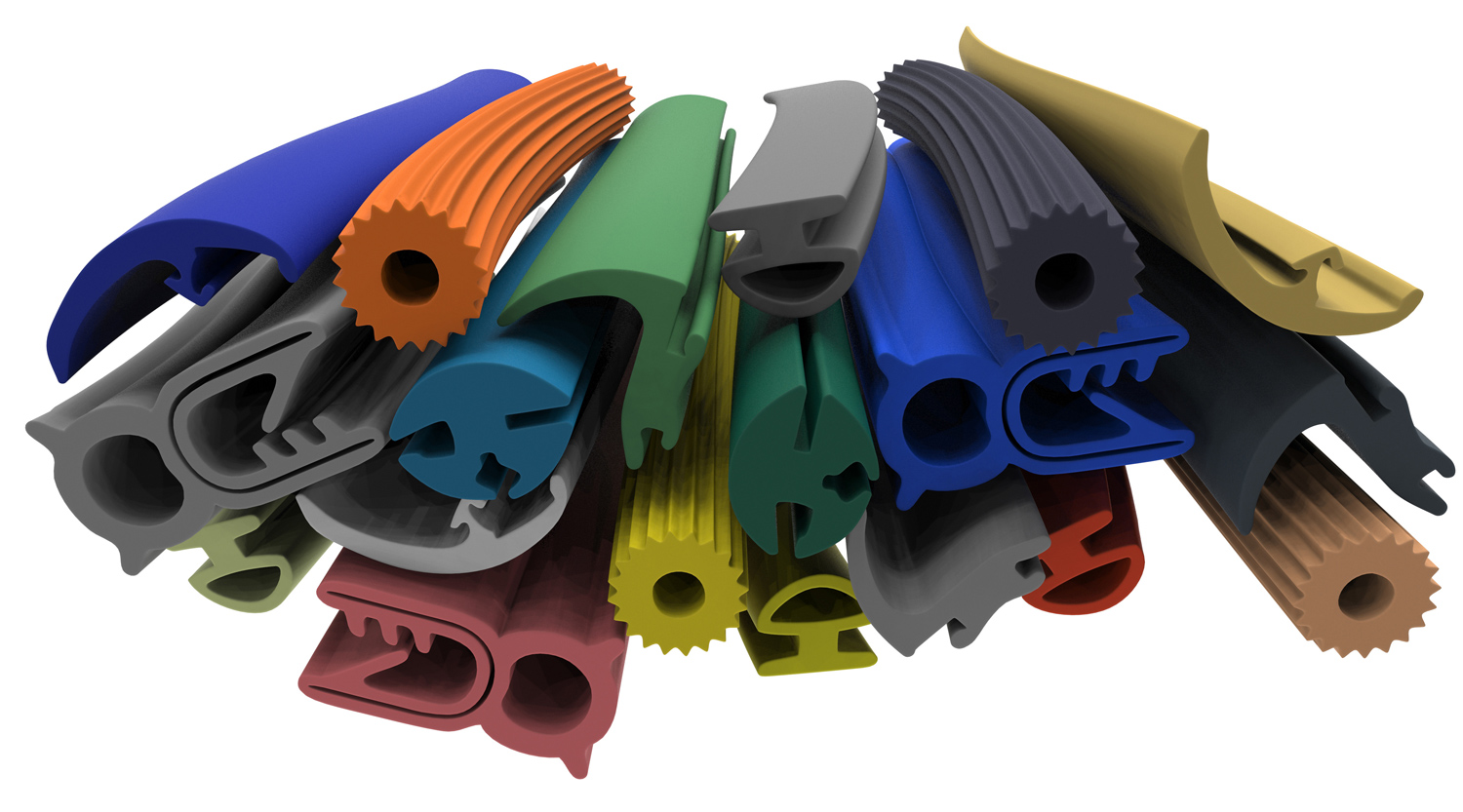
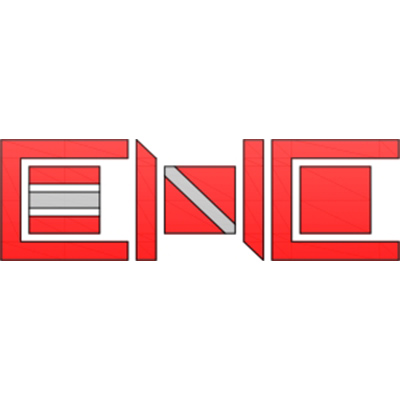
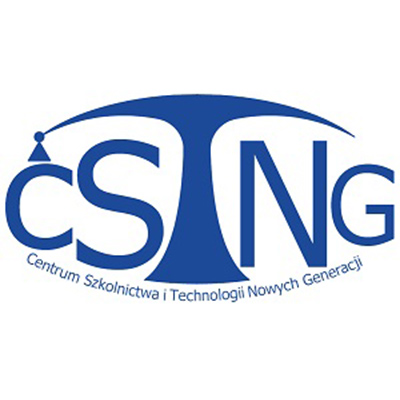
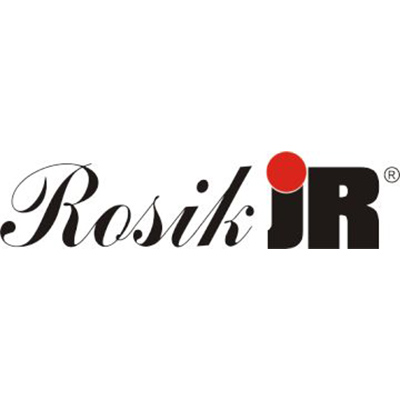
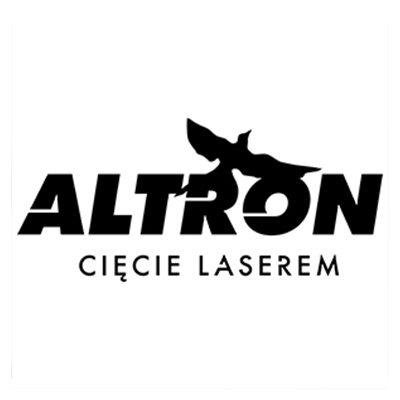
