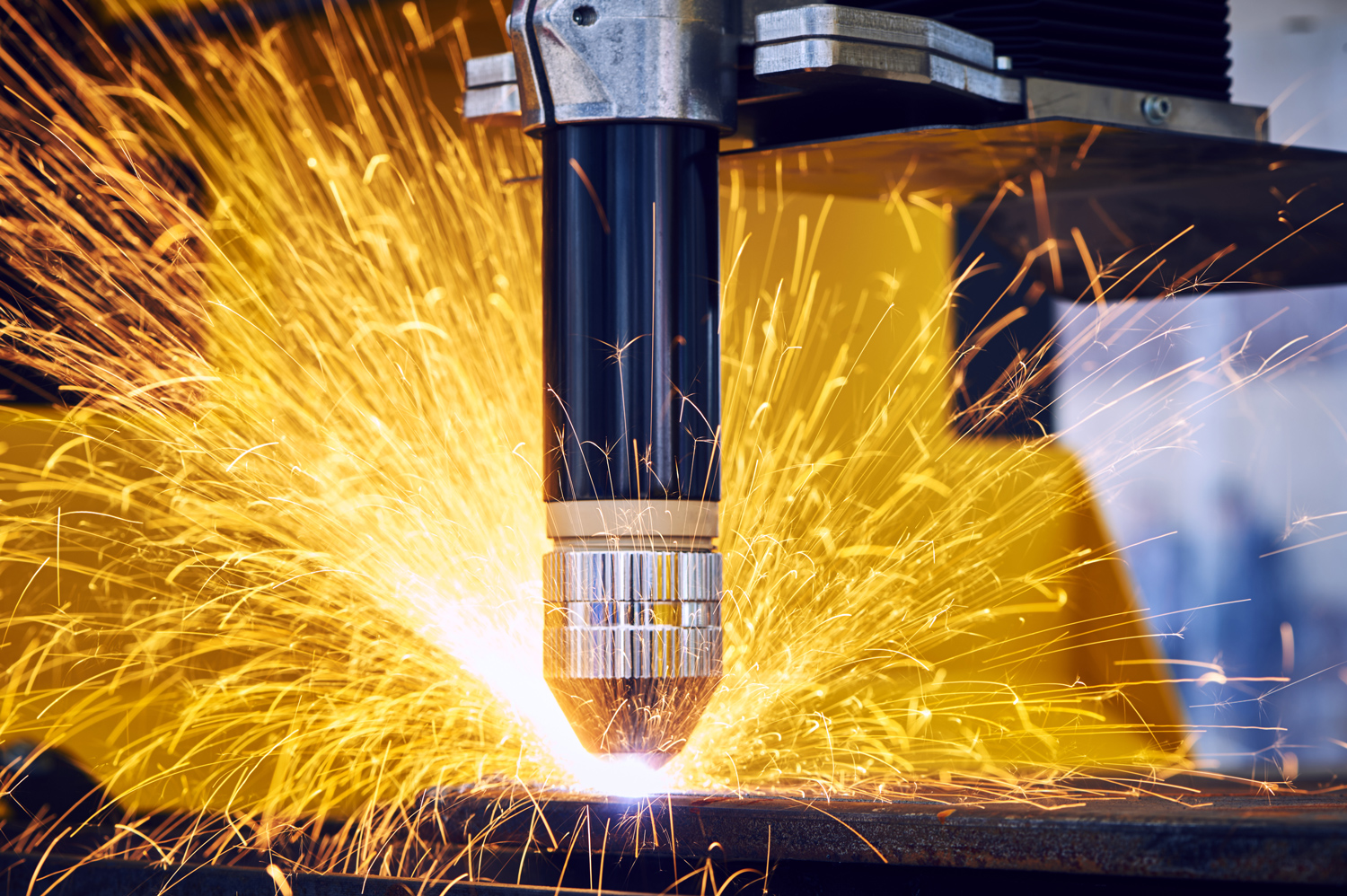
Cięcie plazmą – poradnik
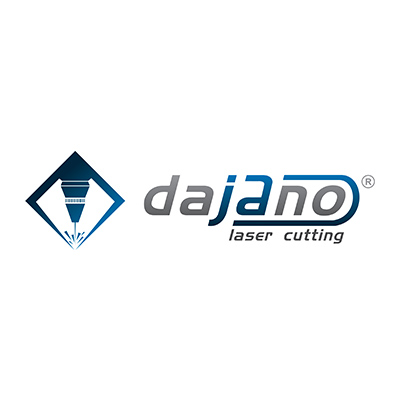
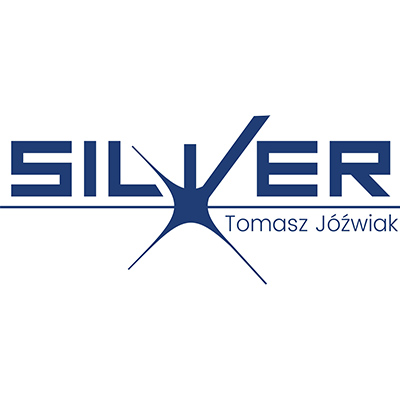
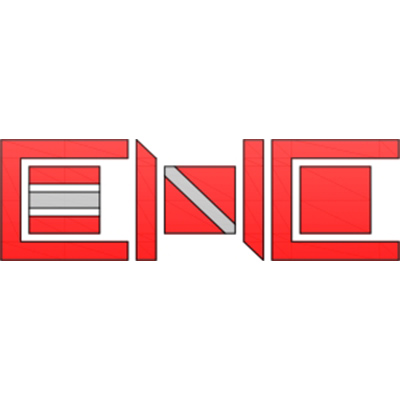
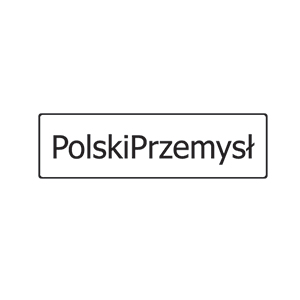
