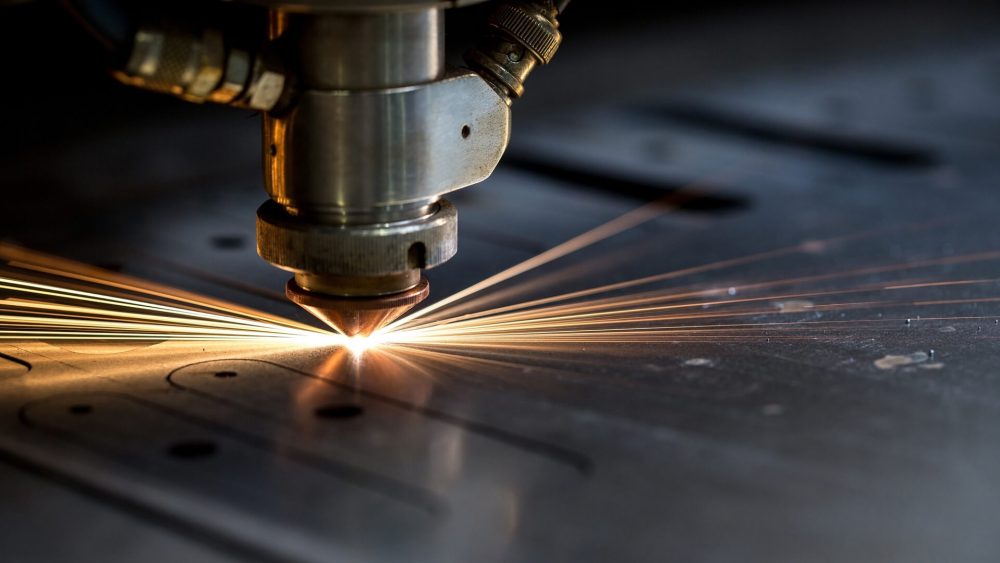
Cięcie CNC
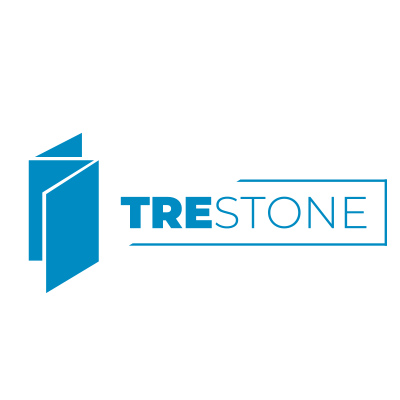
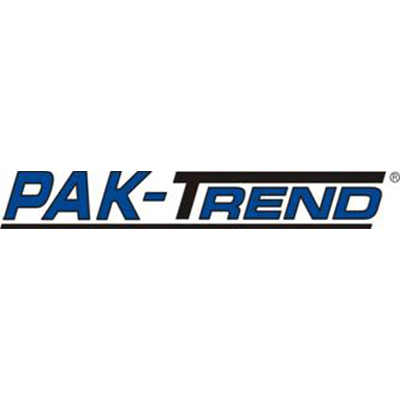
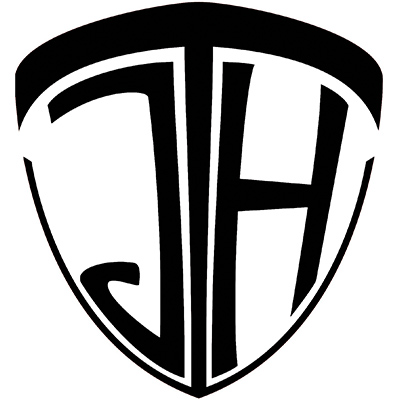
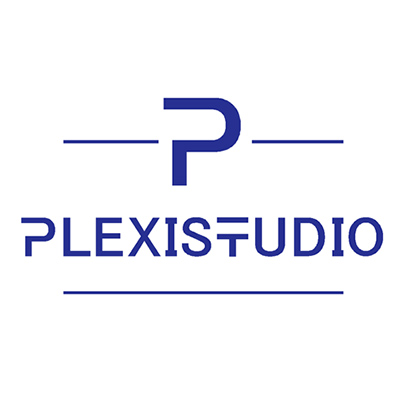
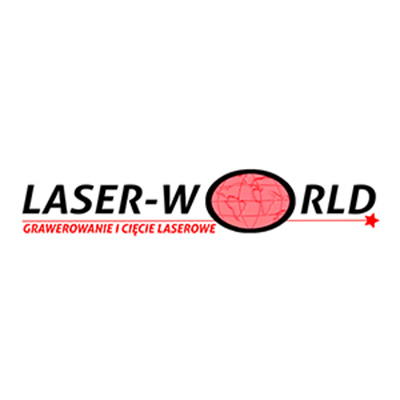
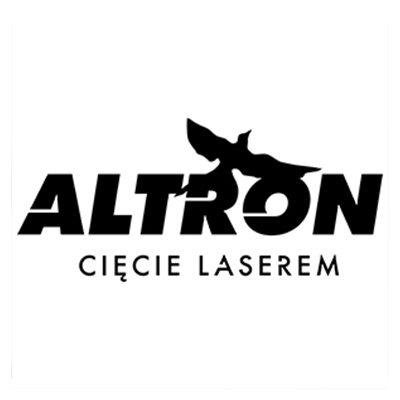
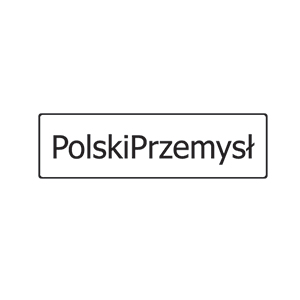
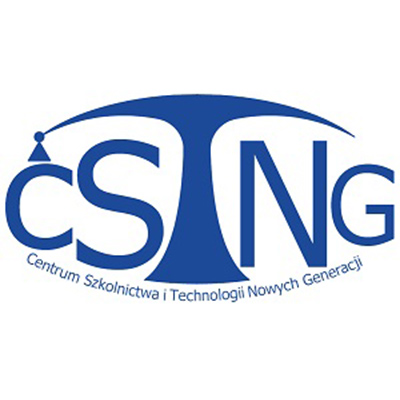
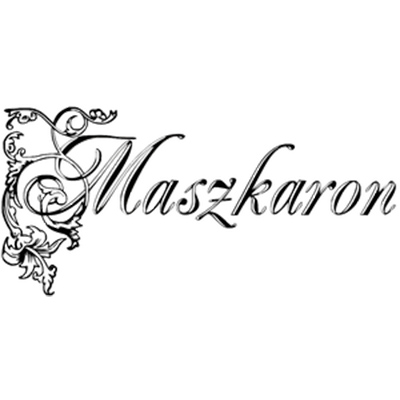
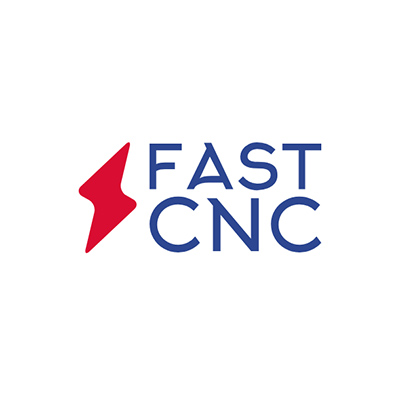
Cięcie CNC jest dziś wiodącą technologią w masowej obróbce i szturmem zdobywa wciąż nowe rynki i znajduje nowe zastosowania. Wiodące rozwiązania, czyli urządzenia komunikujące się z operatorem za pośrednictwem interfejsu użytkownika (urządzenia CNC), kreują nieustanny rozwój technologiczny i wykonują szereg operacji obróbczych, bez których nie sposób wyobrazić sobie dzisiejszych linii produkcyjnych, zaopatrujących niemal każdą dziedzinę przemysłową.
