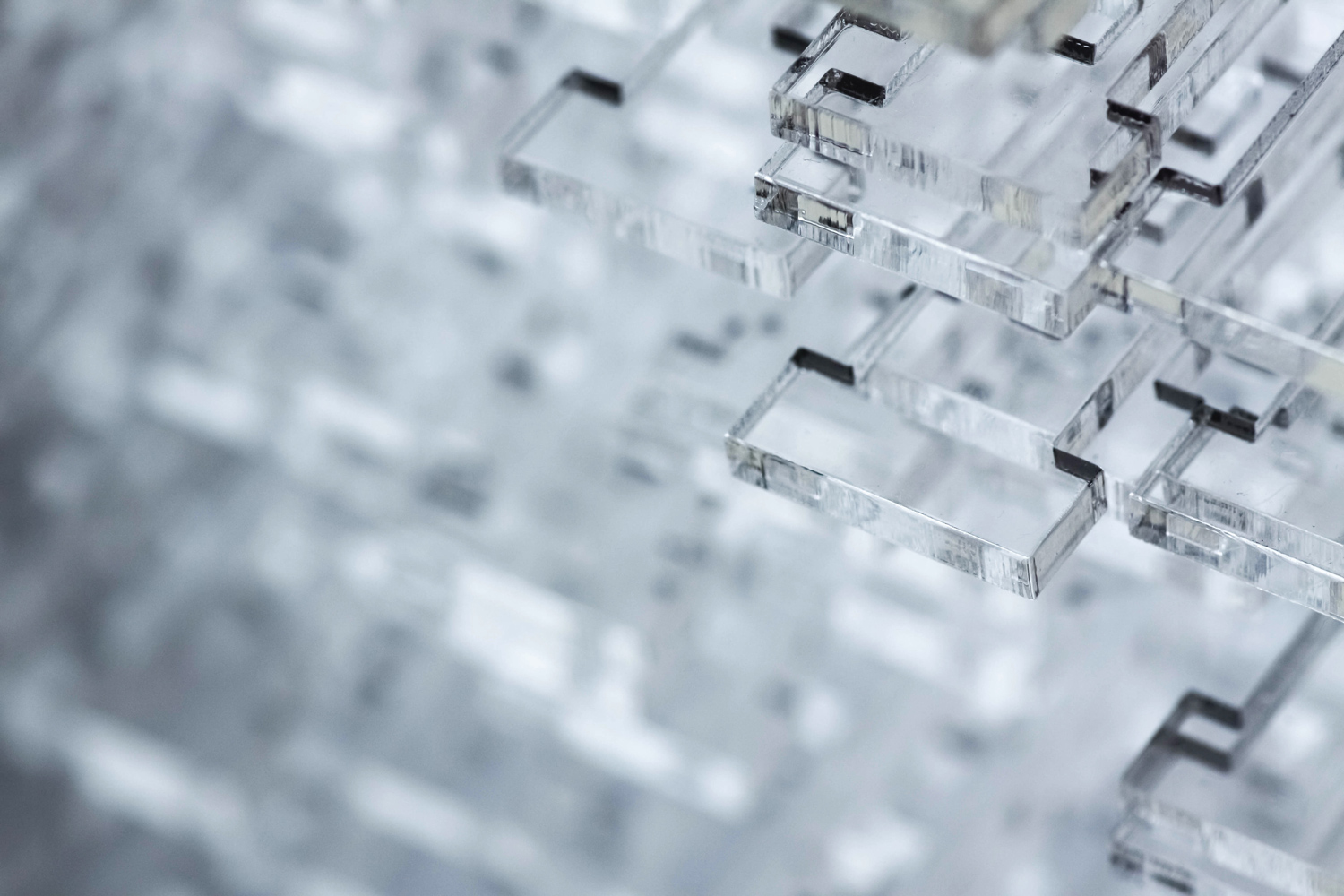
Laserowa obróbka tworzyw sztucznych – poradnik
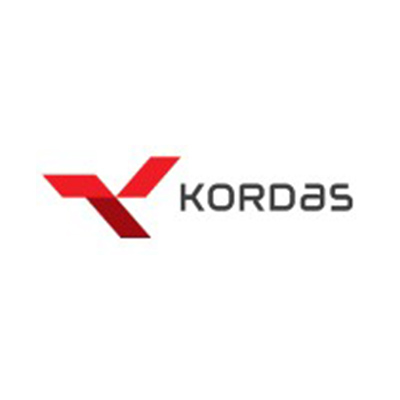
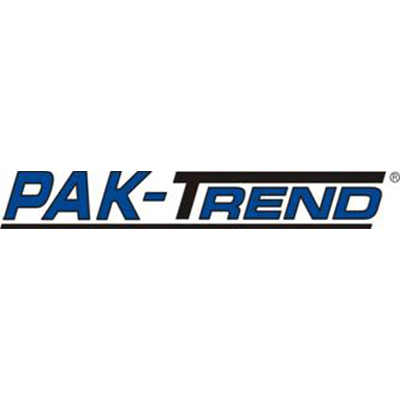
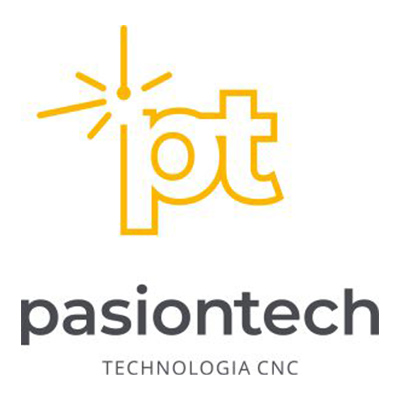
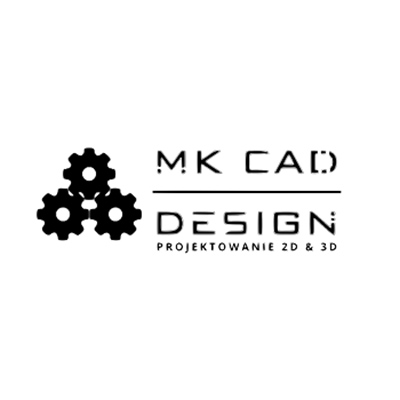
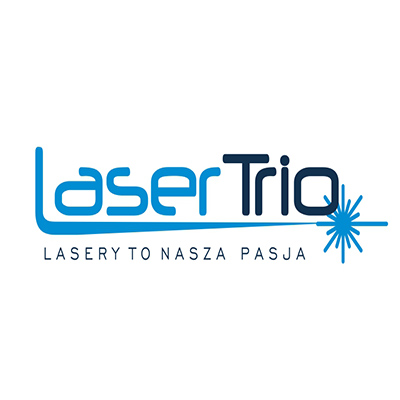
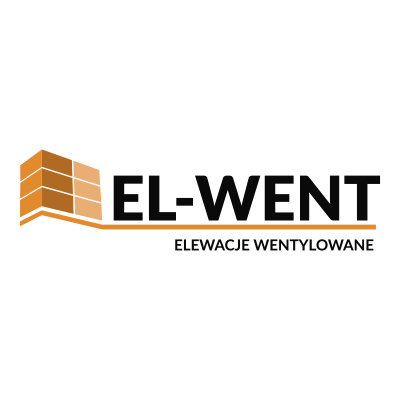

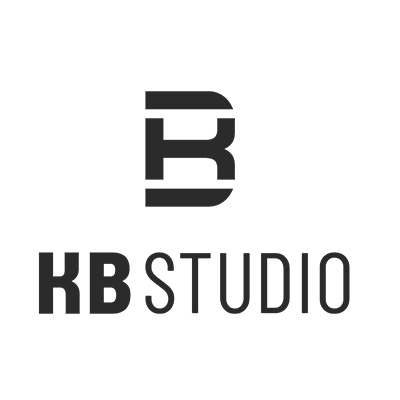
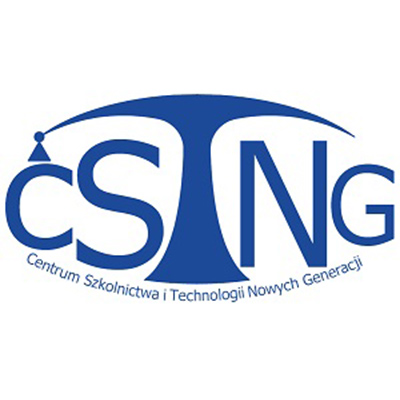
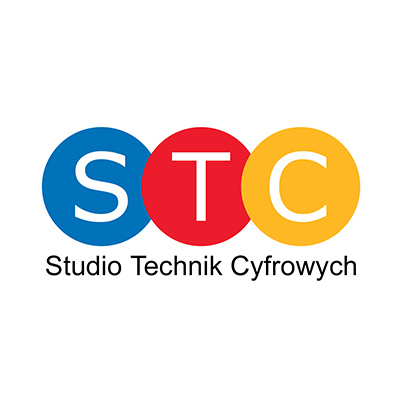
Laserowa obróbka tworzyw sztucznych.
Tworzywa sztuczne to materiały tanie, lekkie i proste w produkcji, odporne na korozję, jak również łatwe do formowania w dowolne kształty. Na linii produkcyjnej komponentów z tworzyw sztucznych technika laserowa – dzięki łatwości automatyzacji procesu – przychodzi ze swoimi rozwiązaniami jako opłacalna ekonomicznie alternatywa dla tradycyjnego cięcia, grawerowania, sklejania lub zgrzewania. Różnorodność źródeł laserowych i wspomniana łatwość automatyzacji tego procesu sprawiły, że laser stał się integralną częścią rynku obróbki tworzyw sztucznych, a sama obróbka CNC tworzyw sztucznych – jedną z najchętniej zamawianych usług.
Zastosowanie obrobionych laserowo tworzyw sztucznych.