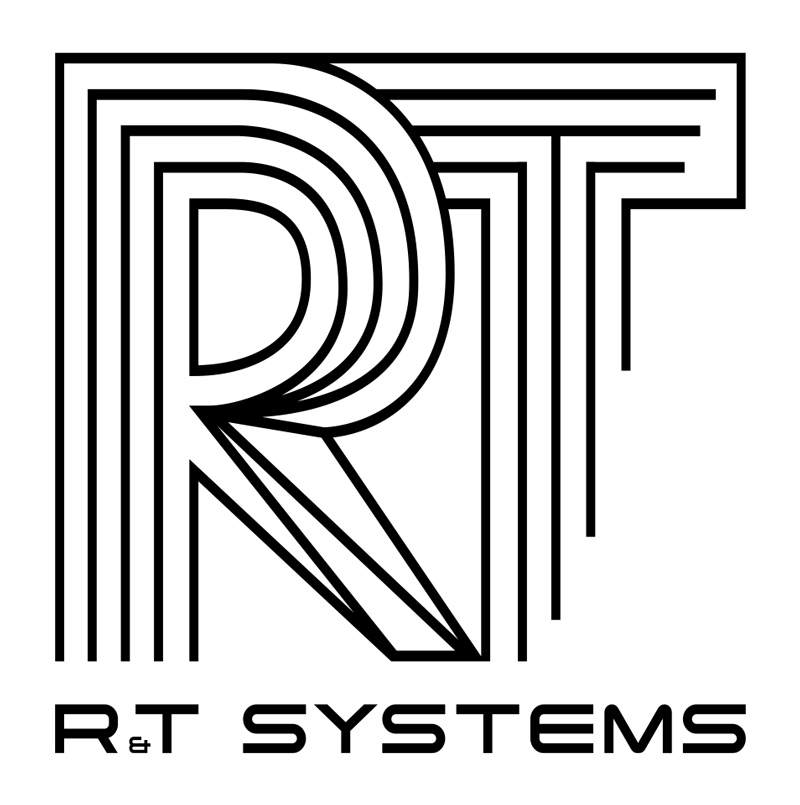
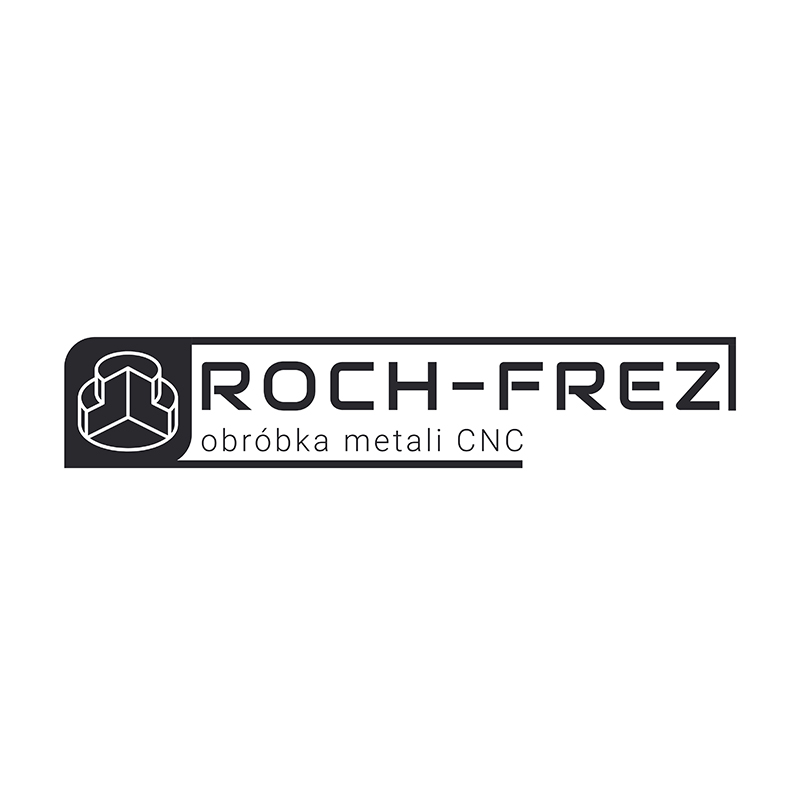
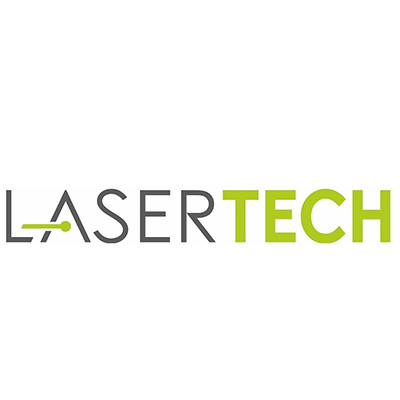
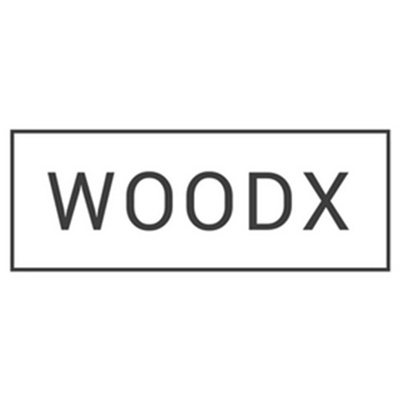
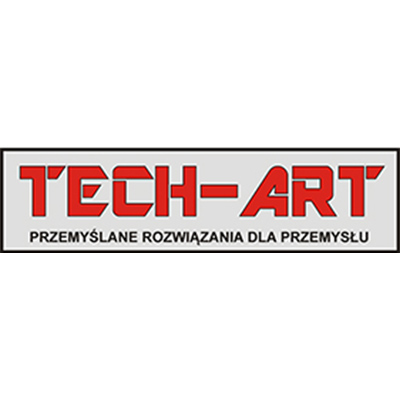
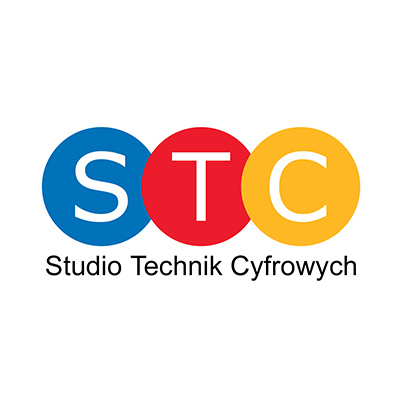
Cięcie plazmą.