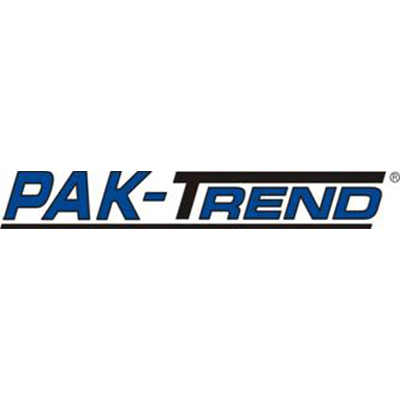
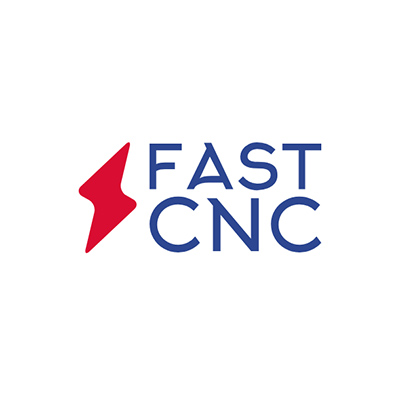
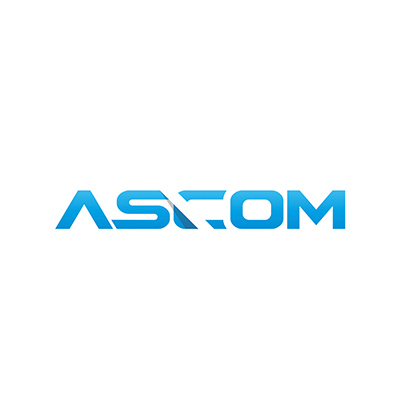
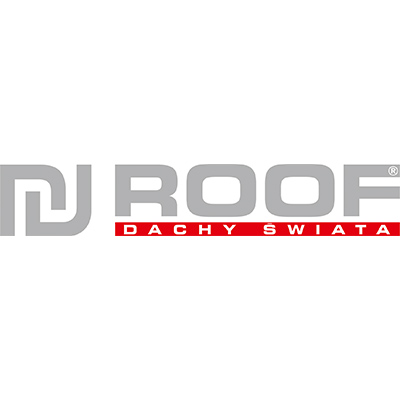

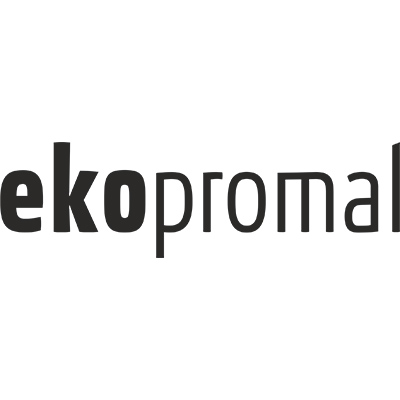
Jak działa LaserTrade?