Cięcie CNC pozwala na uzyskiwanie idealnej dokładności, niedoścignionej jakości, optymalnych kształtów i form w powtarzalnych seriach, ustalanie kolejności zadań i cykliczności wykonywanych ruchów.
Cięcie CNC na zlecenie.
Aby korzystać z ogromu możliwości oferowanych przez technologie CNC, wcale nie trzeba inwestować w kosztowne urządzenia. U nas szybko i wygodnie zlecisz usługi cięcia CNC. Zapewniamy kontakt pomiędzy Klientem a Wykonawcą i umożliwiamy tym podmiotom nawiązanie bezpośredniej relacji oraz współpracy biznesowej. W szerokiej, ogólnopolskiej sieci partnerskiej zgromadzeni zostali zweryfikowani Wykonawcy z całej Polski – także w kategorii cięcie CNC – dysponujący bogatym parkiem maszynowym.
Cięcie CNC na zamówienie to nasza specjalność, a obróbce poddajemy wszystkie materiały (metal, tworzywa sztuczne, drewno, tkaniny, papier, szkło, kamień). Wystarczy, że zamieścisz na naszej platformie ogłoszenie z informacją, co potrzebujesz wykonać poprzez cięcie CNC (możesz dołączyć niezbędne pliki), a firmy CNC chętne podjąć się zlecenia same się z Tobą skontaktują. Będziesz mógł porównać wszystkie oferty w kategorii cięcie CNC i wybrać najkorzystniejszą z nich. Zapraszamy do współpracy.
Ile kosztuje cięcie CNC?
Jeżeli zastanawiasz się, ile kosztuje cięcie CNC, to spieszymy z informacją, że ustalenie ostatecznej ceny realizacji zamówienia zależne jest od wielu czynników, między innymi: wybranej technologii, rodzaju, grubości i wielkości obrabianego materiału, stopnia trudności i złożoności projektu, ilości zamawianych elementów czy produktów.
Cięcie CNC – jakie procesy realizujemy?
Cięcie CNC to szereg możliwości. Oferujemy zatem usługi w zakresie: cięcia laserowego, cięcia plazmowego, cięcia hydroabrazywnego (wodą) oraz cięcia tlenowego (gazowego). Każda z tych technologii dedykowana jest innemu profilowi produkcji – różne metody stosowane są do różnych materiałów, różnych ich grubości. Na podstawie kryteriów danego projektu należy dobrać właściwy proces do danego zastosowania.
Cięcie laserowe.
Bezdotykowe cięcie laserowe skupia promieniowanie selektywnie, do wymaganych niewielkich obszarów (często nawet rzędu mikrometra), co minimalizuje ryzyko deformacji, uszkodzenia, zniszczenia elementu poddanego obróbce. Pozwala to osiągać efekty zachwycające wysoką jakością, precyzją i dokładnością na konkretnych, wybranych obszarach materiału. Ta bardzo mała szerokość linii emisyjnej przekłada się na dużą moc w wybranym obszarze widma, siła tnąca nie wyraża się tutaj zatem w sile mechanicznej, ale termicznej. Powstająca wąska szczelina cięcia pozwala na uzyskiwanie nawet bardzo małych otworów, o niezwykłej finezji, oryginalnych kształtach i perfekcyjnie wykończonych brzegach bez najdrobniejszych strzępień. Wszystko to przy zdumiewającej prędkości. Wszystkie te właściwości trudne są do uzyskania w podobnym wymiarze przez inne metody, dlatego cięcie laserem uznaje się za najefektywniejszą obecnie, najbardziej uniwersalną metodę obróbki materiałów. Trwałość materiałów eksploatacyjnych jest wysoka (dzięki procesowi bezdotykowemu nic się nie niszczy i nie zużywa), automatyka maszyn niezawodna i gwarantująca bezpieczeństwo, dlatego wiele operacji cięcia z zastosowaniem lasera może przebiegać właściwie bezobsługowo. Ponadto przy zastosowaniu laserów włóknowych można w jednej maszynie użyć wiele głowic do cięcia. Systemy laserowe 3D są dużo bardziej wydajne i funkcjonalne niż systemy do cięcia blach płaskich 2D, bo pozwalają na zastąpienie wielu tradycyjnych technologii i dają możliwość precyzyjnej obróbki skomplikowanych detali przestrzennych.
Na rynku usług laserowych wykorzystuje się szereg rozmaitych urządzeń, pozwalających wykonywać różne procesy i różniących się wbudowanymi źródłami lasera. Najczęściej wykorzystywane są lasery gazowe (CO2), lasery fibrowe i lasery wanadatowe. Lasery gazowe cenione są za wysoką wydajność i dobrą jakość promieniowania, a z uwagi na generowaną długość fali (około 10 µm) doskonale nadają się do obróbki tworzyw sztucznych, tekstyliów, skóry, drewna, szkła, papieru. Lasery fiber mają dziesięciokrotnie mniejszą długość fali, dużo mniejszą średnicę ogniska, więc uzyskują wyższe skupienie energii i intensywność. W technologii tej więcej użytecznej energii jest absorbowane, a mniej odbijane, toteż charakteryzuje się ona doskonałą jakością i wysoką sprawnością, i jest lepiej pochłaniana przez atomy metalu, dlatego doskonale sprawdza się w obróbce właśnie metali. Lasery krystaliczne, czyli lasery na ciele stałym, mają długość fali podobną jak w laserach fibrowych, więc wykorzystywane są z powodzeniem w obróbce metali, tworzyw sztucznych, czasami również ceramiki.
Ważne przy tym jest nie samo posiadanie innowacyjnego parku maszynowego, ale również – a może przede wszystkim – wyspecjalizowanej kadry specjalistów, którzy zadbają o całość procesu i zapewnią właściwy jego przebieg. Wysoko wyspecjalizowani pracownicy dowodzą dokładnym prowadzeniem strumienia tnącego, co w połączeniu z precyzyjnym i stabilnym urządzeniem, odpornym na drgania, gwarantuje utrzymanie wymiarów ciętych elementów. U nas znajdziesz specjalistów od laserowego cięcia.
Cięcie laserem sprawdza się w różnych dziedzinach przemysłu i produkcji, jak na przykład: metalurgia, produkcja konstrukcji stalowych, budownictwo, architektura, przemysł stoczniowy, lotniczy, kolejowy, automotive, przemysł medyczny, meblarski, reklama. Cięcie laserowe może być z powodzeniem wykorzystywane przy produkcji maszyn i urządzeń, części zapasowych, różnego rodzaju komponentów i detali, prototypów, artykułów wyposażenia wnętrz, elementów małej architektury, makiet architektonicznych, dekoracji, ozdób, oznakowań, szyldów i w wielu innych zastosowaniach.
Zalety cięcia laserem.
- bardzo wysoka dokładność, precyzja, trwałość, jakość i estetyka wykonania, zachowanie wszystkich wymiarów, parametrów i właściwości,
- możliwość stworzenia najbardziej skomplikowanych kształtów, także elementów trójwymiarowych, przy idealnej powtarzalności,
- możliwość obróbki różnych materiałów,
- wąska szczelina cięcia, minimalna strefa wpływu ciepła,
- wysokie prędkości cięcia, dynamika, produktywność, pełna automatyzacja, komputerowa kontrola procesu,
- brak konieczności prac postfabrycznych, krawędzie zostają utwardzone podczas procesu cięcia, a hartowanie daje gładkie brzegi bez przymusu wykańczania po użyciu lasera,
- wydajność, optymalizacja, wyeliminowanie błędów, obniżenie ilości odpadów, brak zużycia głowicy tnącej, niskie koszty jednostkowe przy dużych partiach produkcji, ekonomiczność procesu.
