wapiennym, chemicznym, petrochemicznym, gazowym, morskim i spożywczym. Etapami odlewania są: przygotowanie materiałów formierskich, wykonanie formy odlewniczej i rdzeni odlewniczych, roztopienie i przygotowanie ciekłego metalu, wypełnienie nim formy, zakrzepnięcie metalu, usunięcie odlewu z formy, oczyszczenie jego powierzchni (piaskowanie, śrutowanie), usunięcie naddatków technologicznych (wlewów, nadlewów, przelewów), poddanie odlewów obróbce cieplnej, cieplno-chemicznej, cieplno-mechanicznej oraz innym zabiegom wykańczającym i polepszającym powierzchnię (jak: śrutowanie, malowanie, wygładzanie, polerowanie), ewentualna obróbka dodatkowa (np. rafinowanie).
Odlewy żeliwne.
Odlewy żeliwne – poprzez stosowanie różnego rodzaju dodatków odlewniczych oraz specjalistycznych technik można uzyskać żeliwo w 100% spełniające wymagania klienta. Popularne odmiany żeliwa to np. ni-hard czy ni-resist, które posiadają zwiększoną odporność na ścieranie. Dzięki dobrym właściwościom lejnym, odlewy mogą mieć skomplikowane kształty. Przykłady zastosowań odlewów żeliwnych: przemysł motoryzacyjny (np. obudowy skrzyni biegów, kadłuby silników, głowice, tarcze i bębny hamulcowe), przemysł kolejowy (wstawki hamulcowe), galanteria odlewnicza, mała architektura, odwodnienia liniowe, żeliwo budowlane, ogrodzenia, artykuły do ogrodu, inżynieria sanitarna (włazy kanałowe, rury, wpusty uliczne), wyposażenie kuchenne.
Anodowanie aluminium.
Anodowanie aluminium (eloksalacja) – jest procesem wytwarzania warstwy tlenku na powierzchni metalu, mającym wpłynąć pozytywnie na jego wytrzymałość, twardość, odporność na korozję, zarysowania i uszkodzenia mechaniczne. Pozwala to uatrakcyjnić wygląd, zwiększyć trwałość i czas użytkowania produktów. Ponadto poprawia to ich walory sanitarne, cechy kwalifikujące do kontaktu z żywnością, pozwala uzyskać nieprzewodzącą warstwę anodową (wykorzystywaną w elektronice) i chroni niektóre stopy aluminium przed korodowaniem w chlorkach (co wykorzystuje przemysł stoczniowy).
Złocenie.
Złocenie – to proces pokrywania powierzchni przedmiotu cienką warstwą złota lub malowanie przedmiotów farbą zawierającą pewną ilość sproszkowanego złota. Powłoki te charakteryzuje duża trwałość i odporność na korozję, a ich celem jest funkcja dekoracyjna, ochronna lub techniczna. Są różne rodzaje złocenia, m.in.: złocenie galwaniczne twarde w kąpielach kwaśnych, obróbka elektrolityczna twarda w kąpielach słabokwaśnych, obróbka elektrolityczna miękka, złocenie chemiczne, złocenie metodą tamponową.
Niklowanie.
Niklowanie – jest technologią pokrywania – w celach dekoracyjnych, antykorozyjnych lub technologicznych (jako podłoże dla innych technik galwanicznych) – wyrobów metalowych warstwą niklu. Dzięki temu wyroby zyskują estetyczny wygląd, wysoką odporność na czynniki zewnętrzne oraz lepszą przyczepność powłok wierzchnich.
Cynkowanie.
Cynkowanie – jest metodą pokrywania metalu cienką, wytrzymałą, odporną na uszkodzenia mechaniczne, ścieranie czy korozję zabezpieczającą powłoką cynku. Proces cynkowania znajduje swoje zastosowanie w wielu gałęziach przemysłu, m.in. w branży elektrycznej, motoryzacyjnej, lotniczej i budowlanej.
Miedziowanie.
Miedziowanie – jest procesem wytwarzania na powierzchni przedmiotów metalowych lub niemetalowych cienkich powłok miedzianych, a wszystko to w celach: dekoracyjnych, ochronnych, technicznych, galwanoplastycznych, naprawy i odnowy wyrobów, zwiększenia odporności korozyjnej, poprawy wyglądu wyrobu, redukcji kosztów obróbki galwanicznej.
Elektropolerowanie.
Elektropolerowanie – to profesjonalny i zaawansowany proces elektrochemiczny, którego celem jest doprowadzenie detalu o dowolnym kształcie do wysokiego połysku, porównywalnego do połysku lustrzanego. Używa się do tego celu kąpieli galwanicznej.
Malowanie proszkowe.