Branży, w jakich znajdą zastosowanie obrobione laserowo tworzywa sztuczne jest tak naprawdę bez liku. Jednym z głównych rynków zbytu dla systemów laserowych są producenci wyświetlaczy, etykiet, liternictwa, firmy tnące folie sztuczne, przemysł motoryzacyjny, panele do użytku domowego, folie klawiatur, pluszowe tkaniny w przemyśle zabawkowym. Obróbka plastiku to szereg rozmaitych działań, obszarów, dziedzin i gałęzi.
Laserowa obróbka tworzyw sztucznych – inne przykłady:
- produkcja dowodów osobistych, identyfikatorów, szablonów, paneli LED, tabliczek informacyjnych, szyldów, uszczelek,
- cięcie folii ochronnych do ekranów dotykowych, cięcie akrylu, płyt poliwęglanowych,
- znakowanie rezystorów, reflektorów samochodowych, opraw okularów, guzików, laptopów, przewodów i kabli, opakowań, obudowy pieczątek, AGD, telefonów, plomb, aparatów słuchowych,
- wiele innych.
Wydajne przetwarzanie tworzyw sztucznych można uzyskać przy użyciu lasera CO2:
- trofea – cięcie i grawerowanie akrylu,
- membrany klawiatur – cięcie malowanych poliwęglanowych folii,
- filtry – cięcie poliestru,
- SMART-X – cięcie lekkich poliestrowych płyt,
- osłony ekranów – cięcie polietylenowych folii,
- PET-G – cięcie i frezowanie,
- przemysł lotniczy – cięcie aramidowych tkanin.