Skorzystaj z formularza "Zapytanie ofertowe" lub "Wyślij zapytanie". Firmy natychmiast otrzymają powiadomienie o konieczności przygotowania wyceny. Oferty otrzymasz na adres e-mail. Jeżeli oferta jest dla Ciebie atrakcyjna, wystarczy, że skontaktujesz się z wybraną firmą i nawiążesz współpracę. Z LaserTrade korzystasz bezpłatnie.
Realizujemy wytłaczanie tworzyw sztucznych: LDPE, HDPE, PP, PA6, PUR, PCV, PS, PS, ABS, PMMA, PC oraz innych.
Do Twojej dyspozycji są wytłaczarki do tworzyw sztucznych z całej Polski. Wykonasz u nas: uszczelki o różnych kształtach, w tym profile z pustymi komorami, profile wargowe, kształtowniki, tuby rurowe, pojemniki, kroplówki, profile specjalne z przeznaczeniem do oświetlenia LED oraz inne według Twoich potrzeb.
Dlaczego wybrać wytłaczanie tworzyw sztucznych u nas?
Odpowiedź jest prosta.
Korzystanie z platformy umożliwia Ci wysłanie zapytania do wielu firm jednocześnie.
Oferty od Wykonawców – na wytłaczanie tworzyw sztucznych – będą zestawione w Twoim Panelu. Wystarczy wybrać najlepszą i nawiązać współpracę.