Malowanie proszkowe – jest sposobem malowania na sucho, albowiem w tym procesie nie używa się wody. Polega ono na nakładaniu naelektryzowanych cząstek farby proszkowej na powierzchnię przewodzącą np. metalu. Osadzona warstwa proszku utrzymuje się na powierzchni malowanego detalu dzięki siłom elektrostatycznym. Najpierw przygotowuje się element do malowania, później nanosi farbę, a na końcu utwardza ją. Metoda ta ma wiele zalet, takich jak: ekologiczność, niemalże pełne wykorzystanie materiału malarskiego, doskonały efekt wizualny, utworzenie powłoki antykorozyjnej na materiałach, oszczędności energetyczne.
Piaskowanie.
Piaskowanie – jest procesem oczyszczania powierzchni metali, mającym za zadanie zredukować wszelkie pojawiające się na metalu uszczerbki (zabrudzenia, rysy, utlenione warstwy, rdzę) i przedłużającym żywotność. Odbywa się to przy wykorzystaniu specjalistycznego urządzenia, zwanego piaskarką.
Odlewy kokilowe i piaskowe.
Odlewy kokilowe i piaskowe – jako usługi dostępne na naszej stronie. Odlewanie kokilowe to metoda odlewania do form trwałych (tzw. kokili). Proces prosty, niewymagający tworzenia na nowo matrycy (formy), gdyż formy te napełniane są metalem wielokrotnie. Dzięki tej metodzie można uzyskać przedmioty spełniające wymagania klienta pod względem rozmiaru, kształtu, wagi oraz gładkości powierzchni, dlatego chętnie korzystają z niej przedsiębiorstwa zajmujące się produkcją seryjną: elementów maszyn, niewielkich przedmiotów, precyzyjnych części do napędu, lekkich konstrukcji, armatury o właściwościach geoszczelnych i cieczoszczelnych. W przypadku niewielkich partii stosuje się najczęściej odlewanie przy zastosowaniu form piaskowych. Jest to zaawansowany technologicznie proces, w którym w pierwszym etapie tworzy się formy lub modele z masy piaskowej, wyposażone w rdzeń odlewniczy, a następnie zalewa się je metalem w formie ciekłej o ściśle określonych właściwościach. W celu osiągnięcia precyzji finalnego kształtu, elementy po wyjęciu z formy poddaje się dalszej obróbce.
Wybijanie w blachach.
Wybijanie w blachach – jest alternatywą dla wiercenia, wypalania i frezowania. W procesie tym tworzy się otwory, przeprowadzając cięcie materiału za pomocą stempla i matrycy. Podczas procesu wybijania stempel wchodzi w materiał, powodując pęknięcie w nim. Kształt pęknięcia zależny jest od wielkości odstępu pomiędzy stemplem a matrycą. Wybijanie otworów w blachach ma zastosowanie w prefabrykacji stali dla konstrukcji stalowych, podkonstrukcji, otworów do podstaw świetlików i klap dymowych, a także elementów do rusztowań, regałów wysokiego składowania, podzespołów do maszyn rolniczych i wielu innych. Wybijać można także znaki, numery, litery itd.