Cięcie plazmą – ten rodzaj cięcia znalazł swoje zastosowanie w przemyśle już w latach 50. ubiegłego wieku. Ciągły rozwój i nieustanne udoskonalanie technologii plazmowej sprawiły, że zakres ciętych materiałów, ich grubości oraz prędkości cięcia znacząco wzrosły i stały się dużo wydajniejsze niż jakiś czas temu.
Cięcie plazmą wykorzystywane jest w wielu gałęziach przemysłu. Sprawdza się głównie tam, gdzie potrzebna jest dobra jakość cięcia i stosunkowo korzystny współczynnik ceny do jakości. Cięcie plazmą z powodzeniem zastępuje proces cięcia tlenowo–gazowego stali stopowych, z uwagi na znacznie niższe koszty eksploatacyjne w przypadku materiałów o grubości do 30 mm. Idealnie sprawdza się przy cięciu materiałów przewodzących prąd elektryczny – o grubości nawet do 150 mm.
Czym jest plazma?
Plazma jest zjonizowaną materią o stanie skupienia przypominającym gaz. Z uwagi na swoje specyficzne właściwości czasami nazywana jest czwartym stanem materii, aczkolwiek z racji tego, że ponad 99,99% materii składa się właśnie z tej substancji, powinna być nazywana pierwszym stanem skupienia. Złożona jest zarówno z cząstek naładowanych elektrycznie, jak i obojętnych. W plazmie współwystępują zjonizowane atomy oraz elektrony, jednak cała objętość zajmowana przez plazmę jest elektrycznie obojętna.
Z uwagi na obecność dużej ilości jonów o różnym ładunku oraz swobodnych elektronów, plazma przewodzi prąd elektryczny, jednak jej opór – inaczej niż w przypadku metali – maleje wraz ze wzrostem temperatury. Gdy natężenie przepływającego prądu osiągnie odpowiednio wysoką wartość, plazma emituje energię w postaci światła i ciepła.
W zależności od natężenia przepływającego prądu w plazmie możemy wyróżnić trzy jej stany:
- przy bardzo małym natężeniu prądu nie widać świecenia (czarny prąd),
- przy większym natężeniu zaczyna ona wytwarzać światło – i jest to zjawisko, które znamy z lamp jarzeniowych,
- przy wzroście natężenia prądu i przekroczeniu pewnej granicy wartości powstaje łuk elektryczny – i tę właśnie właściwość wykorzystuje cięcie plazmą i spawanie plazmą.
Cięcie plazmą – na czym polega?
Jak ciąć plazmą?
Cięcie plazmą wykorzystuje źródło ciepła w postaci silnie skoncentrowanego łuku elektrycznego o dużej energii kinetycznej, jarzącego się pomiędzy ciętym materiałem a nietopliwą elektrodą, umieszczoną w uchwycie plazmowym.
Odpowiednią koncentrację łuku otrzymuje się za pomocą specjalnej dyszy, zwanej dyszą plazmową (dyszą tnącą). W zależności od natężenia prądu cięcia, stosowane są dysze plazmowe o różnej średnicy. Najczęściej spotykanym przedziałem średnic dysz tnących jest przedział od 0,6 mm do 2,0 mm. Zadaniem dyszy tnącej jest koncentracja ciepła na niewielkiej powierzchni materiału, co powoduje znaczny wzrost stopnia jonizacji przepływającego gazu plazmowego. Chłodzone ścianki dyszy powodują zawężanie kolumny łuku. Dzięki dużemu zagęszczeniu mocy wytwarza się uformowany strumień plazmy, który ze względu na temperaturę sięgającą kilkunastu tysięcy stopni Celsjusza oraz dużą prędkość z łatwością przetapia i przedmuchuje metal, wyrzucając materiał ze szczeliny cięcia.
Plazmowy łuk elektryczny jest silnie zjonizowanym gazem, przemieszczającym się z dyszy plazmowej z prędkością bliską prędkości dźwięku. Temperatura wiązki plazmy oscyluje wokół wartości 10 000–30 000 K i zależna jest od natężenia prądu oraz rodzaju i składu gazu plazmowego. Dzięki dużej energii cieplnej łuku plazmowego cięcie plazmą CNC może być realizowane w szerokim zakresie prędkości.