Wady cięcia laserem.
- wysoki koszt zakupu urządzenia,
- zakres ciętych materiałów zależny od zastosowanego źródła lasera oraz powierzchni roboczej urządzenia.
Jakie materiały można poddawać cięciu laserem?
Cięcie laserem metalu.
Materiały metalowe, które można ciąć laserem: metal surowy, powlekany, szczotkowany, polerowany, anodowany, oksydowany, metale szlachetne (złoto, srebro), stal nierdzewna, ocynkowana, galwanizowana, węglowa, konstrukcyjna, szlachetna, kwasoodporna, aluminium, nikiel, tytan, chrom, miedź, mosiądz, brąz.
Przy użyciu nowoczesnych urządzeń laserowych wycinać można w najróżniejszych gatunkach stali. Istotną kwestią jest grubość surowca oraz strefa cięcia. Wycinarki laserowe są idealnym rozwiązaniem przy grubości do około 25-30 milimetrów. Uzyskanie dobrych rezultatów powyżej tej bariery wymaga wysokiej jakości wszystkich elementów, takich jak: materiał (stal przeznaczona do cięcia laserowego), czystość gazu, stan dyszy oraz jakość wiązki. Dobrze sprawdzą się w tej roli specjalne wycinarki laserowe CO2 o zwiększonej mocy. Innowacyjne technologie laserowe w optymalny sposób spełniają swoje funkcje, albowiem mają zainstalowane niezwykle intuicyjne oprogramowanie, które – z niewielką pomocą operatora – może samodzielnie dostosowywać parametry cięcia w zależności od rodzaju metalu.
Zastosowanie elementów metalowych ciętych laserem: rury, materiały budowlane, schody, poręcze, balustrady, ogrodzenia, barierki, stojaki, stelaże, meble, przedmioty codziennego użytku, części samochodowe, narzędzia medyczne i chirurgiczne, ostrza i wiele innych.
Jak to się odbywa: Cięcie laserem blach polega na rozprowadzeniu na niewielkiej powierzchni dużej ilości energii, przy użyciu wiązki laserowej, co powoduje nie tylko topienie materiału, ale przy większej mocy nawet jego wyparowanie, gdyż temperatury osiągane przy użyciu laserowych obrabiarek CNC wynoszą nawet kilka tysięcy stopni Celsjusza. Gdy promień się porusza i topi materiał, surowiec zostaje automatycznie przecinany wzdłuż określonej linii. Laserowe cięcie metalu wyróżnia się trzema etapami: początkiem cięcia (podczas którego gaz dostarczany do strefy tnącej z jednej strony blachy powoduje usuwanie stopionego i utlenionego materiału na stronę przeciwną), cięciem właściwym (gdy wiązka już wniknie w określonym punkcie w powierzchnię, a system przebiega z wyznaczoną geometrią i rozdziela materiał) i zakończeniem (trzeba wówczas uważać, żeby odcinana część nie przechyliła się oraz żeby nie doszło do przegrzania).
Wiązkę laserową cechuje duża gęstość energii, co pozwala kształtować nawet trudno topliwe materiały, przy niewielkiej strefie wpływu ciepła, braku skrzywień, wypaczeń, za to przy dużej prędkości przebiegu procesu. Laserowe cięcie metalu przeprowadzone może być metodą spalania, stapiania bądź sublimacji, ale najczęściej odbywa się w różnych kombinacjach.
Przy cięciu metodą spalania temperatura w szczelinie może wynosić nawet 1200 stopni Celsjusza. Wykorzystywane jest przy tym zjawisko utleniania materiału rozgrzanego przez promień lasera, który pozostawia płynny żużel, wydmuchiwany przez ciśnienie gazu technicznego. Technikę tę stosuje się głównie do obróbki stali niestopowych lub niskostopowych – osiągane są tutaj przy stosunkowo niskiej mocy lasera względnie duże prędkości cięcia.
Nieco inaczej wygląda to przy cięciu metodą stapiania, gdzie nie zachodzi zjawisko spalania, a więc dodatkowa energia musi pochodzić z mocniejszego promienia laserowego lub wspomagania elektrycznego. Materiał, na który oddziałuje promień laserowy o dużej intensywności i mocy, doprowadzony zostaje do postaci płynnej i wydmuchany przez gaz techniczny o dużej energii kinetycznej. Brak reakcji utleniania powoduje powstawanie powierzchni wolnych od tlenków, co ma istotne znaczenie zwłaszcza przy obrabianiu stali wysokostopowych. Metoda ta sprawdza się też przy cięciu metali nieżelaznych.
Z kolei przy tworzeniu różnego rodzaju tabliczek pamiątkowych, trofeów sportowych, prestiżowych wizytówek stosuje się lasery o dużej mocy, które doprowadzą część obrabianego materiału do stanu gazowego, a następnie wydmuchają pod wysokim ciśnieniem – i sposób ten nosi nazwę sublimacji.
Cięcie laserem rur i profili.
Rury i profile zdatne do obróbki laserowej mogą być wykonane z następujących materiałów: aluminium, mosiądz, miedź, chromonikiel, stal konstrukcyjna, nierdzewna, galwanizowana, ocynkowana, węglowa.
Zastosowanie ciętych laserowo rur i profili: części składowe rozmaitych wyrobów metalowych, rurociągów, podpór, ram, konstrukcji nośnych, konstrukcji maszyn i urządzeń. Znajdą one zastosowanie w budowie pojazdów użytkowych, maszyn rolniczych, mebli, regałów sklepowych, przyrządów fitness, w petrochemii i architekturze.
Jak to się odbywa: Proces laserowego cięcia rur i profili polega na punktowym wprowadzeniu energii pod postacią wysokoenergetycznego strumienia tnącego (gorącego promienia laserowego), otoczonego gazem technicznym o dużej czystości. Jest to półprodukt bardziej przetworzony niż blacha, dlatego potrzeba mniejszej ilości obróbki dla powstania gotowego produktu. Można wycinać dowolne typy (prostokątne, kwadratowe, okrągłe, owalne, w kształcie liter H, L, T, U), zachowując regularność krawędzi, wysoką jakość, bez konieczności późniejszego zastosowania dodatkowych czynności (jak: ukosowanie, wiercenie, frezowanie, pasowanie). Pozwala to na bezproblemowe i precyzyjne połączenie wszystkich części. Przy pracach bardziej zaawansowanych niż obróbka 2D, użyć można technologii 3D, pozwalającej na wykonywanie skosów do 45 stopni (głowica tnąca pracuje w pięciu osiach, co pozwala na wycinanie nawet bardzo skomplikowanych brył i często zastępuje wiercenie, wykrawanie, wybijanie, gwintowanie, frezowanie, piłowanie, usuwanie zadziorów itd.). Warto też pamiętać, że obróbka laserowa to nie tylko przecinanie rur (giętych, hydroformowanych, wstępnie uformowanych, wstępnie spawanych) i profili (zamkniętych – prostokątnych, kwadratowych, okrągłych, specjalnych – i otwartych), giętych lub tłoczonych elementów, ale również możliwość jednoczesnego kształtowania otworów i tzw. zamków służących precyzyjnemu łączeniu elementów. Istotną funkcję – zwłaszcza w systemie seryjnym – pełni dodatkowy osprzęt, pozwalający zautomatyzować w pełni produkcję krótkich i długich detali z materiału o dowolnym kształcie oraz powierzchniach płaskich lub tłoczonych. Ponadto urządzenia te umożliwiają automatyczny załadunek i rozładunek detali po obróbce cięcia laserowego 3D, co przekłada się na wydajniejszą i bezpieczniejszą pracę. Profesjonalna opieka inżynierska, nowoczesne oprogramowanie i cyfrowe sterowanie – to gwarancja niedoścignionej dokładności i najwyższej jakości (bez gradu, rys, odprysków i zadrapań). Laserowe cięcie rur i profili to możliwość uzyskania skomplikowanych i bardzo wymagających pozycji, modułów o praktycznie każdym kształcie oraz pewne cięcie, bez obawy o deformację, jeżeli zastosuje się odpowiednie parametry (zapewniające np. niemożność złamania wiązką laserową przeciwległej strony rury). Sprawdza się to zarówno w przypadku jednostkowych, jak i średnio- czy wieloseryjnych zleceń.