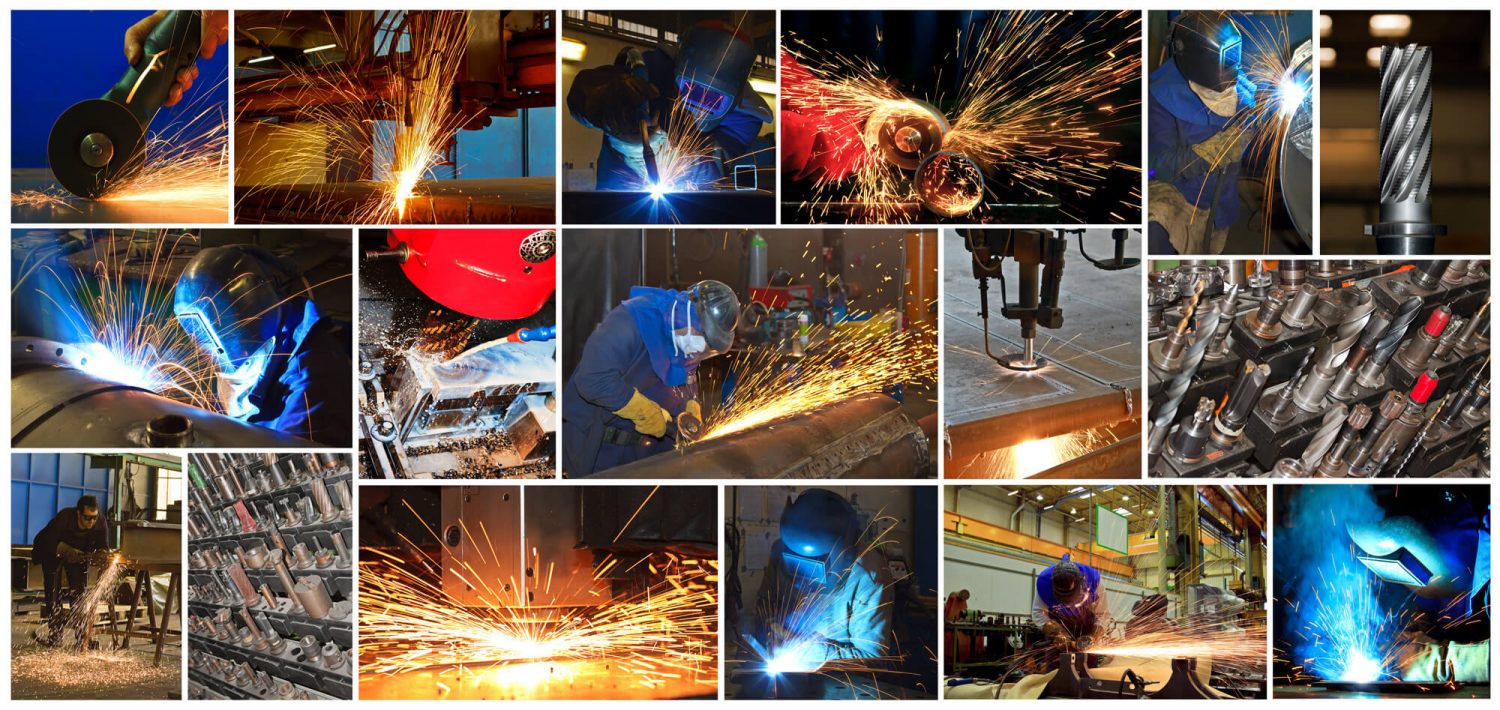
Potrzebujesz wykonać inną usługę obróbki metali? Skontaktuj się z nami, nasi Partnerzy z pewnością będą mogli pomóc Ci także w inny sposób.
Obróbka metali i stali – współpraca.
Kogo zapraszamy do współpracy w zakresie obróbki metali i stali?
Obsługujemy od Klientów indywidualnych po duże koncerny – do każdego zlecenia podchodzimy z takim samym zaangażowaniem. Od produkcji jednostkowej po wieloseryjną – u nas zrealizujesz każdą usługę CNC w każdym materiale.
Można powiedzieć, że obróbka metali i stali nie ma przed nami żadnych tajemnic. Tniemy laserem, plazmą, tlenem, wodą, grawerujemy, znakujemy i działamy na dziesiątki innych sposobów. Wykrawarki, elektrodrążarki, giętarki, prasy krawędziowe, frezarki, tokarki, centra obróbcze CNC, szlifierki, nitownice, gwintownice, spawarki, walcarki, wybijarki, kabiny do malowania proszkowego i wiele, wiele więcej – to to, co możemy zaoferować naszym Klientom. Usługi realizujemy kompleksowo, w optymalnych terminach, atrakcyjnych cenach i najwyższej jakości.
W ramach kategorii obróbka metali i stali pracujemy na szerokiej gamie materiałów, między innymi: stal konstrukcyjna, szlachetna, czarna, węglowa, nierdzewna, kwasoodporna, narzędziowa, galwanizowana, ocynkowana, Hardox, aluminium, mosiądz, miedź.
Z naszych usług korzysta wiele firm z najróżniejszych dziedzin przemysłu, takich jak: metalurgia, energetyka, górnictwo, gospodarka komunalna, branża motoryzacyjna, lotnicza, stoczniowa, petrochemiczna, maszynowa, budowlana, meblarska i wiele, wiele innych. Każdy znajdzie u nas coś dla siebie.
Zleć obróbkę metali i stali.
Dla Twojej wygody stworzyliśmy niezwykłe miejsce, w którym skupiliśmy – w ogólnopolskiej sieci partnerskiej – szereg firm produkcyjnych, zajmujących się profesjonalną obróbką materiałów, w tym metali.
Obróbka stali realizowana jest w naszym portalu przez podmioty produkcyjne dysponujące specjalistycznymi parkami maszynowymi oraz wiedzą i umiejętnościami wykwalifikowanych specjalistów z branży metalowej. W związku z tym, że posiadamy do dyspozycji najnowocześniejsze, innowacyjne technologie CNC, nie ma dla naszych Partnerów (z całej Polski) zadań niemożliwych do zrealizowania. Sprzęt oraz wiedza naszych Partnerów od obróbki metali pozwalają przetworzyć w zaawansowanych procesach technologicznych większość dostępnych na rynku materiałów. Dzięki temu z nami wyprodukujesz, co tylko będziesz chciał! Posiadamy wszystko, co konieczne, aby zaoferować Ci usługi obróbki metali na najwyższym poziomie. Możesz polegać na doświadczeniu naszych Partnerów!
Pozostałe tagi: obróbka powierzchni metali, utwardzanie cieplne metali, obróbka stali Hardox, kokile żeliwne i stalowe Poznań.