Laserowa obróbka tworzyw sztucznych – rodzaje.
Laserowa obróbka tworzyw sztucznych to przede wszystkim: cięcie, spawanie, znakowanie (w tym: grawerowanie).
A) Cięcie tworzyw sztucznych technologią laserową przynosi wiele korzyści i jest metodą tańszą i bardziej ekonomiczną w porównaniu do tradycyjnych technik rozdzielania detali. Do głównych cech laserowego cięcia tworzyw sztucznych zaliczamy:
- brak zużycia narzędzi,
- brak odłamków – nie trzeba czyścić pola roboczego urządzenia,
- bezdotykowa obróbka – brak uszkodzeń i zmniejszone odpady,
- brak potrzeby mocowania przetwarzanego materiału,
- równe krawędzie bez ponownej obróbki, kontury bez odkształceń,
- nie powoduje powstawania mikropęknięć w obszarze cięcia, ze względu na niskie obciążenie cieplne nie występuje zjawisko nadtopienia elementu,
- uzyskanie elementów o dowolnym kształcie i wysokiej dokładności wykonania,
- powtarzalność kształtów i wymiarów,
- optymalne wykorzystanie materiału,
- bezkontaktowy proces.
Wśród cięcia tworzyw sztucznych wyróżniamy między innymi: cięcie poliwęglanu laserem, cięcie folii laserem, cięcie gumy laserem (np. wycinanie uszczelek), wycinanie laserem HIPS, cięcie laserem dibondu.
B) Przy łączeniu tworzyw sztucznych metodą konwencjonalną jest – niedoskonałe, bo nie zawsze estetyczne oraz wymagające stosowania dodatkowych materiałów – klejenie. Lepszym rozwiązaniem jest z całą pewnością nowoczesna technika laserowa, umożliwiająca precyzyjne spawanie laserowe, podczas którego skoncentrowana wiązka energii powoduje nadtopienie krawędzi obu elementów, a roztopiony materiał tworzy trwałe połączenie między materiałami. Strefa wpływu ciepła jest na tyle mała, że nie następuje zmniejszenie wytrzymałości obu części. Jest również technika polegająca na spawaniu tworzyw nałożonych na siebie dzięki wykorzystaniu zjawiska transparentności materiału. Ognisko ustawia się w miejscu styku obu elementów, a doprowadzona energia sprawia, że nadtopieniu ulega tylko substancja nieprzepuszczająca promieniowania laserowego. Spoina powstaje w precyzyjny i szybki sposób, gwarantując dobrą wytrzymałość i wysoką szczelność połączenia.
C) Znakowanie laserowe tworzyw sztucznych (w tym: znakowanie laserowe na folii) w głównej mierze polega na odbarwieniu powierzchni elementu. Polimery o ciemnych kolorach obrabia się poprzez spienianie (materiał bazowy ulega częściowemu roztopieniu oraz zgazowaniu, powstałe pęcherzyki gazu tkwią na powierzchni zastygłej substancji, rozpraszając padające światło). Tworzywa o jasnej barwie są poddawane grawerowaniu (usuwane są kolejne warstwy materiału, a powstałe napisy są odporne na zużycie ścierne). Znakowanie za pomocą lasera to szybka, dokładna i powtarzalna metoda, pozwalająca nanosić na element dowolne symbole i znaki, niezależnie od kształtu powierzchni. Przy zastosowaniu odpowiednio szerokiej gamy produktów oraz wiązki o odpowiedniej długości fal, możliwe jest znakowanie praktycznie dowolnego tworzywa sztucznego.
Zalety laserowego znakowania:
- bezdotykowe możliwości przetwarzania materiału,
- doskonałe rezultaty, dokładność, trwałość, odporność na ścieranie i temperaturę,
- obszerne możliwości projektowania (możliwość nanoszenia wszelkiego rodzaju treści – logo, kody, numery serii, inne),
- możliwość znakowania najdrobniejszych detali i elementów, również w trudno dostępnych miejscach,
- duża przepustowość (znakowanie trwa kilka sekund).
Dzięki ogromnym możliwościom techniki laserowej, krótkiemu czasowi dostosowywania ustawień i dużej elastyczności narzędzi, obrabianie tworzyw sztucznych jest nie tylko pracą ciekawą, ale również korzystną i opłacalną.
Funkcje i zalety technologii laserowej w obróbce tworzyw sztucznych.
Jak wiadomo, laserowa obróbka tworzyw sztucznych ma wiele zalet. Do najważniejszych z nich należą:
- opłacalna produkcja,
- możliwość programowania produkcji taśmowej,
- bezdotykowe i niezawodne możliwości przetwarzania rozmaitych materiałów,
- doskonałe, perfekcyjne, precyzyjne rezultaty,
- możliwość zrezygnowania ze stosowania obróbki wykańczającej brzegi – laser bowiem pozostawia je idealnie gładkie,
- oszczędność materiału poprzez tzw. szybkie cięcia,
- duża przepustowość i szybkość procesu,
- niesamowite możliwości projektowania,
- trwałość.
Wadą jest przede wszystkim wysoki koszt inwestycyjny.
Rodzaje tworzyw sztucznych odpowiednie do obróbki laserowej.