Znajdziesz tu wytłaczarki do PCV oraz wielu innych materiałów.
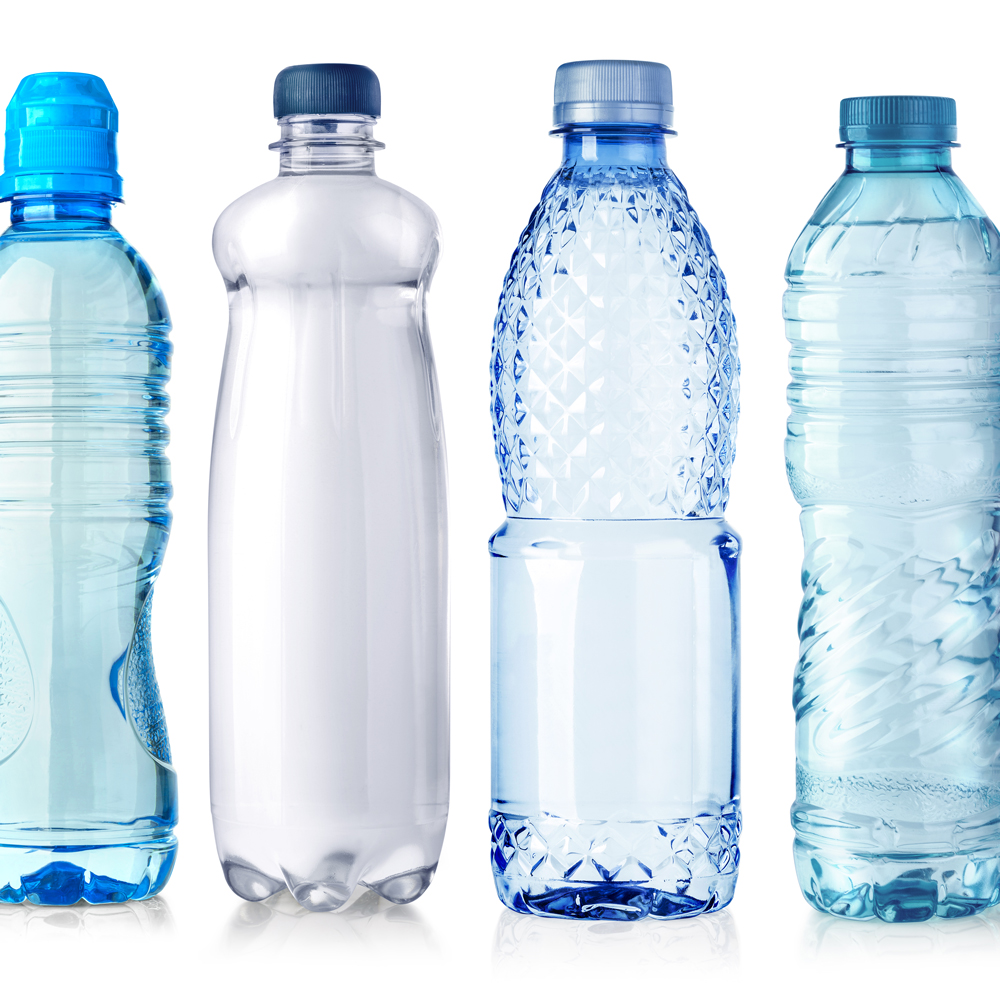
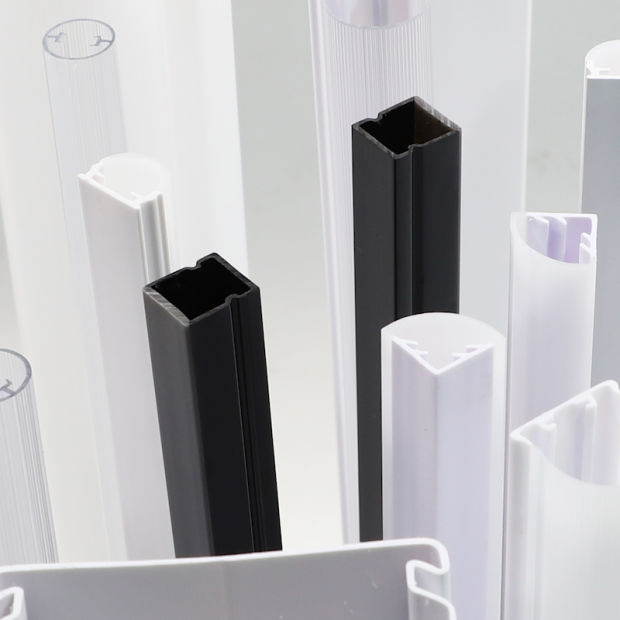
Gotowy na wytłaczanie tworzyw sztucznych?
Nie trać czasu.
Jeżeli jesteś gotowy dodać swoje pierwsze zapytanie o wytłaczanie tworzyw sztucznych, rozpocznij proces, a resztą zajmiemy się my!
Skorzystaj z bezpłatnej wyceny przygotowanej przez wiele firm jednocześnie.
Wytłaczanie tworzyw sztucznych – usługa.
Nowatorski park maszynowy (m.in. wytłaczarki PCV) wraz z odpowiednio dobraną technologią stanowią gwarancję wysokiej jakości produktów i usług produkcji jednostkowej i seryjnej. Oferujemy produkcję zarówno prostych, jak i bardziej złożonych elementów wykonanych z tworzyw sztucznych. Zajmujemy się także wytwarzaniem części prototypowych. Precyzyjna obróbka możliwa jest dzięki współpracy z naszymi Partnerami z całej Polski, którzy dysponują szerokim parkiem maszynowym z setkami maszyn sterowanych numerycznie, gotowych do pracy i działających w najróżniejszych technologiach.
Gdzie stosuje się wytłaczanie tworzyw sztucznych?