Cięcie plazmowe wykorzystuje prąd stały o biegunowości ujemnej. Uchwyt masowy podłączony jest więc do bieguna dodatniego, a plazmowy do bieguna ujemnego. Zajarzenie łuku plazmowego odbywa się poprzez potarcie dyszy tnącej o materiał cięty (rozwiązanie starsze technologicznie) lub przez wykorzystanie tzw. łuku pilotażowego, jarzącego się między elektrodą a dyszą plazmową. Łuk ten powstaje dzięki wykorzystaniu krótkich impulsów o wysokim napięciu, wytwarzanym w jonizatorze wysokiej częstotliwości. Wykorzystanie łuku pilotażowego znacznie ułatwia przebieg procesu cięcia. Umożliwia wstępne nadtopienie brzegów ciętego materiału, rozpoczynanie procesu cięcia w dowolnym położeniu palnika tnącego.
Plazma tworzona jest za pomocą palnika do cięcia plazmą. Palnik może być prowadzony przez operatora ręcznie lub w sposób zautomatyzowany.
Cięcie plazmą – rodzaje palników plazmowych.
- palniki z łukiem wewnętrznym (niezależnym) – są one mniej wydajne, ze względu na duże odprowadzanie ciepła przez dyszę chłodzoną wodą; stosowane głównie do cięcia materiałów nieprzewodzących prądu elektrycznego i do cięcia cienkich blach, jak również do metalizacji,
- palniki z łukiem zewnętrznym (zależnym) – powszechnie stosowane; podobnie jak przy palnikach do spawania, w palnikach do cięcia łuk pomocniczy umożliwia zajarzenie łuku głównego; zajarzenie się łuku pomocniczego odbywa się w osłonie gazu Ar (argonu), ale proces cięcia realizowany jest najczęściej przy użyciu gazów plazmowych.
Powszechnie stosowanym gazem plazmotwórczym jest powietrze. W urządzeniach o dużych mocach z reguły używa się argonu, azotu, wodoru, dwutlenku węgla oraz mieszanki argon–wodór i argon–hel.
Strumień plazmy umożliwia cięcie materiałów przewodzących prąd elektryczny – wykonanych ze stali węglowych i stopowych, aluminium i jego stopów, mosiądzu, miedzi oraz żeliwa.
Z czego składa się system plazmowy?
W konwencjonalnym systemie plazmowym wyróżnić można cztery podstawowe elementy:
- źródło zasilania (potocznie nazywane źródłem plazmowym),
- palnik plazmowy,
- przewód uziemiający,
- części eksploatacyjne.
Jeśli mamy do czynienia z systemami plazmowymi wąskostrumieniowymi (potocznie zwanymi plazmami HD), dochodzą do tego jeszcze konsole gazowe, służące do dozowania i miksowania gazów technicznych.
Aby system plazmowy działał sprawnie, potrzebne jest zasilanie elektryczne oraz gaz. W systemach konwencjonalnych w roli gazu plazmowego oraz osłonowego zwykle wykorzystuje się powietrze podawane z kompresora lub butli. Systemy plazmowe wąskostrumieniowe dają możliwość zastosowania gazów technicznych, takich jak: tlen, azot, argon.
Cięcie plazmą – parametry.
Do podstawowych parametrów, które mają wpływ na cięcie plazmą i przebieg procesu, zaliczamy:
- natężenie prądu cięcia – decyduje o temperaturze i energii łuku plazmowego, wraz ze wzrostem natężenia prądu zwiększa się również prędkość cięcia lub grubość przecinanego materiału,
- napięcie łuku plazmowego – decyduje o sprawnym przebiegu procesów cięcia plazmowego, wynosi od 50 do 200 V,
- prędkość cięcia (prowadzenia palnika plazmowego) – dobierana do natężenia prądu i grubości ciętego materiału,
- grubość cięcia – do której należy dopasować natężenie prądu i prędkość cięcia; dla poszczególnych materiałów grubości cięcia wynoszą:
– stal konstrukcyjna: 0,5–30 mm (cięcie jakościowe), 20 mm (przebicie produkcyjne),
– stal nierdzewna: 0,8–20 mm (cięcie jakościowe), 16 mm (przebicie produkcyjne),
– aluminium: 1,2–25 mm (cięcie jakościowe), 16 mm (przebicie produkcyjne), - odległość palnika od ciętego materiału – powinna być dobrana tak, aby pozwoliło to na zachowanie odpowiedniej jakości cięcia, nie uszkadzając przy tym dyszy plazmowej,
- rodzaj, ciśnienie i natężenie przepływu gazu plazmowego – prędkość wypływu strumienia plazmy z palnika oraz temperatura zależą od natężenia prądu, średnicy i kształtu, jaką osiąga dysza plazmowa,
- rodzaj i konstrukcja elektrody,
- średnica dyszy tnącej,
- położenie palnika względem ciętego przedmiotu – palnik powinien być prowadzony prostopadle do ciętej powierzchni.
Rodzaj gazu plazmowego, ciśnienie i natężenie przepływu prądu, rodzaj i konstrukcja elektrody oraz dyszy tnącej – to czynniki wynikające z konstrukcji urządzenia i uchwytu plazmowego, a zatem ustalane są przez producenta.