Do laserowej obróbki tworzyw sztucznych nadają się następujące tworzywa:
- poliamid (PA) – to nazwa używana w odniesieniu do sztucznych lub technicznych żywic termoplastycznych, charakteryzujących się wysoką wytrzymałością, sztywnością i twardością; z uwagi na oporność na działanie środków chemicznych może być w łatwy sposób przetwarzany za pomocą laserowego plotera tnącego; cięcie laserowe poliamidu cechuje wysoka precyzja i bezkontaktowy proces; krawędzie są zgrzane podczas procesu cięcia termicznego i dzięki temu nie strzępią się, nie trzeba wykonywać żadnych dalszych procesów technologicznych, żeby detale nadawały się do dalszej produkcji; włókna poliamidowe są wykorzystywane do produkcji tkanin takich jak: żyłki, okrycia przeciwdeszczowe, bielizna czy artykuły gospodarstwa domowego;
- poliwęglan (PC) – materiał powszechnie stosowany do produkcji folii na przednie, dotykowe panele, wskaźniki instrumentów czy prędkościomierze; folie wykonane z tego syntetycznego materiału mogą być przetwarzane nawet do grubości 3 mm; bezdotykowy system obróbki przez wiązkę laserową i związane z tym gładkie krawędzie cięcia oraz wysoka precyzja to istotne argumenty za wykorzystaniem obróbki laserowej;
- polipropylen (PP) – jeden z najbardziej popularnych materiałów powszechnego użytku (zastosowanie: tkaniny i folie techniczne, wkładki filtracyjne, obicia mebli i siedzeń samochodowych), twardszy, bardziej sztywny i trwalszy niż polietylen; bardzo dobrze tnie się laserem, krawędzie są zawsze najwyższej jakości, bez zadziorów; proces jest bezdotykowy, zatem cięcie jest bez zniekształceń, o najwyższym stopniu precyzji;
- poliuretan (PUR) – wytworzony jest z tworzywa sztucznego lub żywicy syntetycznej; materiał wszechstronny, trwały, odporny na pleśń, w zależności od potrzeb i dostosowania może być twardy, kruchy lub elastyczny (np. sztywna pianka na podeszwach butów, gąbki izolacyjne lub do użytku domowego, miękka pianka poliuretanowa używana do wkładów opakowań); poliuretan stosowany jest także do obróbki folii i tkanin; bardzo dobrze tnie się za pomocą noża tnącego (plotera);
- poliformaldehyd (POM) – jest semikrystalicznym tworzywem termoplastycznym o właściwościach sprawiających, że w wielu przypadkach może być używany jako zamiennik materiałów metalicznych; znajduje się głównie w postaci folii, cienkich płyt lub arkuszy do cięcia, w elektronice stosowany jako opakowania; po obróbce laserem CO2 może być stosowany w inżynierii mechanicznej, przemyśle motoryzacyjnym oraz do produkcji mebli;
- polimid (PI) – często przedstawia się w postaci cienkich, elastycznych, półprzeźroczystych płyt, ale również jako warstwy izolacyjne ogniw magazynujących energie czy w postaci włókien do filtrowania gazów (ze względu na odporność na temperaturę, zarówno ekstremalnie niską (–256°), jak i bardzo wysoką (+400°), znajduje zastosowanie w sektorze lotniczym); folie z tego materiału mogą być laminowane, metalizowane lub pokrywane klejem; obróbka laserowa najczęściej odbywa się w miejscu na elementy elektroniczne i często w kombinacji z innymi częściami lub foliami;
- polistyren (PS) – w czystej postaci jest krystalicznie bezbarwnym, twardym, kruchym termoplastem o bardzo ograniczonej elastyczności; produkowany głównie w postaci płyt o powierzchni gładkiej lub z wytłoczonym wzorem; przez systemy laserowe przetwarzany jest głównie na folie i cienkie płyty (przykład zastosowań: opakowania z cienkiej folii, tworzenie modeli); dzięki swoim szczególnym właściwościom oraz niskiej cenie jest materiałem szeroko stosowanym w przemyśle reklamowym (lekkie talerze, znaki świetlne, stoiska targowe, kasetony, zawieszki, potykacze, ekspozytory POS, stojaki) oraz przemyśle (elementy opraw oświetleniowych, elementy lad chłodniczych, paletki na produkty spożywcze); duża elastyczność w przetwarzaniu, materiał nie musi być równomierny, najwyżej położone krawędzie mogą być obrabiane; obróbka odbywa się bezdotykowo, możliwe jest więc wycinanie nawet filigranowych detali;
- polimetakrylan metylu lub akryl (PMMA) – syntetyczny, przypominający szkło materiał termoplastyczny, idealny do cięcia i grawerowania laserem CO2; stosowany głównie w branży reklamowej oraz sektorze oznakowań i etykiet; pojawiające się opary PMMA podczas procesu laserowego są łatwo odsysane i filtrowane (jeśli są takie wymagania);
- poliester (PES) – syntetyczny materiał, szeroko stosowany w przemyśle (od tkanin odzieżowych i przemysłowych wyrobów włókienniczych, aż po tkaniny polarowe); znajduje zastosowanie w klawiaturach membranowych, foliach na przednie dotykowe wyświetlacze oraz foliach i tkaninach dystansowych;
- politereftalan etylenu (PET) – jest termoplastycznym, poliestrowym materiałem; stanowi surowiec do produkcji folii, tkanin i płyt, wykorzystywanych w różnych sektorach, np. jako meble czy folie izolacyjne; często używany jako tkaniny lub folie pod obróbkę laserem; dodatkowo występuje jeszcze PET Glikol (PETG) – materiał trudnopalny, odporny chemicznie, wytrzymały, praktycznie niezniszczalny, idealny do cięcia i znakowania laserem CO2; PET/PETG jest używany do ochrony maszyn, urządzeń i w przemyśle meblarskim;