Cięcie laserem tworzyw sztucznych.
Materiały plastikowe, które można ciąć laserem: poliamid (PA), poliwęglan (PC), polipropylen (PP), poliuretan (PUR), poliformaldehyd (POM), poliimid (PI), polistyren (PS), polimetakrylan metylu (PMMA, akryl, pleksi), poliester (PES), politereftalan etylenu (PET), polietylen (PE), poliarylosulfon (PSU, PPSU), polieteroketon (PEEK), kopolimer akrylonitrylu, butadienu i styrenu (ABS), silikon, pianka, inne.
Nie powinno się obrabiać laserowo (bo grozi to powstaniem trujących gazów): PCW, winylu, poli-dwubromostyrenu, PTFE (teflonu).
Jest bardzo dużo rodzajów tworzyw sztucznych, różniących się właściwościami, dlatego długość fali i inne parametry cięcia będą się różnić, zależnie od obrabianego materiału.
Zastosowanie elementów plastikowych ciętych laserem: prototypy, elementy maszyn i urządzeń,makiety architektoniczne,szyldy, oznakowania, tablice znamionowe, informacyjne i reklamowe, gadżety reklamowe i promocyjne, trofea i nagrody, identyfikatory, szablony, uszczelki, filtry, opakowania, pudełka, pojemniki, zadaszenia, świetliki, osłony, płyty o specjalnym przeznaczeniu (ekrany przeciwhałasowe, antytermiczne, płyty fluorescencyjne, tarcze policyjne), przedmioty użytkowe, zabawki, urządzenia elektroniczne, wyświetlacze, folie ochronne do ekranów dotykowych, przednich paneli, wskaźników instrumentów i prędkościomierzy, membrany klawiatur, dekoracje i ozdoby, biżuteria, inne.
Jak to się odbywa: Ten bezdotykowy proces cięcia tworzyw sztucznych laserem, niepodatny na deformacje, uszkodzenia, zniekształcenia, polega na pokonaniu spójności materiału przy wykorzystaniu wiązki laserowej. Kiedy promień lasera skupi się w określonym punkcie, przenika materiał i rozpoczyna się proces cięcia. Mamy do czynienia z tak dużą temperaturą (ale tylko miejscowo, pozostała część przedmiotu nie jest obciążona termicznie), że tworzywo roztapia się lub odparowuje. Lasery o ultrakrótkim czasie impulsu pozwalają odparować prawie każdy materiał w tak szybkim czasie, że wpływ ciepła pozostaje niemal niedostrzegalny. Pozwala to na zachowanie gładkich powierzchni (bez nadtapiania), idealnie zaokrąglonych krawędzi i estetycznego wyglądu bez konieczności stosowania obróbki wykańczającej.
Na proces cięcia laserem wpływ mają następujące parametry: położenie ogniska (wpływające na gęstość mocy i kształt szczeliny cięcia na przedmiocie obrabianym), średnica ogniska (określająca kształt i szerokość szczeliny cięcia), średnica dyszy (określająca kształt i ilość strumienia), moc lasera (energia na powierzchnię = gęstość mocy x czas oddziaływania na przedmiot obrabiany), prędkość cięcia (zmieniająca się w zależności od zadania i obrabianego materiału, grubość materiału wpływa na jej zmniejszenie, a większa moc lasera na przyspieszenie), tryb pracy (określający czy energia docierać będzie w trybie ciągłym czy impulsowym), stopień polaryzacji (określający, w jakim stopniu osiągnięta została pożądana polaryzacja kołowa), gazy tnące i ciśnienia cięcia (mówiące o tym, jakie gazy procesowe z jakim ciśnieniem przetłaczane są przez szczelinę ciecia).
Cięcie laserem drewna.
Materiały drewniane, które można ciąć laserem: drewno lite (sosna, topola, balsa, dąb, buk, wiśnia, czereśnia, akacja, jawor, klon, jesion, orzech włoski, olcha, brzoza, lipa, mahoń, teak, eukaliptus, bambus, jodła, cedr, daglezja), tarcica lita, fornir, okleina naturalna, płyta pilśniowa (MDF, HDF, LDF), płyta wiórowa (OSB), sklejka, korek.
Drewno występuje w różnych postaciach, różniących się gęstością, rodzajem włókien, zawartością żywicy, twardością, dlatego w zależności od zastosowanego rodzaju trzeba wybrać odpowiednie moce lasera oraz prędkości przejścia. W zasadzie wszystkie rodzaje drewna da się ciąć laserem (aczkolwiek trudno to czynić w drewnie hebanowym), ważne jednak, aby materiał był jednorodny, o stałej gęstości i zawartości żywicy. Akurat nienajlepszym materiałem do cięcia laserowego jest korek, bo krawędzie robią się przy tym czarne i zwęglone, za to przy grawerowaniu sprawdza się on znakomicie. Przed każdym cięciem właściwym warto ustawić próbkę lasera, aby ocenić, jak zachowa się podczas obróbki dany materiał.
Zastosowanie elementów drewnianych ciętych laserem: rękodzieło artystyczne, biżuteria, zabawki, figurki 3D, meble, artykuły wyposażenia wnętrz i dekoracyjne, przybory kuchenne, modele, tabliczki, szyldy i oznakowania zewnętrzne, prezenty, pamiątki, ozdoby, podkładki, ramki, skarbonki, breloki, magnesy, wizytowniki, podstawki, stojaki, zawieszki, obudowy, opakowania, skrzyneczki, wykończenia instrumentów muzycznych.
Jak to się odbywa: Cięcie drewna odbywa się metodą sublimacji, czyli stan skupienia materiału zmienia się z ciała stałego bezpośrednio w gazowy. Strumień gazu tnącego utrzymuje cząsteczki pary z dala od układu optycznego. Istnieje stosunkowo niskie obciążenie termiczne materiału w pobliżu prześwitu cięcia, dlatego linie brzegowe nie są ani spalone, ani mocno przypalone, a ładnie, starannie, dokładnie i precyzyjnie wykończone, bez potrzeby stosowania obróbki wykańczającej. Cięcia wysokiej jakości można uzyskać przez dokładne ogniskowanie i wybór odpowiedniej optyki oraz dostarczanie sprężonego powietrza.
Obróbka bezdotykowa ma też ten plus, że jest bezpieczna, nie jest potrzebne mocowanie materiału, nie tępią się narzędzia, a brak sił skrawania pozwala na cięcie skomplikowanych ażurów, a wszystko to bez wypaczeń materiału, pyłu i sypiących się wiórów (odpadają więc czasochłonne i trudne procesy czyszczenia).