Napięcie łuku plazmowego zależy od rodzaju gazu plazmowego, konstrukcji urządzenia, natężenia prądu cięcia oraz odległości palnika uchwytu od ciętego materiału. Zależność między napięciem łuku plazmowego a odległością palnika plazmowego wykorzystywana jest w przecinarkach plazmowych sterowanych numerycznie (regulacja odległości palnika w trakcie cięcia). Przy dobieraniu właściwych parametrów procesu cięcia zawsze należy kierować się zaleceniami umieszczonymi w dokumentacji techniczno-rozruchowej urządzenia.
Do parametrów, które regulowane mogą być przez operatora – a ich dobór uzależniony jest między innymi od rodzaju i grubości ciętego materiału – zaliczamy:
- natężenie prądu cięcia,
- prędkość cięcia,
- odległość palnika plazmowego od ciętego materiału.
Natężenie prądu cięcia – to główny parametr, mający wpływ na zakres grubości cięcia, wydajność i efektywność procesu. Im wyższe jest jego natężenie, tym większa grubość i prędkość cięcia. Jego wyższe wartości wymagają stosowania dyszy tnącej o większej średnicy, co wpływa na powstawanie szerszej szczeliny cięcia. Jeśli dla materiału o określonej grubości zwiększymy natężenie prądu tnącego, zwiększy się szybkość oraz wydajność cięcia. Należy przy tym pamiętać, że zbyt wysokie natężenie prądu cięcia dla grubości materiału może skutkować nadmiernym miejscowym przegrzaniem się materiału i powstawaniem naprężeń oraz odkształceń cieplnych.
Dla ustalonej wartości natężenia prądu cięcia można zastosować szeroki zakres prędkości cięcia. Warto przy tym pamiętać, że zbyt mała prędkość cięcia może być powodem przerywania łuku plazmowego (łuk gaśnie i ponownie się zajarza), co prowadzi do szybszego zużycia dysz i elektrod. Powstają wówczas nacieki usuwanego metalu i duża ilość przylegającego żużlu. Przy zbyt niskiej prędkości cięcia strumień plazmy układa się osiowo w stosunku do elektrody (im niższa prędkość cięcia, tym bardziej zbliżamy się do współosiowości). Z kolei zbyt duża prędkość cięcia powoduje powstawanie dużego ukosu powierzchni cięcia, dużych ilości zalegającego żużlu, a nawet niecałkowite przebicie się przez cięty materiał (czyli: nieprzecięty materiał). Im większą prędkość wykorzystuje cięcie plazmą, tym płomień plazmowy bardziej zbliża się ku prostopadłości względem elektrody.
Przyjmuje się, że cięcie plazmą ma optymalną prędkość wówczas, gdy strumień plazmy układa się pod kątem 45⁰ względem elektrody.
Odległość uchwytu plazmowego (palnika plazmowego) od ciętego materiału to parametr mający bardzo duże znaczenie dla przebiegu procesu cięcia. Odległość powinna być tak dobrana, ażeby cięcie plazmą nie uszkodziło dyszy plazmowej, przy jednoczesnym zachowaniu odpowiedniej jakości cięcia. Zbyt bliska odległość palnika doprowadzić może do uszkodzenia dyszy tnącej oraz spowodować nadtopienie górnej krawędzi ciętego materiału. Zbyt duża odległość to ryzyko powstawania nadmiernego ukosu powierzchni cięcia i tworzenia się dużej ilości żużlu na dolnej krawędzi cięcia. Powstały żużel jest trudny do usunięcia. Producenci uchwytów plazmowych przewidują użycie specjalnych dystansów, kompatybilnych z ich uchwytami – bardzo często w postaci specjalnych sanek drucianych lub sanek na drobnych kołach jezdnych (mogą to być również inne rozwiązania), dzięki czemu operator ma możliwość utrzymania odpowiedniej odległości dyszy od ciętego materiału. Najczęstszym błędem, spotykanym w przypadku ręcznego cięcia plazmą, jest właśnie cięcie bez dystansu (trzymanie palnika w powietrzu, ciągnięcie dyszą tnącą po ciętym materiale). Taka technika cięcia jest niedopuszczalna, wywiera negatywny wpływ na przebieg procesu, wpływa na szybsze zużycie się elementów eksploatacyjnych uchwytów, może powodować cofanie się płomienia plazmowego do palnika oraz uszkodzenie palnika.
Cięcie plazmą – metody i typy cięcia.
Przy użyciu palnika plazmowego wykonywać można cięcie plazmą przeróżnego typu. Najpopularniejszymi z nich są:
- cięcie plazmą podstawowe – czyli zwykłe rozcinanie elementu obrabianego od krawędzi,
- cięcie plazmą szablonowe – w przypadku cięcia tego typu przebijamy się w środku obrabianego elementu, a następnie prowadzimy palnik (podobnie jak przy cięciu podstawowym) wzdłuż wcześniej przygotowanego szablonu,
- cięcie plazmą poprzez ukosowanie – cięcie plazmą tego typu polega na tym, że palnik pochylamy pod odpowiednim kątem, tak aby po odcięciu otrzymać pochyloną krawędź,
- cięcie plazmą poprzez żłobienie – dzięki zastosowaniu specjalnych części eksploatacyjnych, możliwe jest tworzenie regularnych wyżłobień w obrabianym materiale; pozwala to usunąć np. wadliwy spaw lub rozdzielić wcześniej zespawane elementy; podczas żłobienia palnik skierowany jest pod kątem ostrym w stosunku do obrabianej powierzchni, dzięki czemu stopiony materiał jest wydmuchiwany na zewnątrz bez przecinania materiału; korzyści stosowania żłobienia plazmowego to: redukcja hałasu i dymów w porównaniu z innymi cieplnymi metodami żłobienia, wysoka precyzja, duża wydajność i czystość usuwania metalu, redukcja ryzyka nawęglania w porównaniu z procesem żłobienia łukiem elektrycznym, możliwość żłobienia metali żelaznych i nieżelaznych,
- cięcie plazmą wielu blach jednocześnie – możliwe jest po uprzednim ułożeniu ich w stos,
- cięcie plazmą zmechanizowane – możliwe jest po zainstalowaniu systemu na stole CNC.