- polichlorek winylu (PVC) – tworzywo sztuczne masowo wykorzystywane na rynku, bo wytwarzane jest w tani sposób i może mieć różnorodne zastosowanie; dostępny w postaci twardej PVC-U (nieplastikowy) i miękkiej PVC-P (plastikowy), bardziej elastycznej poprzez dodanie zmiękczaczy; jest to materiał niepalny i może być produkowany jako formy przejrzyste lub kolorowe, charakteryzuje się wytrzymałością mechaniczną i twardością; stosowany w budownictwie, przemyśle elektronicznym, mechanice i w branży reklamowej (tablice i elementy dekoracyjne); dodatek zmiękczaczy w PVC-P nadaje mu elastyczności, prawie jak guma, dlatego ma doskonałe własności tłumiące (wykorzystywany w reklamie, przemyśle opakowań, urządzeniach medycznych, przemyśle fotograficznym);
- polietylen (PE) – to jedno z najpopularniejszych tworzyw sztucznych, towarzyszące nam każdego dnia: w trakcie pracy, nauki, zabawy, podczas zakupów, gdy pakujemy towar do reklamówek; ma znaczną ilość odmian o różniących się cechach, najprostszy podział wyróżnia polietylen wysokiej gęstości (HDPE) i polietylen niskiej gęstości (LDPE); znajdziemy go w folii, torbach zakupowych, kapturach termokurczliwych, opakowaniach ogólnych, wieczkach opakowań, powłokach kartonowych pojemników na mleko, powłokach przewodów, wysokowydajnych workach średniej i małej wielkości; skrzynkach i pojemnikach, butelkach (na produkty spożywcze, środki czystości i kosmetyki), w zabawkach, kanistrach na benzynę, rurach i artykułach gospodarstwa domowego;
- poliarylosulfon (PSU, PPSU) – przezroczyste tworzywo termoplastyczne, o dużej wytrzymałości mechanicznej i sztywności, odporne na wysokie temperatury – ma możliwość długotrwałej pracy w wysokich temperaturach; konstruktorzy wybierają je również dzięki takim właściwościom jak: wysoka odporność na pełzanie (duża odporność jest zauważalna zarówno w wysokich, jak i w niskich temperaturach), wysoka stabilność wymiarowa, odporność na oddziaływanie procesu hydrolizy, wysoka odporność chemiczna; wykorzystywany w branży medycznej i farmaceutycznej, motoryzacji, automotive, branży paliwowej, branży chemicznej (suwaki do zaworów, detale w postaci kołnierzy, rurek, kadłuby pomp), w przemyśle spożywczym (naczynia i pojemniki do stosowania w kuchenkach mikrofalowych), przemyśle elektronicznym (złączki, korpusy cewek, izolatory o wysokich częstotliwościach, gniazda antenowe);
- polieteroketon (PEEK) – termoplastyczne, półkrystaliczne tworzywo konstrukcyjne o wielu zaletach: odporność na hydrolizę, doskonałe właściwości ślizgowe, dobre właściwości mechaniczne, odporność na promieniowanie, odporność chemiczna, odporność na pełzanie, odporność na ścieranie, wysoka sztywność, wysoka stabilność wymiarowa, wysoka temperatura użytkowa (260°C), uniwersalny materiał do obciążonych elementów; przykładowe zastosowania: adaptery do elementów elektronicznych, uchwyty instrumentów medycznych, zębniki transportujące, bloki łożyskujące;
- kopolimer akrylonitrylu, butadienu i styrenu (ABS) – jego najważniejszymi własnościami są: udarność i twardość, płynięcie, odporność termiczna; tworzywo ABS jest odporne na działanie wodnych roztworów kwasów, zasad, stężonego kwasu chlorowodorowego i fosforowego, alkoholi oraz olejów zwierzęcych, roślinnych i mineralnych; ulega natomiast stężonym kwasom: siarkowemu i azotowemu, rozpuszcza się w estrach, ketonach, acetonie i chlorku etylenu; jego przetwórstwo obejmuje procesy formowania wtryskowego i wytłaczania; znajduje zastosowanie w: motoryzacji (wewnętrzne panele drzwiowe, słupki, elementy foteli, kratki wlotu powietrza, deski rozdzielcze, obudowy lusterek), w sprzęcie (obudowy urządzeń kuchennych i odkurzaczy, panele sterowania sprzętu AGD), wytłaczaniu (płyty, brodziki łazienkowe, dachy do ciągników, obrzeża meblowe, wnętrza lodówek), inne (zabawki, dobra konsumenckie, telefony, kaski ochronne);
- silikon – materiał wytrzymały na ekstremalne temperatury, od bardzo wysokich po niskie; sprężysty i giętki, bardzo lekki, odporny na uszkodzenia; cechuje go: niepalność, odporność termiczna i chemiczna, odporność na promieniowanie ultrafioletowe, dobra izolacyjność i smarność; zastosowanie: wykorzystywany do produkcji akcesoriów kuchennych, w budownictwie (materiały uszczelniające i łączące, czynności wykończeniowe, budowlane, konstrukcyjne), w przemyśle (jako podstawowy surowiec do budowy form silikonowych), w kosmetyce (jako składnik szamponów, odżywek, stosowany również w podkładach do twarzy), we włókiennictwie (do preparacji włókien poliestrowych), w medycynie (do produkcji opatrunków, implantów piersi, soczewek kontaktowych, cewników), oleje, smary lub ich składniki, składniki żywic, do produkcji lakierów i kauczuków.
Rodzaje materiałów NIENADAJĄCE SIĘ do obróbki laserowej.
Przy obrabianiu laserowo poniższych tworzyw mogą powstać gazy trujące dla człowieka:
- PCW,
- winyl,
- poli-dwubromostyren,
- PTFE (teflon).