Wytłaczane profile wykorzystywane są głównie w branży budownictwa: rury, profile, płyty, folie. W procesie wytłaczania wykorzystywanych jest wiele części konstrukcyjnych. Przy wytłaczaniu profili z polichlorku winylu (PVC) niezbędna jest odporność na korozję, a przy produkcji profili wzmocnionych – odporność na zużycie.
Wytłaczanie umożliwia wykonywanie bezkońcowych uszczelek o różnych kształtach: profile z pustymi komorami, profile wargowe oraz połączenie jednych i drugich. Można też wytłaczać: kształtowniki, tuby rurowe, pojemniki, kroplówki, profile specjalne z przeznaczeniem do oświetlenia LED.
Na jakich materiałach pracujemy?
Jeśli zastanawiasz się, jakie tworzywa sztuczne można stosować do obróbki metodą wytłaczania, to spieszymy poinformować, że odpowiednie będą:
- LDPE,
- HDPE,
- PP,
- PA6,
- PUR,
- PCV,
- PS,
- ABS,
- PMMA,
- PC
- oraz inne.
Na czym polega wytłaczanie tworzyw sztucznych?
Wytłaczanie tworzyw sztucznych jest operacją ciągłą otrzymywania wyrobów lub półwyrobów (w postaci profili, płyt lub folii) z tworzyw polimerowych, w której gorący, uplastyczniony – w układzie uplastyczniającym wytłaczarki – materiał jest przeciskany przez odpowiednio ukształtowany ustnik, znajdujący się w głowicy, w efekcie tworząc profil o pożądanym kształcie. Osiąga się przy tym wydajności powyżej 1000 kg/h.
Proces wytłaczania przeprowadzany jest w celu formowania i mieszania. Materiałem wyjściowym są tworzywa w postaci granulatu, proszku, przemiału, aglomeratu. Wsadza się je do podgrzewanego cylindra, tam ulegają plastyfikacji i homogenizacji, by następnie móc przejść przez głowicę wytłaczającą, a jeszcze później przez kalibratory formujące gotowy wyrób, którym są np. rury, profile, płyty, folie. Wytłoczka zostaje schłodzona, a później cięta na odcinki o wymaganym wymiarze lub nawijana na bębny, szpulki itd., aby następnie można ją było nanieść w miejscu montażu.
Wytłaczanie przeprowadza się w urządzeniach zwanych wytłaczarkami (m.in. wytłaczarka PCV), które składają się z trzech układów: napędowego (silnika, przekładni), sterowania (mocy, temperatury itp.), plastyfikującego (zasobnika, cylindra, ślimaka, grzejników, wentylatorów). Ich zadanie polega na dostarczeniu do głowicy odpowiednio ujednorodnionego tworzywa – przy określonym natężeniu przepływu (wydajności procesu), ciśnieniu i temperaturze. Wyposażone są one w podajnik (zasobnik na surowiec) – i mogą to być dozowniki wolumetryczne, czyli objętościowe lub grawimetryczne, czyli wagowe – oraz komponenty pomocnicze (np. barwniki do tworzyw sztucznych).
Do przemieszczania tworzywa stosuje się przenośniki ślimakowe, tzw. ślimaki.
Układ plastyfikujący wytłaczarki złożony jest z jednego lub dwóch ślimaków plus cylindra. W zależności od rodzaju przetwarzanego surowca stosuje się różnego rodzaju ślimaki.
Rodzaje ślimaków:
• stożkowe,
• równoległe,
• współbieżne,
• przeciwbieżne.
Rodzaje wytłaczarek:
• wytłaczarka do tworzyw sztucznych jedno- i dwuślimakowa,
• wytłaczarka tworzyw sztucznych stożkowa i równoległa,
• wytłaczarka współbieżna i przeciwbieżna.