Przy cięciu drewna miękkiego wystarczające będą mniejsze moce lasera niż przy cięciu drewna twardego. Należy także pamiętać, że im wyższa zawartość żywicy w drewnie, tym częściej może dochodzić do przypaleń czy zwęgleń krawędzi.
Najefektywniejsze jest cięcie drewna do 20 mm. Powyżej tych wartości warto pomyśleć o użyciu frezarki, gdyż laser musiałby przejść wiele przejść, co mogłoby skutkować niewytworzeniem czystego cięcia. Frez CNC z łatwością poradzi sobie z większą grubością, ale trzeba się przy tym liczyć z tym, że szerokość nacięcia będzie większa niż w przypadku cięcia laserem. Ploter frezujący CNC może przy okazji wykonać rzeźbę w drewnie, a wycinarka laserowa – grawer (również relief) na całym obszarze roboczym.
Cięcie laserem tkanin.
Materiały tekstylne, które można ciąć laserem: bawełna, filc naturalny i syntetyczny, jedwab, len, satyna, aksamit, koronki, nylon, wiskoza, welur, diagonal, polar, plus, softshell, jeans (denim), skaj, skóra, sztuczne futro (faux fur), drelich, zamsz, ultra-zamsz, mikrozamsz, mikrofibra, mikrofaza, alcantara, aramid, Kevlar®, Ultrasuede®, Tencel®, Tyvek®, tkaniny spacer, diagonalne, techniczne, syntetyczne, lateks i inne.
Cięcie laserem bez problemu sprawdza się przy większości materiałów syntetycznych oraz organicznych.
Zastosowanie elementów tekstylnych ciętych laserem: artykuły dla branżymodowej, przemysłu odzieżowego, technologii medycznych, dekoracyjnej (banery reklamowe, flagi), zabawkarskiej (maskotki), tekstylia domowe, przemysłowe tkaniny techniczne (a z nich: filtry, tapicerki, samochodowe poduszki powietrzne, owiewki samochodowe, tekstylia w przemyśle żeglarskim, torby, plecaki, kurtki, odzież specjalna i ochronna, kamizelki ostrzegawcze i kuloodporne, buty, namioty wojskowe, balony, lotnie, paralotnie, spadochrony, osłony termiczne, części kompensatorów).
Jak to się odbywa: Wiązka laserowa, przechodząc przez optykę, rozwija temperaturę powodującą topnienie i odparowanie tkaniny. Można w ten sposób tworzyć ażurowe efekty, ozdobne wzory, ornamenty, frędzle bądź po prostu przyciąć materiał bez strzępienia, gdyż wiązka lasera topi materiał, sklejając krawędzie i zapewniając czyste, spójne, gładkie wykończenie, bez strzępień (tzw. kauteryzacja). Możliwe jest cięcie tkanin we wszystkich kierunkach, niezależnie od struktury materiału. Obróbka odbywa się bezdotykowo i beznarzędziowo, dzięki czemu materiał nie jest poddawany obciążeniom, nie zniekształca się, nie wypacza, a narzędzie nie ulega zużyciu. Tkaniny organiczne (typu bawełna, len) podczas cięcia laserem mogą uzyskiwać zbrązowiałe krawędzie, co da się jednak kontrolować poprzez wybór odpowiednich parametrów, właściwej soczewki i użycie sprężonego powietrza.
W programach wektorowych typu Adobe Illustrator, Rhino lub Inkscape można cyfrowo projektować wzory do cięcia albo wprowadzać w nie ręczne wzory linii, a one przekonwertują je na format cyfrowy. Materiał umieszcza się płasko na maszynie laserowej i załadowuje wzory cięcia do lasera. W kolejnym kroku uruchamia się proces laserowy, a wzory zostają wycięte szybko i dokładnie.
Cięcie laserem papieru.
Materiały papiernicze, które można ciąć laserem: papier kredowy, niepowlekany, welinowy, woskowany, satynowany, czerpany, tektura lita i sklejana, falista, introligatorska, warstwowa (architektoniczna), karton, brystol, kalka kreślarska.
Zastosowanie elementów papierowych ciętych laserem: kartki, koperty, zaproszenia, arkusze barwne (korespondencje, cenniki, menu), karnety, vouchery, bony podarunkowe, winietki na stół, wizytówki, ilustracje 3D, okładki książek, zakładki do książek, kalendarze, planery, szablony (używane do oznaczeń produktów przemysłowych czy graffiti), etykiety, dyplomy, świadectwa, gratulacje, nagrody, podziękowania, makiety dla architektów, wycinanki, układanki, puzzle, modele samolotów, samochodów, elementy do scrapbookingu, materiały szkolne i biurowe, ozdoby, papeteria, etykiety, ekspozytory papierowe, standy kartonowe, uszczelki kartonowe, foldery reklamowe, gadżety, logotypy, koronki i ornamenty, dekoracje okolicznościowe, papierowe maski, torebki, paczki, pudełka, kosze, wyświetlacze, teczki, wysokiej jakości opakowania (wycinanie i wykonywanie miejsc zagięć). Wyżej wymienione artykuły wykorzystywane są przez wiele branż: rękodzieło artystyczne, sztukę, rzemiosło, druk, poligrafię, reklamę, branding, materiały identyfikacji wizualnej, przemysł papierniczy, opakowaniowy, dekoracyjny, artykuły szkolne, wykańczanie papieru, modelarstwo, scrapbooking.
Jak to się odbywa: Cięcie papieru za pomocą lasera jest procesem rozdzielania termicznego, przeprowadzanym metodą sublimacji. Wiązka laserowa uderza w powierzchnię materiału papierowego i nagrzewa ją aż do stopienia lub całkowitego odparowania. Właściwy proces cięcia rozpoczyna się w momencie, kiedy wiązka wniknie w materiał w jednym punkcie, a system laserowy, przebiegając zgodnie z wybraną geometrią, spowoduje rozdzielenie obrabianego materiału.
Rodzajów papieru, kartonu i tektury jest wiele, dlatego też nie ma uniwersalnych parametrów ich obróbki. Za każdym razem, kiedy rozpoczyna się pracę na nowym materiale, warto skorzystać z matrycy skali szarości (składającej się ze 100 różnych odcieni szarości), która pomoże ustalić właściwe parametry obróbki laserowej.
Można obrabiać materiał bez dymu i okopconych, ponadpalanych krawędzi, zachowując precyzję idealnych konturów (bez skaz, śladów, zmarszczek i zniekształceń), ale tam, gdzie efekt przypalenia krawędzi jest pożądany – można go osiągnąć poprzez wybranie odpowiednich parametrów. Przy cięciu laserowym nie trzeba też mocować materiału, toteż nie dochodzi do jego zniszczenia, uszkodzenia, poszarpania, zmiażdżenia. Wycinarka laserowa pozwala skutecznie i szybko przecinać nawet wiele warstw grubego materiału (typu karton), bez obawy o zniszczenie.
Cięcie papieru pozwala na dowolność i dobór technik dopasowanych do potrzeb. Może być wykorzystywane do uzyskania precyzyjnych krzywizn i ścisłych narożników, ornamentów, różnego rodzaju zdobień, dziurkowania, perforowania, drapania, modelowania, cięcia zewnętrznego albo filigranowego, opracowywania prototypów opakowań, tworzenia kartek pop-up, papercraftingu (cardmakingu), scrapbookingu i wielu innych zastosowań.
Cięcie laserem szkła.