Przy obróbce tych tworzyw sztucznych sprawdzą się mechaniczne grawerki lub plotery do cięcia.
Obróbka laserowa akrylu.
Jednym z tworzyw sztucznych chętnie i powszechnie stosowanym w obróbce laserowej jest akryl, znany również pod wieloma innymi nazwami, jak: szkło akrylowe, szkło organiczne, PMMA, polymethyl methacrylate, potocznie plexiglas, pleksi, plexi, metaplex, żargonowo pleksa. Nazwy handlowe stosowane przez producentów to: Akrylon, Altuglas®, Limacryl®, Oroglas, P-Plex, PerClax, Perspex®, Plexpol, Setacryl®, Acrylite®, Setapan®, Lucryl®, Deglas®, Friacryl®, Hesa-Glas®, Resarit®, Satin Glass®, Setasand®, Setaletter®, Plexiglast® resist, CRYLON®, CRYLUX™.
Jeśli i Ty jesteś entuzjastą stosowania akrylu (zwanego też plexi/pleksi) i z racji swoich obowiązków dość często wbijasz w wyszukiwarkę któreś z haseł, jakie za chwilę wymienimy, na pewno dalsza część artykułu powinna być dla Ciebie interesująca i przydatna. Czytaj zatem dalej…
Jak się okazuje, jednymi z najczęściej wyszukiwanych zwrotów – dotyczących laserowej obróbki akrylu – są: „obróbka plexi”, „cięcie plexi”, „cięcie pleksi”, „ciecie pleksi”, „cięcie plexi laserem”, „cięcie pleksi laserem”, „cięcie laserem plexi”, „cięcie laserem pleksi”, „cięcie laserowe plexi”, „cięcie laserowe pleksi”, „laserowe cięcie plexi”, „laserowe cięcie pleksi”, „wycinanie plexi”, „wycinanie pleksi”, „wycinanie w plexi”, „wycinanie w pleksi”, „wycinanie z plexi”, „wycinanie z pleksi”, „wycinanie laserowe plexi”, „wycinanie plexi na wymiar”, „cięcie plexi na wymiar”, „docinanie plexi”, „docinanie plexi na wymiar”, „grawerowanie plexi”.
Pleksi należy do rodziny tworzyw termoplastycznych. Jest to materiał tak często i entuzjastycznie stosowany przez producentów, że należy mu się chwila uwagi i oddzielny opis.
Głównym składnikiem tego tworzywa jest poli(metakrylan metylu). Niektóre rodzaje zawierają też pewne ilości innych poliakrylowych polimerów i kopolimerów. Jest on przezroczysty, sztywny i odporny na promienie UV. Jego zaletą jest na pewno stosunkowo niska temperatura depolimeryzacji, co wiąże się z łatwym recyklingiem, z kolei wadą – niewielka twardość, przez co powierzchnia płyt łatwo ulega zarysowaniu, szczególnie widocznemu w przypadku wykończenia na połysk.
Rodzaje płyt akrylowych.
Istnieją dwie metody produkcji akrylu: odlewanie (GS) i wytłaczanie (XT). Obie poddają się dobrze obróbce, jednakże z uwagi na odrębne właściwości, pod wpływem wiązki lasera zachowują się inaczej.
- akryl lany (GS)
Akryl wylewany zazwyczaj postrzegany jest jako jakościowo lepszy. Proces jego produkcji jest bardziej kosztowny, toteż jego cena końcowa jest wyższa niż w przypadku akrylu wytłaczanego. Powstaje, gdy płynny akryl wlewany jest do form o różnych rozmiarach i kształtach. Jest jednolitym materiałem, wolnym od naprężeń, z jednakowymi właściwościami we wszystkich kierunkach. Rezultatem cięcia laserowego pleksy wylewanej są gładkie, polerowane, zatopione krawędzie bez ostrych brzegów. Wadą jest dużo większa tolerancja grubości płyty niż w przypadku akrylu ekstrudowanego oraz mniejsza gama kolorów i grubości. Dobrze poddaje się laserowemu grawerowaniu – grawerunki są idealnie białe, a powierzchnie uzyskują efekt mrożonego szkła. Akryl odlewany wykorzystywany jest do produkcji większości dostępnych na rynku nagród.
- akryl wytłaczany, zwany inaczej ekstrudowanym (XT)
Wytłaczanie akrylu polega na ekstruzji, czyli wyciskaniu masy przez dyszę o wybranej grubości. Otrzymujemy w ten sposób materiał niejednolity, o licznych naprężeniach wewnętrznych (mających wpływ na jego zachowanie się podczas obróbki i dalszego użytkowania) i właściwościach mogących się zmieniać zależnie od kierunku cięcia. Ma również niższą tolerancję grubości (w granicach ±5%), doskonale więc sprawdza się w zastosowaniach mających podłączenie elektryczne. Efektem laserowego cięcia są gładkie, polerowane krawędzie, niestety często występują tu też ostre występy pomiędzy krawędzią cięcia a powierzchnią materiału. Pleksa wytłaczana przy większym naprężeniu ma skłonność do pękania w miejscach cięcia laserowego. Jest tańsza, dlatego często stosowana jest w produkcji masowej. Z uwagi na niższy punkt topnienia nie potrzebuje tak dużej mocy lasera, jak akryl lany, przy tej samej grubości płyty. Trudno się ją graweruje laserem, a rezultaty takiej obróbki są matowo szare.
Konfiguracja urządzenia przy obróbce pleksi.
Przy odpowiednim oprogramowaniu i ustawieniu maszyny możliwe jest uzyskanie optymalnych rezultatów, niewymagających żadnych poprawek.