Cięcie plazmą – zastosowania.
Do cięcia plazmowego całe ciepło wymagane do stopienia materiału powinno pochodzić tylko z łuku plazmowego, co powoduje, że grubość blachy podlegającej cięciu jest ograniczona. Rozróżnia się łuk przenoszony i nieprzenoszony. Przy łuku przenoszonym cięty materiał – jako że stanowi część obwodu elektrycznego – powinien przewodzić prąd elektryczny. Jest to metoda odpowiednia do cięcia zarówno materiału o niewielkiej, jak i o dużej grubości blachy. Stosowany gaz plazmowy decyduje o przenoszeniu energii. W przypadku cięcia za pomocą łuku nieprzenoszonego materiał nie stanowi elementu obwodu łuku elektrycznego. Cięcie plazmą za pomocą łuku nieprzenoszonego jest odpowiednie tylko do cięcia z niskimi osiągami, jako że dysza plazmowa spełnia funkcję anody.
Cięcie plazmą – co mu podlega? Otóż cięciu podlegają prawie wszystkie topliwe i przewodzące prąd elektryczny metale – stal węglowa i stopowa, czarna, nierdzewna, stale miękkie, aluminium.
Cięcie plazmą to metoda ekonomiczna i dobra jakościowo dla materiałów ze stali konstrukcyjnej o grubości poniżej 30 mm, stali stopowej i kolorówki.
W zależności od źródła mocy, ręczne systemy plazmowe są zdolne do rozcinania blach o grubości do 75 mm. Zaawansowane systemy wysokoamperażowe potrafią rozciąć nawet do 160 mm.
Cięcie plazmą zardzewiałych, pomalowanych czy zabrudzonych powierzchni nie wymaga wcześniejszego czyszczenia. Do prawidłowej pracy przecinarki plazmowej niezbędny jest jedynie dobry kontakt elektryczny przewodu masowego z ciętym materiałem. Plazmą można ciąć blachy, kształtowniki, rury oraz siatki.
Systemy plazmowe z powodzeniem instaluje się również na stołach CNC oraz robotach.
Cięcie plazmą – 10 najczęściej popełnianych błędów.
Dobry operator, umiejętnie dysponujący serwisowanym systemem PAC, to dla firmy większe zyski z operacji cięcia oraz lepsza rentowność. Niekiedy pozwala to zaoszczędzić naprawdę wielu wydatków operacyjnych oraz godzin przestojowych.
Cięcie plazmą – jakich błędów unika dobry operator?
1 – Używanie materiałów eksploatacyjnych do ich wydmuchania
Używanie bardzo zużytych materiałów eksploatacyjnych, do samego końca ich trwałości, prowadzić może nie tylko do zniszczenia dobrego arkusza metalu, ale także poskutkować kosztowną usterką palnika i niepotrzebnym czasem przestoju w pracy. Zużycie materiału można rozpoznać na kilka sposobów: na podstawie wydawanego dźwięku, koloru łuku albo subtelnych zmian w wysokości palnika. Najlepszą metodą oceny stanu części palnika jest okresowe sprawdzanie jakości ciętej krawędzi metalu oraz kontrolowanie części palnika, gdy jakość ta ulega pogorszeniu. Przydatne w tym celu jest prowadzenie dokumentacji zmieniającej się w czasie średniej trwałości części eksploatacyjnej (wyrażonej w liczbie startów lub czasu pracy łuku) oraz opracowanie wytycznych oczekiwanej trwałości na bazie natężenia prądu, materiału i grubości.
2 – Zmiana materiałów eksploatacyjnych
Nie jest dobrze również, gdy materiały eksploatacyjne wymieniane są zbyt często. Nie jest bezwzględną koniecznością wymiana ich po upływie zdefiniowanej liczby godzin. Znacznie korzystniej jest, gdy operator bacznie przygląda się stopniowi ich zużycia. Czy na wewnętrznej lub zewnętrznej powierzchni dyszy widoczne są wgłębienia? Czy końcówka jest już za okrągła? TAK? Materiał nadaje się do wymiany! NIE? Nadal można z niego korzystać, nawet gdy zdefiniowana liczba godzin już upłynęła.
Jeśli wgłębienie na samym środku wkładki z hafnu jest już zbyt duże – elektroda jest zużyta, jeśli nie – można korzystać z niej nadal. Jeśli kontrola pierścieni zawirowujących gaz wykazuje obecność brudu lub smaru w otworach, pęknięcia, przepalenia łuku, nadmierne zużycie – powinny być one wymienione, w przeciwnym wypadku niechaj nadal służą. Jeśli osłony wykazują objawy uszkodzeń fizycznych – czas na ich zmianę, ale jeśli da się je wyczyścić z odprysków metalu, mogą ponownie być używane.
3 – Stosowanie nieprawidłowych parametrów i części
Materiał eksploatacyjny dobieramy w zależności od ciętego materiału i jego grubości, natężenia prądu i gazu plazmowego oraz innych parametrów cięcia. Stosowanie nieodpowiednich materiałów eksploatacyjnych skutkować może zmniejszeniem trwałości części oraz pogorszeniem jakości cięcia. Informacje o właściwych materiałach, pasujących do różnych prac cięcia, znajdują się w podręczniku operatora.