Materiały szklane, które można ciąć laserem: szkło okienne, hartowane, ceramiczne, kolorowe, artystyczne, laminowane, lakierowane, lane, prasowane, tłoczone, taflowe, kryształowe, zwierciadlane, lustrzane, float, płaskie, stożkowe, okrągłe, pojemnikowe, szklanki, kieliszki, karafki, butelki.
Nie każdy rodzaj szkła nadaje się do cięcia laserowego.
Zastosowanie elementów szklanych ciętych laserem: szyby okienne, szyby kominkowe, ścianki działowe, kabiny prysznicowe, lustra, optyka, balustrady, schody, blaty, panele kuchenne i łazienkowe, meblościanki, wyposażenie sklepów, gabloty wystawiennicze, witryny, elementy szklane w przemyśle motoryzacyjnym, chemicznym, budowlanym, szyby w smartfonach, szkło ochronne, rozkrój szklanych rurek i pojemników, materiały promocyjne, reklama, oznakowania, ozdoby, dekoracje, sztuka, pamiątki, podarunki, nagrody, statuetki.
Jak to się odbywa: Do cięcia szkła stosuje się lasery CO2 o dużej mocy oraz wykorzystuje przy tym ultrakrótkie impulsy laserowe. Pęknięcie szkła podczas procesu laserowego cięcia szkła odbywa się wzdłuż bardzo precyzyjnej linii. Dzięki odpowiedniemu doborowi rodzaju cięcia i parametrów (jak: energia impulsu, współczynnik nakładania, powtarzalność impulsu) zapobiec można powstawaniu mikropęknięć i ukruszeń na krawędziach, wykluczając przy okazji konieczność czasochłonnego wykańczania i znacznie przyspieszając czas obróbki. Pozwala to szybko i bezbłędnie zrealizować najbardziej wymagające zlecenia – zarówno płaskie elementy, jak i te o skomplikowanej geometrii i zakrzywionych płaszczyznach – przy zachowaniu wysokiej jakości cięcia. Technologia ta nie potrzebuje stosowania dodatkowej cieczy chłodzącej, jak w przypadku cięcia mechanicznego szkła, co przekłada się na mniejsze koszty konserwacji oraz późniejszego czyszczenia szyby. Poprzez eliminację bądź znaczne ograniczenie mechanicznych uszkodzeń do minimum ogranicza się także straty produkcyjne. Umiejętnie przeprowadzone cięcie laserem szkła jest więc skuteczne, efektywne i ekonomiczne.
Na jakość cięcia laserowego wpływ ma wiele czynników: parametry (takie jak: mod promieniowania, współczynnik jakości wiązki BPP, rodzaj gazu tnącego, średnica wiązki w ognisku, położenie ogniska, prędkość cięcia, energia impulsu, współczynnik nakładania i powtarzalności impulsu), dokładność prowadzenia wiązki laserowej (w połączeniu ze stabilną obrabiarką o wysokiej odporności na drgania), właściwości ciętego materiału (absorpcja, przewodność cieplna).
Cięcie wodą.
Proces znany pod wieloma nazwami – także jako cięcie strumieniem wody, obróbka hydro-abrazyjna, obróbka hydro-ścierna, obróbka strumieniowo-ścierna, obróbka wodno-ścierna, waterjet, abrasive waterjet (AWJ) – stosowany jest zwykle wszędzie tam, gdzie obróbka termiczna, ubytkowa czy cięcie tarczą nie mogą zapewnić zadowalających efektów. Polega na rozdzielaniu materiałów – tudzież przecinaniu ich – przy wykorzystaniu wody pod bardzo wysokim strumieniem, a w przypadku bardzo twardych i grubych elementów jest to woda z dodatkiem ścierniwa (garnetu). Regulując rodzaj użytego ścierniwa, jego gramaturę, ilość, a także prędkość cięcia, decydujemy o jakości krawędzi – najszybsze jest cięcie rozdzielające, może się to jednak przełożyć na nierówności krawędzi, z kolei cięcie jakościowe odbywa się przy niższej prędkości, co przekłada się również na wyższe koszty. Po skończeniu prac nie ma konieczności dalszej obróbki elementów poprzez frezowanie czy toczenie. Cięcie wodą odbywa się na zimno, nie występuje więc strefa wpływu ciepła ani problem odkształceń termicznych, gdyż temperatura krawędzi podczas cięcia nie przekracza 100oC.
Pięcioosiowe wersje urządzeń (3D) pozwalają tak pochylać głowicę, żeby można było wycinać pod odpowiednim kątem – idealnie sprawdza się to w żłobieniu czy ukosowaniu do celów spawalniczych.
Cięcie może odbywać się przy użyciu wielu głowic i jednej pompy multiplikatorowej, trzeba jednak wziąć pod uwagę, że większa liczba głowic wymagać będzie zastosowania mniejszego otworu albo większej pompy. Wysokie ciśnienie (nawet 4000 bar) – niezbędne przy cięciu strumieniem wody – uzyskiwane jest za pomocą pomp HP (High Pressure), a stosowane do tego celu są dwa typy pomp: tłokowe i wzmacniaczowe.
Rodzaj głowicy dobiera się pod dany materiał. Używane są głowice: wodne (do: miękkiej gumy, pianki, miękkich wykładzin PVC, folii, miękkiego bądź cienkiego drewna, tkanin, papieru i tektury oraz innych miękkich surowców), wodno-ścierne (do: szkła zwykłego i kuloodpornego, twardego bądź grubego drewna, MDF, twardszych tworzyw sztucznych, nylonu, Kevlaru, brązu, miedzi, mosiądzu, aluminium, stali zwykłej, nierdzewnej, narzędziowej, Inconelu, włókna węglowego, kompozytów, ceramiki, kamienia – granitu, marmuru).
Wycinanie przy użyciu tej technologii daje możliwość przebijania (z dokładnością do 0,1 mm) praktycznie wszystkich rodzajów materiałów, poza diamentami (m.in.: metalu, drewna, tworzyw sztucznych, pianki, gumy, szkła, kamienia, ceramiki), bez zmiany ich struktury. Wodą można więc wycinać różnorodne kształty w szerokiej gamie materiałów, z czego korzysta branża spożywcza, papiernicza, drzewna, meblowa, wykończenia wnętrz, budowlana, motoryzacyjna, lotnicza, a także przemysł ciężki, maszynowy, metalowy, elektroniczny.
Zalety cięcia wodą.
- precyzja cięcia, powtarzalność wymiarów,
- szeroki zakres rodzajów ciętych w ten sposób materiałów,
- możliwość przecinania dużych grubości,
- bezpieczeństwo: brak oparów, bezpyłowość,
- brak problemów z rozszerzalnością cieplną i naprężeniami materiałów,
- brak odkształceń, odprysków, uszkodzeń, mikropęknięć,
- brak odpadów surowca lub ich niewielka ilość.
Wady cięcia wodą.
- duży pobór prądu przez pompę.
Jakie materiały można poddawać cięciu wodą?
Cięcie wodą metalu.
Materiały metalowe, które można ciąć wodą: stal węglowa, nierdzewna, narzędziowa, konstrukcyjna, kwasoodporna, Hardox, miedź, aluminium, mosiądz, brąz, tytan.
Zastosowanie elementów metalowych ciętych wodą: szybkie wytwarzanie prototypów, detale oraz konstrukcje z grubego i twardego metalu, elementy maszyn, sita do kotłów.