- moc lasera
Potrzebna moc lasera uzależniona jest od grubości materiału i oczekiwanej wydajności pracy maszyny. Im wyższa, tym szybszy i wydajniejszy jest proces cięcia. Aby praca była efektywna, należy użyć mocy przynajmniej 60 W. Zasada jest taka: na 1 mm grubości (przy grubości do 20-25 mm) najlepszą jakość daje 10 watów mocy lasera.
- soczewka
Niezwykle istotną sprawą jest wybór odpowiedniej soczewki. Im materiał jest grubszy, tym dłuższa powinna być ogniskowa soczewki. Z reguły wykorzystuje się soczewkę 2,5″, przy grubszych materiałach – 4″ lub 5″. W przypadku materiałów o grubości powyżej 8 mm pomocne jest ogniskowanie wiązki lasera nie na powierzchni, lecz wewnątrz materiału – z reguły około 1/3 grubości materiału poniżej jego powierzchni. Pomoże to uzyskać równe, jednolite cięcie.
Żeby chronić soczewkę, a jednocześnie uzyskać optymalną jakość cięcia, należy stosować dysze o dużej średnicy. Przy stosowaniu dyszy o małej średnicy lub silnego nadmuchu, istnieje ryzyko matowienia krawędzi cięcia. Wskutek zbyt szybkiego wystygnięcia materiału, wykończenie brzegów będzie miało mleczne zabarwienie.
- właściwy stół
Stół powinien zapewniać dobry przepływ powietrza nad i pod materiałem oraz pochłaniać odbicia wiązki lasera od stołu. Dobry przepływ powietrza umożliwia szybkie usunięcie powstałych podczas cięcia gazów oraz – w przypadku grawerowania – pyłów. Dobrym rozwiązaniem jest stół do cięcia z akrylowymi lamelami lub akrylową kratownicą, w zależności od wielkości obrabianego przedmiotu. Do cięcia grubszych płyt akrylowych (o grubości przynajmniej 6 mm) oraz do części szerszych niż 100 mm zalecany jest ten pierwszy – skutecznie zapobiega on odbiciom wiązki lasera podczas cięcia. W przypadku węższych części bardziej praktyczny będzie stół do cięcia z akrylową kratownicą lub stół podciśnieniowy z akrylową kratownicą w formie nakładki, ponieważ w ten sposób części poddawane obróbce pozostaną w pozycji płaskiej po zakończeniu cięcia. Płyty grubsze niż 8 mm wymagają już użycia innej wersji stołu.
- system wyciągowy
Aby powstałe w trakcie cięcia opary jak najszybciej odprowadzić z wnętrza maszyny, niezbędne jest zastosowanie odpowiedniego systemu wyciągu. Jest to warunek bezwzględnie konieczny, aby pozwolić na osiągnięcie wysokiej jakości rezultatów cięcia (polerowanych krawędzi). Nigdy nie należy zostawiać bez nadzoru uruchomionego urządzenia, gdyż niesprawna wentylacja i za słaby wyciąg powietrza mogą doprowadzić do zapłonu oparów i w rezultacie pożaru.
Parametry laserowego cięcia akrylu.
Do cięcia plexiglasu laserem potrzebna jest większa częstotliwość niż podczas cięcia np. drewna. Dzięki temu brzegi cięcia roztapiają się jednolicie, dając czysty, wypolerowany efekt. Przy akrylu lanym (GS) polecana częstotliwość to 5000–20000 Hz, przy wytłaczanym (XT) – nie większa niż 5000 Hz.
Ustalenie idealnych parametrów jest bardzo ważne, jeżeli chcemy w sposób bezpieczny i wydajny pracować ze szkłem organicznym. Dlaczego? Jeżeli częstotliwość będzie za niska, na brzegach cięcia pojawi się tzw. efekt falowania, czyli drobne nierówności. Aby temu zapobiegać, trzeba zwiększyć lub obniżyć częstotliwość prędkości cięcia. Należy też mieć na uwadze, że niewystarczająca prędkość cięcia może spowodować powstanie nacięcia, co zwiększa ryzyko zapalenia się materiału.
Parametry laserowego grawerowania akrylu.
Akryl graweruje się dobrze przy wysokiej szybkości i niewielkiej mocy urządzenia. Do znakowania akrylu wystarczy niewielka moc lasera, zastosowanie zbyt dużej mocy może prowadzić do zniekształcenia materiału. Sprawdza się tutaj zatem reguła „mniej znaczy więcej” – najlepsze rezultaty osiąga się poprzez niewielkie „zarysowanie” powierzchni, co daje ładny, biały grawerunek. Zastosowanie zbyt dużej mocy spowoduje, że efekty będą głębokie, ale nie białe.
Płyty akrylowe zazwyczaj graweruje się od strony tylnej, co daje lepszą jakość i atrakcyjny wygląd produktu końcowego, a przy okazji grawerunek zabezpieczony jest przed działaniem czynników zewnętrznych. Trzeba pamiętać, że wzór będzie odbiciem lustrzanym, dlatego przed wysłaniem projektu do lasera należy przygotować w edytorze lub w ustawieniach drukowania lustrzane odbicie docelowej grafiki.
Ustawienia grafiki i oprogramowania.
Dla uzyskania optymalnych efektów obróbki trzeba również wziąć pod uwagę odpowiednie ustawienia grafiki i oprogramowania.
- ograniczona liczba kształtów
Aby laser mógł pracować jednostajnie i bez niepotrzebnych przestojów, należy do minimum ograniczyć liczbę kształtów w konturze.
- właściwy wybór punktu początkowego
Punkty początkowe zawsze powinny znajdować się w rogu, gdzie są mniej widoczne. Dlaczego? Miejsce początkowe, gdzie laser nacina materiał, zawsze będzie dostrzegalne – tego nie da się uniknąć. Szczególnie zauważalne są punkty znajdujące się na prostych liniach lub pośrodku łuku. Z tego powodu wybieramy te jak najmniej widoczne miejsca.