Bardzo ważne jest używanie części przy odpowiednim natężeniu prądu. Najlepszą jakość cięcia oraz trwałość części eksploatacyjnych uzyskuje się zwykle wówczas, gdy natężenie prądu jest ustawione na 95% wartości znamionowej dyszy. Gdy prąd będzie zbyt mały, cięcie będzie niedoskonałe, a gdy zbyt duży – ucierpi trwałość dyszy.
4 – Nieprawidłowe zmontowanie palnika
Palnik musi być zmontowany w taki sposób, aby wszystkie części dokładnie do siebie pasowały i były prawidłowo wyosiowane, dopiero wtedy można uzyskać dobry styk elektryczny oraz prawidłowy przepływ gazu i płynu chłodzącego przez palnik. Podczas wymiany części materiały eksploatacyjne należy trzymać na czystej szmacie warsztatowej, żeby zapobiec zanieczyszczeniu palnika brudem i pyłem metalicznym. Bardzo ważne – ale często zaniedbywane – jest zachowanie czystości podczas montażu palnika. Podczas smarowania pierścienia uszczelniającego o przekroju okrągłym należy nałożyć tylko tyle smaru, aby pierścień błyszczał. Za duża jego ilość może skutkować zapychaniem elementu zawirowującego gaz oraz zanieczyszczeniem palnika pyłem mechanicznym – co może doprowadzić do niekontrolowanego zapłonu łuku w komorze plazmy i ewentualnego uszkodzenia palnika. Nigdy nie nakładamy też smaru na palniki – to również może być przyczyną szkodliwego zapłonu łuku albo zapłonu wewnątrz palnika.
5 – Zaniedbywanie rutynowej konserwacji
Przy odpowiedniej, systematycznej dbałości o palniki, mogą one wytrzymać nie tylko miesiące, ale nawet i lata pracy. Gwinty powinny być zawsze czyste, a powierzchnie montażowe kontrolowane pod kątem zanieczyszczeń i uszkodzeń mechanicznych. Wszelki brud, pył metaliczny i nadmiar smaru na pierścieniu uszczelniającym o przekroju okrągłym należy usuwać. Do czyszczenia palnika powinno się używać bawełnianego wacika oraz środka do czyszczenia styków elektrycznych lub nadtlenku wodoru.
6 – Niesprawdzanie przepływu płynu chłodzącego i przepływu gazu
Należy pamiętać o codziennym sprawdzaniu przepływu i ciśnienia gazu oraz płynu chłodzącego. Przy niedostatecznym przepływie materiały eksploatacyjne będą nienależycie chłodzone, przez co ich trwałość będzie zmniejszona. Bardzo częstą przyczyną uszkodzenia części i palnika jest właśnie nieprawidłowy przepływ chłodziwa, wynikający ze zużycia pompy, zapchania filtrów, niskiego poziomu płynu chłodzącego itd. Aby utrzymać łuk tnący, należy zachować stałe ciśnienie gazu. Zbyt wysokie ciśnienie gazu to częsta przyczyna „trudnego rozruchu”, czyli sytuacji, w której palnik nie może zapalić łuku, choć wszystkie pozostałe warunki prawidłowej pracy są spełnione. Za duże ciśnienie gazu skutkuje też gwałtownym zużywaniem się elektrody. Aby zapobiec zmniejszeniu trwałości materiałów eksploatacyjnych i palnika, również gaz plazmowy musi być utrzymywany w czystości. Systemy sprężonego powietrza szczególnie narażone są na zanieczyszczenie olejem, wilgocią i cząstkami.
7 – Przebijanie zbyt nisko
Krytyczne znaczenie pod względem jakości cięcia oraz trwałości części eksploatacyjnych ma odsunięcie palnika, czyli odległość od końcówki dyszy do elementu obrabianego. Nawet niewielkie odchylenie wysokości palnika może mieć wpływ na kątowość ciętej powierzchni. Szczególnie ważna podczas przebijania jest wysokość palnika. Często popełnianym błędem jest przebijanie zbyt nisko – wówczas stopiony metal rozpryskuje się z przodu dyszy i osłony, powodując uszkodzenie części i związane z tym problemy z jakością cięcia. Jeżeli palnik przebija po dotknięciu metal albo jest przeciągany wzdłuż powierzchni podczas cięcia, dochodzić może nawet do „gaśnięcia” łuku. A jeżeli łuk „gaśnie”, może to doprowadzić do uszkodzenia elektrody, dyszy, elementu zawirowującego, a nawet palnika. Palnik oraz części chroni przed uszkodzeniem przebijanie na wysokości 1,5–2 razy wyższej niż zalecana.
8 – Cięcie zbyt szybko lub zbyt wolno
Zbyt szybkie lub zbyt wolne cięcie kończy się problemami z jakością cięcia. Przy zbyt małej szybkości na odciętych fragmentach pojawia się „żużel wolnobieżny”, czyli nagromadzenie grudek żużlu wzdłuż dolnej krawędzi. Możemy mieć także do czynienia z poszerzeniem szczeliny oraz powstawaniem nadmiernej ilości rozprysków na górze. Natomiast przy zbyt dużej szybkości łuk opóźnia się w szczelinie, powodując niezamierzone ukosowanie krawędzi, wąską szczelinę oraz małe i twarde grudki żużlu wzdłuż dolnej krawędzi odcinanego fragmentu. Taki „szybkobieżny żużel” jest niezwykle trudny do usunięcia. Jeżeli prawidłowo dobierzemy szybkość cięcia, ilość żużlu będzie minimalna, a czysta krawędź nie będzie wymagała żadnej obróbki końcowej przed przekazaniem do dalszych etapów produkcji.