Jak to się odbywa: Technologia abrasive waterjet używa strugi wody do przyspieszenia ziaren ścierniwa (np. garnetu, twardszego i o ostrzejszych krawędziach niż piasek). Po przejściu przez dyszę wodną woda powoduje inżektorowe zasysanie ścierniwa do komory miksującej, po czym ta mieszanina wody i ścierniwa kierowana jest do dyszy hydro-ściernej (mixing tube) w celu jej uformowania i ustabilizowania. Powstała struga jest w stanie przecinać najtwardsze materiały, nawet o grubości większej niż 150 mm, gdyż u wylotu z dyszy jej prędkość przekracza 300 m/s. Do cięcia bardzo twardych materiałów zalecane jest wykorzystywanie proszku ściernego z węglika boru.
Cięcie wodą drewna.
Materiały drewniane, które można ciąć wodą: drewno lite (dąb, akacja, mahoń, jesion, jabłoń).
W przypadku płyt pilśniowych (np. MDF) i wiórowych, z uwagi na ich chłonność i pęcznienie pod wpływem wody, bądź możliwość rozpuszczenia się kleju (w przypadku niektórych sklejek), lepiej wybrać inną metodę obróbki.
Zastosowanie elementów drewnianych ciętych wodą: produkcja i zdobienie mebli, elementy podłogi i listew, elementy ozdobne w balustradach balkonowych, blaty mebli.
Jak to się odbywa: Do przecinania drzewa cienkiego i miękkiego w zupełności wystarczy zastosowanie głowicy wodnej, natomiast przy cięciu grubych i twardych gatunków drzew z pewnością praktyczniejsze i skuteczniejsze będzie użycie głowicy wodno-ściernej, a zatem obróbka z dodatkiem ścierniwa.
Cięcie wodą drewna sprawdzi się przemyśle drzewnym oraz meblarskim, a także wszędzie tam, gdzie zależy nam na wykrawaniu skomplikowanym detali i złożonych kształtów z drewna. Technologia ta może się okazać dużo użyteczniejsza niż zastosowanie tradycyjnych frezarek do drewna.
Cięcie wodą tworzyw sztucznych.
Materiały plastikowe, które można ciąć wodą: poliamid PA, poliwęglan PC, polietylen PE, HDPE, polipropylen PP, polipropylen kanalikowy – kartonplast, kopolimer akrylonitrylo-butadieno-styrenowy ABS, polichlorek winylu PVC, poli(tlenek metylenu) POM, poli(metakrylan metylu) PMMA, politereftalan etylenu PET, PETG, puliuretan, poliueratan spieniony PU, PUR, polistyren, polistyren wysokoudarowy Tuplex HIPS, PS, tekstolit, bakelit, winyl, teflon PTFE, pianka, guma, gąbka, styropian, wełna mineralna (wełna szklana), włókno węglowe (karbon), aramid, grafen, płyty HPL, szkło epoksydowe.
Zastosowanie elementów z tworzyw sztucznych ciętych wodą: uszczelki, izolacje, neony, szyldy, logotypy, litery reklamowe, elementy wykończeniowe samochodów i samolotów, dekoracje, upominki.
Jak to się odbywa: Cięcie tworzyw sztucznych strumieniem wody to proces niezwykle efektywny. Sekretem precyzji, szybkości i łatwości pracy z nawet najbardziej wymagającymi tworzywami jest zastosowanie wysokiego ciśnienia, wynoszącego nawet 4000 bar, co po zamianie w energię kinetyczną zapewnia strumieniowi wody prędkość zbliżoną do prędkości dźwięku. Urządzenia do obróbki hydro-abrazyjnej zbudowane są z: pompy wysokociśnieniowej (dostarczającej strumień) oraz wycinarki (pozwalającej na zmieszanie go z materiałem ściernym i wypuszczenie w odpowiednim kierunku). Woda wykorzystywana jest wielokrotnie, w zamkniętym obiegu. Wysoką jakość krawędzi zapewnia także brak strefy wpływu ciepła, dzięki czemu brzegi ciętych elementów nie ulegają nadtopieniu.
Cięcie wodą szkła.
Materiały szklane, które można ciąć wodą: szkło lite,warstwowe (klejone folią lub żywicą), białe, kolorowe, płaskie i inne, lustra, powłoki pancerne, kuloodporne, zbrojone.
Cięcie wodą nie sprawdzi się w przypadku szkła hartowanego.
Zastosowanie elementów ze szkła ciętych wodą: szkło do smartfonów, szkło meblowe, akwaria, szyby zabytkowych samochodów, inkrustacje w blatach stołowych, witraże, lustra, wyroby biżuteryjne.
Jak to się odbywa: Kruche materiały, jak szkło, wymagają przebijania niskociśnieniowego. Dzięki temu można im nadawać kontury i profile, jakich nie sposób byłoby uzyskać przy użyciu innych technologii. Ważne jest, żeby otwory w szkle zacząć wykonywać przy ciśnieniu ok. 7200 psi/500 barów do 11 600 psi/800 barów, a dopiero później zacząć je zwiększać. Do proporcjonalnej regulacji ciśnienia używa się multiplikatora. Zamiast piasku kwarcowego, jako ścierniwa można używać oliwinu, który z uwagi na miękkość ogranicza możliwość powstawania pęknięć, odprysków i innych wad, dzięki czemu krawędź cięcia jest estetyczna i idealnie gładka. Cięcie szkła wodą nie wywołuje drgań ani nie tworzy strefy wpływu ciepła, dlatego nie ma potrzeby wykonywania żadnej obróbki końcowej.
Parametry – takie jak ciśnienie cięcia, gradację, rodzaj ścierniwa, ilość wody – dobiera się pod obrabiany materiał (rodzaj użytego szkła oraz stopień skomplikowania projektu). Obrabiany materiał nie zmienia struktury ani cech wytrzymałościowych, zmienia się jedynie jego forma i kształt. Jeśli operator Waterjeta jest doświadczony, proces przebiega szybko, sprawnie, dokładnie.
Cięcie wodą kamienia.
Materiały kamienne, które można ciąć wodą: marmur, piaskowiec, granit, cembrit, konglomerat, gres szkliwiony, płyty ceramiczne, glazura i terakota.
Zastosowanie elementów z kamienia ciętych wodą: listwy dekoracyjne (bordiury), intarsje, rozety i mozaiki na ścianach i podłogach, loga i herby, wstawki dekoracyjne, blaty kuchenne i łazienkowe, parapety, schody, nagrobki, pomniki, rzeźby, tablice pamiątkowe.
Jak to się odbywa: Z uwagi na niewielką ciągliwość (odkształcenia, rozciągliwość) kamienia, cięcie tak kruchego materiału wymaga przebijania niskociśnieniowego (ok. 800 bar). Przy zastosowaniu nieodpowiednich parametrów i nieumiejętnej obróbki materiał mógłby pękać, kruszyć się czy odpryskiwać podczas przebijania. Cięcie kamienia wodą warto zatem zlecić specjalistom.
Podczas docinania kamienia strumieniem wody stosuje się wyłącznie zimną wodę, co pozwala zachować naturalne właściwości kamienia na krawędziach oraz minimalizuje ryzyko mikrouszkodzeń, które mogłyby w przyszłości postępować, powodując wyniszczanie materiału w głąb. Aby zapewnić perfekcyjne cięcie twardych materiałów, wykorzystuje się środek ścierny podobny do piasku, ale o większej chropowatości – garnet. W przypadku piaskowca można zredukować ilość materiału ściernego, ponieważ cząstki kamienia po ich wyłamaniu ze struktury same w sobie mogą służyć jako przecinający materiał ścierny.
Cięcie plazmą w metalu.