- określenie kolejności zadań cięcia
Kolejność zadań cięcia sprawdzić można w programie graficznym (CorelDraw, Adobe Illustrator), w rozwijanym menu – zawsze zaczynać się ona będzie od dołu do góry. Kolejność poszczególnych zadań cięcia może mieć wpływ na jakość większych ilości przedmiotów. Jeśli na obszarze roboczym cięte są duże ilości mniejszych przedmiotów, materiał będzie się mocno rozgrzewał w danym miejscu, co niesie ze sobą ryzyko zapalenia. Jeżeli wycinanych jest więc dużo małych wzorów z jednej, dużej płyty, wskazane jest uporządkowanie poszczególnych części, tak aby materiał zdążył wystygnąć pomiędzy cięciami.
Dodatkowe możliwości doposażenia systemu laserowego do obróbki PMMA.
Funkcjonalności mogące zoptymalizować pracę przy obróbce plexi to między innymi:
- połączenie cięcia laserowego z modułem frezującym równolegle na jednej maszynie,
- wiele rozmiarów stołów roboczych, dopasowanych do wymiarów dostępnych na rynku formatów materiałów,
- wiele funkcji automatyzacji (celem optymalizacji produkcji),
- specjalna konstrukcja stołu roboczego (celem uniknięcia refleksów wiązki lasera oraz optymalizacji obróbki),
- system odprowadzania dymu z możliwością zamontowania filtra,
- system optyczny do rozpoznawania znaczników drukarskich – dla drukowanych materiałów PMMA,
- możliwość grawerowania oraz wykonywania płaskorzeźb na całym polu roboczym urządzenia.
Zalety systemów laserowych do obróbki akrylu.
Stosowanie technologii laserowej to w zasadzie same korzyści:
- przezroczyste jak szkło, krystalicznie czyste, idealnie gładkie krawędzie cięcia w jednym przejściu roboczym – nawet w wewnętrznych konturach obrabianego detalu, bez konieczności polerowania,
- brak konieczności zaciskania i mocowania materiału,
- bezdotykowa obróbka, a zatem mniejsze uszkodzenia i straty materiału,
- nie ma wiórów, mniej zanieczyszczeń do usunięcia, niższe nakłady przy czyszczeniu,
- praktycznie pozbawione promienia kontury wewnętrzne we wszystkich grubościach i typach szkła akrylowego,
- możliwość obróbki akrylu z folią ochronną, co pozwala zabezpieczać oraz unikać uszkodzeń,
- brak zużycia narzędzi – wysoka i stała jakość cięcia w bardzo długim czasie,
- możliwość kombinowanej obróbki narzędziem frezującym i laserem CO2 w jednym urządzeniu,
- wielkości stołu pasujące do wszystkich formatów płyt PMMA dostępnych w handlu,
- grawerowanie wielkoformatowe (także reliefowe) na całej powierzchni obróbczej.
Zastosowanie obrabianych laserowo płyt akrylowych.
Akryl jest materiałem idealnym do obróbki – przez co i chętnie stosowanym – w wielu dziedzinach:
- litery na szyldy i tabliczki znamionowe, oznakowania,
- nagrody oraz gadżety reklamowe i promocyjne (napisy, stojaki, reklamy, ekspozytory),
- przedmioty dekoracyjne (akcesoria, design),
- grafiki na torty i ciasta,
- ozdoby świąteczne,
- makiety architektoniczne,
- drobne przedmioty użytkowe, pojemniki, pudełka,
- elementy maszyn i urządzeń,
- prototypy,
- jubilerstwo i moda (pierścionki, kolczyki, wisiorki, zawieszki, guziki, akcesoria),
- zadaszenia, świetliki,
- okna samolotów, pojazdów, statków,
- światłowody,
- płyty o specjalnym przeznaczeniu (ekrany przeciwhałasowe, antytermiczne, płyty fluorescencyjne, tarcze policyjne i wiele innych).
Obróbka laserowa – zleć u nas!
Różnorodność dostępnych tworzyw sztucznych wymusza stosowanie różnych metod ich obróbki. Nie wszystkie z nich spełniają wymagania rynku dotyczące precyzji, ekonomii, a także łatwości integracji z rozwiązaniami sieciowymi. Nic więc dziwnego, że tradycyjne metody coraz częściej ustąpić muszą pierwszeństwa nowoczesnym rozwiązaniom. Śmiało można powiedzieć, że urządzenia tnące laserem to zdecydowani liderzy w wyścigu o miano najlepszej maszyny do laserowej obróbki tworzyw sztucznych. Gwarantują bezdotykową pracę, szybki proces i wiele możliwości zastosowań, nieograniczonych ani kształtem, ani powierzchnią obrabianego przedmiotu. Laser nie wpływa na strukturę i właściwości ciętego materiału, nie zużywa się, nie generuje odpadów i gwarantuje stałą wysoką jakość powtarzalnych cięć w skali masowej. Całą maszynę reguluje się w sposób prosty, dane do programu wprowadza się łatwo – czy można chcieć czegoś więcej? Chyba nie. Można zatem stwierdzić, że jest to urządzenie niemal perfekcyjne. A u nas znajdziesz ich pod dostatkiem. Lasery z całej Polski czekają w gotowości, by realizować Twoje pomysły i zlecenia. Do dzieła zatem!
Pozostałe tagi: obrobka laserowa, obróbka cieplna plexi, filtry do obróbki laserowej, laser przycinanie arkusz, znakowanie lusterek Wrocław.