9 – „Rozciąganie” łuku
Rozciąganie łuku następuje na początku i na końcu cięcia, gdy łuk musi się „rozciągnąć” (czyli odchylić od prostej, prostopadłej ścieżki) w celu odnalezienia metalu. Rozciąganie może skutkować cięciem przez łuk bocznych ścianek dyszy. Podczas startu od krawędzi łuk plazmowy powinien być aktywowany, gdy otwór dyszy jest wyśrodkowany dokładnie nad krawędzią obrabianego elementu – trzeba o tym pamiętać podczas operacji przebijania przebijarką/plazmą, gdy łuk jest uruchamiany od przebitego otworu. W tym zastosowaniu łuk należy uruchomić od krawędzi, a nie od środka przebitego otworu. Rozciągnięcie może nastąpić również na końcu cięcia, gdy palnik jest zaprogramowany do przejścia za płytę z włączonym łukiem albo gdy „wyprowadzenie cięcia” podąża za szczeliną uprzednio odciętego metalu. Aby zminimalizować ten efekt, można zmienić moment wysyłania sygnału wyłączenia łuku oraz sposób programowania wyprowadzenia cięcia.
10 – Zderzenie palnika
Nieodwracalne uszkodzenia palnika mogą się pojawić w wyniku upadków i zderzeń. Zapobiec kolizjom palnika z elementem obrabianym można, programując system cięcia kształtów w taki sposób, aby palnik przemieszczał się wokół ciętych części (a nie nad nimi). Czujniki wysokości palnika często chronią przed zderzeniami palnika, uwzględniając zmianę charakterystyki materiału. Jednakże kontrolery wysokości z regulacją napięcia nie dają gwarancji całkowitej ochrony palnika. Przykładowo na końcu cięcia występuje często „nurkowanie palnika”, gdy palnik podąża zbyt długo za szczeliną. Kontroler wysokości palnika zmniejsza wysokość, aby skompensować wzrost napięcia towarzyszący rozciągnięciu łuku. W celu zminimalizowania tego efektu można zmienić program wyprowadzenia cięcia oraz parametry kontrolera wysokości palnika. W zapobieganiu uszkodzeniom palnika wynikającym ze zderzenia, pomagają też urządzenia mocujące palnik z funkcją odłączenia.
Cięcie plazmą – zalety i wady.
Wśród głównych KORZYŚCI ze stosowania technologii plazmowej na szczególną uwagę zasługują następujące cechy użytkowe:
- cięcie plazmą to znaczne prędkości – 5 do 7 razy większe niż w przypadku cięcia tlenowo–gazowego,
- cięcie bez podgrzewania, szybkie przebijanie,
- wąska strefa wpływu cięcia, małe odkształcenia cieplne – dzięki silnie skoncentrowanemu działaniu temperatury i dużym prędkościom cięcia mamy do czynienia ze stosunkowo niewielkim wpływem temperatury na cały materiał,
- niewielka szczelina cięcia,
- dobra jakość powierzchni cięcia (możliwość uzyskania doskonałej, lustrzanej powierzchni krawędzi z agregatami plazmowymi klasy XD),
- możliwość cięcia bez nadpalania materiałów cienkich,
- duży zakres grubości cięcia – od 0,5 mm do 160 mm,
- skuteczne cięcie plazmą w pionie i ukosowanie stali konstrukcyjnej o grubości do 30 mm,
- łatwa automatyzacja procesu cięcia,
- bardzo duże tempo produkcji z blachy cienkiej po właściwym ustawieniu i zaprogramowaniu,
- relatywnie niski koszt inwestycji.
Optymalny dobór gazów plazmowych i parametrów cięcia pozwalają uzyskać bardzo dobrą jakość przeciętej powierzchni, praktycznie zerową ilość zgorzeliny oraz wysoką powtarzalność elementów. Automatyczne ustawienie elementów na blasze lub rurze (Nesting) minimalizuje ilość odpadów.
Cięcie blach plazmą (cięcie łukiem plazmowym) nie jest jednak pozbawione WAD, a wśród nich warto wymienić:
- duży hałas (z wyjątkiem cięcia pod wodą),
- silne promieniowanie UV,
- duża ilość gazów i dymów szkodliwych dla zdrowia (problem ten rozwiązuje System Inteligentnego Sterowania Stołami Sekcyjnymi),
- zmiany w strefie wpływu cięcia,
- trudności w utrzymaniu prostopadłości krawędzi (problem rozwiązuje plazma High Definition).
Technologia obróbki plazmowej (plazmowe cięcie) funkcjonuje w przemyśle już od ponad 50 lat. Pomimo wielu mitów o cięciu plazmowym, jakie przez ten czas się utrwaliły, warto wprowadzić w zakładach produkcyjnych to rozwiązanie, jeśli tylko jest taka potrzeba i zapotrzebowanie na tego typu usługi. Gwarantuje ono dobre efekty pracy przy jednoczesnej oszczędności czasu i niskich kosztach.
W jednym miejscu skupiamy profesjonalne firmy z różnych dziedzin. Wykonasz tu cięcie laserem, cięcie plazmą, wodą i tlenem.
Zapraszamy do współpracy!
Tagi: plazma do cięcia, plazma cięcie, ciecie plazma, plazmowe cięcie.