Cięcie plazmą możliwe jest dzięki silnie skoncentrowanemu łukowi elektrycznemu o dużej energii kinetycznej, jarzącemu się pomiędzy ciętym materiałem a nietopliwą elektrodą, umieszczoną w uchwycie plazmowym. Ową koncentrację łuku otrzymuje się dzięki dyszy tnącej (dyszy plazmowej), która może mieć średnicę od 0,6 do 2,0 mm (w zależności od natężenia prądu cięcia). Dzięki dużemu zagęszczeniu mocy powstaje strumień plazmy o temperaturze nawet kilkunastu tysięcy stopni Celsjusza, który z łatwością i ogromną prędkością (bliską prędkości dźwięku) przetapia i przedmuchuje metal, wyrzucając materiał ze szczeliny cięcia. Materiał poddawany jest zarówno działaniu termicznemu (łuk elektryczny), jak i mechanicznemu (ciśnienie gazu plazmowego).
Przy cięciu plazmowym stosowany jest prąd stały o biegunowości ujemnej – uchwyt masowy podłączony jest więc do bieguna dodatniego, a plazmowy do ujemnego. Zajarzenie łuku odbywa się poprzez potarcie dyszy tnącej o materiał cięty (w starszych rozwiązaniach) albo przez wykorzystanie tzw. łuku pilotażowego, jarzącego się między elektrodą a dyszą plazmową, powstającego dzięki wykorzystaniu krótkich impulsów o wysokim napięciu, wytwarzanym w jonizatorze wysokiej częstotliwości. Umożliwia to wstępne nadtopienie brzegów ciętego materiału i rozpoczynanie cięcia w dowolnym położeniu palnika tnącego.
System plazmowy składa się z: palnika, przewodu uziemiającego, źródła zasilania i części eksploatacyjnych. W plazmach HD (czyli systemach plazmowych wąskostrumieniowych) są jeszcze konsole gazowe, dozujące i miksujące gazy techniczne (takie jak: tlen, azot, argon). Powszechnie stosuje się palniki z łukiem zewnętrznym (zależnym), ale są także palniki z łukiem wewnętrznym (niezależnym) – i te ostatnie stosowane są przede wszystkim do cięcia materiałów nieprzewodzących prądu elektrycznego oraz cienkich blach, jak również do metalizacji.
Cięcie metali plazmą może odbywać się różnymi metodami: podstawową (czyli zwykłe rozcinanie), szablonową (według przygotowanego szablonu), poprzez ukosowanie (czyli pod odpowiednim kątem) oraz żłobienie (pozwalające tworzyć regularne wyżłobienia w materiale). Cięcie może przebiegać w sposób zmechanizowany (po zainstalowaniu systemu na stole CNC), możliwe jest także cięcie wielu blach jednocześnie (po uprzednim ułożeniu ich w stos).
Wśród parametrów wpływających na przebieg cięcia plazmą znajdują się między innymi: natężenie prądu cięcia, napięcie łuku plazmowego, grubość oraz prędkość cięcia, odległość palnika od materiału oraz jego położenie względem ciętego przedmiotu, rodzaj, ciśnienie i natężenie przepływu gazu plazmowego, rodzaj i konstrukcja elektrody, średnica dyszy tnącej.
Cięcie metalu plazmą wykorzystywane jest w wielu gałęziach przemysłu. Jest to metoda ekonomiczna, sprawdzająca się w przypadku miękkiej blachy (o grubości od 6 do 40 mm), aluminium, stali konstrukcyjnej o grubości poniżej 30 mm, stali nierdzewnej, węglowej, stopowej, żeliwa, mosiądzu, miedzi. W zależności od źródła mocy, ręczne systemy plazmowe są zdolne do rozcinania blach o grubości do 75 mm, natomiast zaawansowane systemy wysokoamperażowe potrafią rozciąć nawet do 160 mm. Nie trzeba wcześniej czyścić zardzewiałych, brudnych czy pomalowanych powierzchni. Można przecinać blachy, profile, kształtowniki, rury czy siatki.
Zalety cięcia plazmą.
- szeroki zakres ciętych materiałów (w zasadzie wszystkich przewodzących prąd) oraz grubości cięcia,
- szybkie przebijanie,
- wąska strefa wpływu ciepła,
- niewielka szczelina cięcia,
- możliwość cięcia cienkich materiałów bez nadpalania krawędzi,
- relatywnie niski koszt inwestycji.
Wady cięcia plazmą.
- duży hałas i silne promieniowanie UV,
- spore ilości dymu i gazów,
- trudności w utrzymaniu prostopadłości krawędzi.
Cięcie gazem (tlenem) w metalu.
Ten rodzaj cięcia nazywany bywa też płomieniowym i polega na następujących po sobie procesach: rozgrzania metalu do temperatury zapłonu, utlenienia oraz wydmuchania go tlenem pod wysokim ciśnieniem. Do podgrzania wykorzystuje się: propan (przy grubszych blachach), acetylen (przy blachach cienkich), propylen lub gaz ziemny. Cięcie acetylenowo-tlenowe uzasadnione jest w przypadku, gdy występują częste przerwy pomiędzy cięciami i pozwala na szybkie osiąganie naprawdę wysokiej temperatury. Przy cięciu propanowo-tlenowym wzrost temperatury nie jest taki szybki, a zatem tę metodę wykorzystuje się do cięcia zautomatyzowanego dłuższych odcinków, z rzadkimi przerwami podczas pracy.
Cięcie tlenem najkorzystniejsze jest w przypadku materiałów, w których zapłon odbywa się w temperaturze niższej niż wynosi jego temperatura topnienia, a topnienie powstających tlenków w temperaturze niższej niż zapłon.
Jak to się odbywa: Na wysokości ok. 1,5-3 mm, nad ciętym arkuszem ustawia się płomień podgrzewający. Po osiągnięciu temperatury spalania przez górną krawędź blachy – w miarę wypływania rozżarzonego materiału – unosi się palnik, po czym otwierany jest zawór tlenu tnącego i rozpoczyna się cięcie. Po przecięciu dolnej części blachy i przedmuchaniu szczeliny rozpoczyna się przesunięcie cięcia. Im grubszy materiał, tym szerokość szczeliny jest większa. Należy pamiętać o zachowaniu jednostajnej prędkości oraz w miarę stałej odległości pomiędzy dyszą a przecinanym materiałem.
Materiały metalowe, które można ciąć tlenem: stal konstrukcyjna, niskowęglowa, niskostopowa, żelazo, wolfram, grubsze materiały wykonane ze zwykłej stali, blachy pokryte rdzą.
Cięcie mogą utrudniać podwyższone ilości materiałów dodatkowych w stali.
Zalety cięcia tlenem.
- szeroki zakres grubości ciętych materiałów i dobra jakość tego cięcia,
- możliwość cięcia pod różnymi kątami (także prostopadłymi),
- możliwość zautomatyzowania procesu,
- koszty eksploatacyjne oraz zakupu sprzętu są stosunkowo niewysokie.
Wady cięcia tlenem.
- niska prędkość cięcia,
- wysłużony czas przebijania przez materiał (konieczność wstępnego podgrzewania),
- szeroka strefa wpływu ciepła,
- brak możliwości cięcia stali wysokostopowych i o wysokiej zawartości węgla (z uwagi na temperaturę zapłonu).
Tagi: cięcie stali CNC, wycinanie CNC w metalu, systemy cięcia laserowego, cięcie laserem Jawor, cięcie plazmą Jawor, hartowanie laserowe Jawor, cięcie plazmowe CNC Złotów, laser arkusz przycinanie, laser metal przecinanie.