Odmiany procesów wytłaczania:
- konwencjonalne,
- auto–termiczne – ciepło dostarczane przez tarcie,
- powlekające – podciśnieniowe i ciśnieniowe,
- porujące – do układu uplastyczniającego dodaje się porofor, czyli środek spieniający,
- z rozdmuchem – swobodne (w ten sposób otrzymuje się rękaw foliowy),
- z rozdmuchem – z ograniczeniem mechanicznym (w ten sposób otrzymuje się pojemniki),
- z napełnianiem – np. kroplówki z granulowaniem – w wodzie lub powietrzu, z proszku robi się granulat,
- współwytłaczanie – koekstruzja kilku warstw.
Zautomatyzowane wytłaczanie PCV i innych materiałów – zleć!
Poprzez zastosowanie wytłaczania prowadzonego przez robota można zautomatyzować produkcję i uczynić ją wydajniejszą i elastyczniejszą. W tym przypadku dysza zamontowana jest w ruchomy sposób na robocie, a nie na wytłaczarce. Wytłaczarka połączona jest z dyszą za pomocą ogrzewanego węża o stabilnym ciśnieniu. Robot z dyszą podąża przewidzianym torem na podzespole. Prędkość przepływu materiału musi tu zostać zsynchronizowana z ruchem robota, a zatem potrzebne są indywidualne rozwiązania (nie produkty standardowe). Zaletami takiego sposobu pracy jest możliwość połączenia dwóch etapów procesu – wytłaczania profilu i montażu – w jeden, co pozwala na skrócenie czasu taktowania, większą elastyczność i bardziej opłacalną produkcję. Wśród Partnerów mamy także specjalistów od zautomatyzowanego wytłaczania.
Jeśli chciałbyś nawiązać współpracę i zlecić wytłaczanie tworzyw sztucznych to jesteśmy miejscem idealnym do tego. Zrzeszamy setki firm partnerskich z całego kraju, dysponujących szerokim parkiem maszynowym i najnowocześniejszymi technologiami. Zapewniamy szybki, łatwy i bezpośredni kontakt z całą siecią partnerską, a oferty wykonania zapisują się w uporządkowany sposób w jednym miejscu – Twoim osobistym Panelu Klienta. Można je wygodnie posortować według ważnych dla siebie kryteriów. Po wybraniu Wykonawcy zrealizujesz zamówienie z dostawą prosto pod drzwi.
Jaki jest przebieg procesu wytłaczania?
Podczas procesu wytłaczania tworzywo polimerowe w formie proszku bądź granulatu dozowane jest do zasobnika, czyli leja zasypowego wytłaczarki, skąd grawitacyjnie, przy pomocy ślimaka, przenoszone jest do dalszej części maszyny. Potem trafia do układu formującego, czyli głowicy, gdzie w części ogrzewanej ulega stopieniu, a następnie homogenizacji materiałowej i termicznej. Na końcu uplastyczniona, jednorodna masa materiałowa jest formowana przy użyciu ustnika w dowolny kształt.
Jakie są techniki wytłaczania?
Wśród odmian procesów wytłaczania warto wspomnieć o: konwencjonalnym, powlekającym (ciśnieniowym i podciśnieniowym), porującym (gdy do układu uplastyczniającego dodaje się porofor), autotermicznym (gdy ciepło dostarczane jest przez tarcie), z granulowaniem, z napełnianiem, z rozdmuchiwaniem (swobodne bądź z ograniczeniem mechanicznym), a także o współwytłaczaniu.
Jakie są wady i zalety wytłaczania?
Proces wytłaczania ma zarówno zalety, jak i wady. Zaletami są: możliwość stworzenia skomplikowanych i gotowych do użytkowania wyrobów podczas jednej operacji technologicznej, bez konieczności obróbki wykańczającej; możliwość automatyzacji i komputeryzacji procesu oraz produkcji masowej; wysoka estetyka, jakość oraz powtarzalność; niska pracochłonność i niewielka emisja szkodliwych substancji. Wśród słabych stron procesu należy wskazać na: spore nakłady finansowe potrzebne na oprzyrządowanie i wdrożenie do produkcji nowego wyrobu; długi czas przygotowania i nieekonomiczność przy krótkich seriach produkcyjnych; brak homogenizacji materiałowej przy zastosowaniu wielu tworzyw w jednym procesie.